When choosing anti-static protection, you'll find both temporary and permanent solutions available. Temporary solutions, like surface coatings and sprays, work with ambient moisture and need regular reapplication but are cost-effective for short-term needs. Permanent solutions form conductive networks within materials, offering lasting protection without humidity dependence and maintaining effectiveness even after repeated washing. While temporary options might suit basic packaging needs, permanent solutions excel in sensitive environments like electronics manufacturing and medical facilities. Your specific application requirements, budget, and environmental conditions will guide you toward the best protection strategy.
Understanding Anti-Static Protection Types
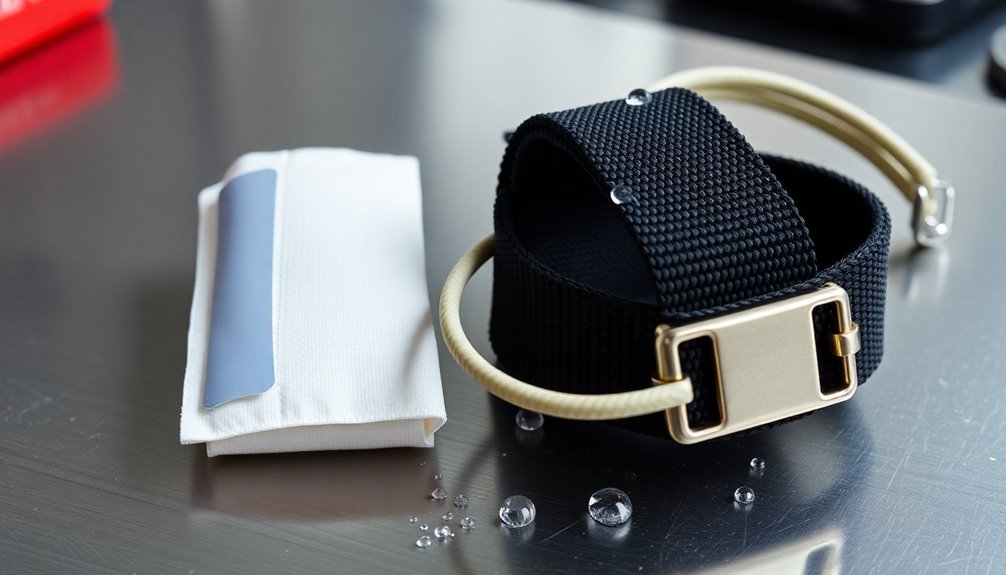
Static electricity poses significant risks in various industries, particularly when handling sensitive electronic components or managing critical manufacturing processes. When you're looking for reliable protection against static buildup, permanent anti-static solutions offer distinct advantages over temporary alternatives.
These permanent solutions work by forming continuous 3D networks within polymer structures, creating a lasting defense that won't migrate or wear off over time. Loading levels of 5-10 weight percent are typically sufficient for effective anti-dust properties.
You'll find they're not dependent on humidity levels, unlike many traditional anti-static treatments, making them effective even in dry environments. They're especially valuable in automotive interiors, electronic device packaging, and clean room surfaces where consistent protection is vital.
Products like ADK STAB AS-300, Pebax®, and PELESTAT offer superior performance while maintaining the host material's physical properties.
You can easily color these solutions without compromising their effectiveness, unlike carbon-based alternatives. Their low ionic content and minimal outgassing make them ideal for sensitive applications in medical devices and electronics packaging.
When you need to prevent electrostatic discharge (ESD) in critical environments, these permanent solutions provide immediate, reliable protection that won't diminish over time, ensuring consistent performance throughout the product's lifecycle.
Temporary Solutions and Their Applications
You'll find temporary anti-static solutions particularly effective for quick surface applications where immediate static control is needed.
These solutions, which include migrating additives like Atmer™ 129, move to the material's surface and work with ambient moisture to dissipate static charge. They provide up to 12 months of effective static control performance.
For industrial short-term protection, you can apply these solutions through various methods including surface coatings, masterbatches, or concentrates, depending on your specific application requirements.
Quick Surface Applications
Prevention of static buildup often requires immediate, short-term solutions that you can quickly apply to surfaces.
You'll find various temporary treatments available as liquids, sprays, or wipes, making them ideal for rapid deployment in packaging and shipping scenarios. These solutions work particularly well with plastics and electronics, though you'll need to plan for periodic reapplication. Maintaining relative humidity above 60% helps extend the effectiveness of these treatments.
When you're selecting a quick surface treatment, you'll encounter several options, including topical anti-static coatings, conductive paints, and specialized wipes. These treatments are particularly useful in electronics packaging, medical supplies, and handling static-sensitive components.
You'll want to take into account the specific requirements of your application, as different materials may require different treatment approaches.
The effectiveness of your chosen treatment will depend heavily on environmental conditions, particularly humidity levels and surface cleanliness. You'll achieve the best results by properly cleaning surfaces before application and maintaining appropriate environmental conditions.
Remember that these temporary solutions don't provide permanent protection – you'll need to monitor their performance and reapply as needed. For shipping and short-term storage applications, anti-static bags offer a convenient solution that you can implement quickly.
Industrial Short-Term Protection
Industrial environments demand flexible approaches to static control, and temporary solutions often prove invaluable for short-term protection needs.
Handheld meters can accurately measure static levels up to 200kV, allowing you to monitor the effectiveness of temporary protection solutions and make adjustments as needed.
You'll find migrating static control additives particularly effective for applications lasting up to 12 months, especially in food and cosmetic packaging scenarios. These additives work by moving to the polymer's surface and attracting moisture, effectively reducing static build-up without compromising clarity or mechanical properties.
When you're working with temporary static control solutions, you'll notice they're easy to implement through masterbatches or concentrates in both extrusion and injection molding processes. Products like Atmer™ 129 deliver cost-effective protection while maintaining essential material properties.
- Requires minimal addition levels for effective static control
- Works efficiently in humidity-dependent environments
- Prevents dust attraction and improves handling safety
- Suitable for both food and cosmetic packaging applications
- Can be easily incorporated into existing manufacturing processes
However, you should consider that these temporary solutions will gradually lose effectiveness over time. For applications requiring ongoing protection, you might want to explore permanent solutions like inherently dissipative polymers (IDPs), which offer consistent, long-term static control without migration concerns.
Permanent Anti-Static Technology Explained
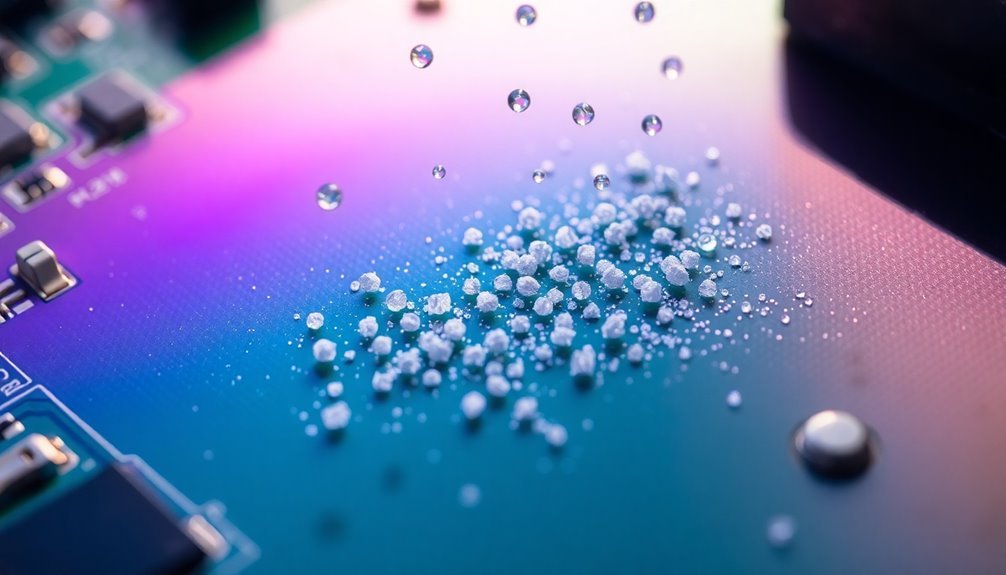
Permanent anti-static additives work by forming continuous conductive networks throughout polymer materials, creating reliable pathways for static dissipation.
These networks, made from materials like carbon nanotubes or inherently dissipative polymers, become an integral part of the material's structure rather than sitting on the surface. Unlike temporary solutions, permanent additives like PELESTAT maintain their effectiveness even after repeated washing cycles.
The resulting permanent protection offers you consistent performance without the need for reapplication, making it ideal for applications requiring long-term static control.
Network Formation Within Polymers
Modern permanent anti-static technology relies on sophisticated network formation within polymers, where specialized agents create continuous pathways for static dissipation. When you incorporate permanent anti-static agents like IDPs or conductive fillers into your polymer matrix, they form a three-dimensional network that guarantees consistent static control.
Unlike temporary solutions, these networks won't migrate or wear off over time. These networks demonstrate anti-static action lasting over one year compared to external agents that only work for around 6 weeks.
The network formation process involves strategic positioning of hydrophilic polar groups on the surface, while conductive fillers establish reliable pathways throughout the material. You'll find this technology particularly effective because it doesn't depend on ambient humidity to function, making it ideal for controlled environments like cleanrooms.
- Inherently dissipative polymers (IDPs) create molecular charge diffusion channels through block copolymer structures
- Carbon nanotubes and graphene form highly efficient conductive networks at low dosage levels
- Polyether block amides position themselves strategically to guarantee continuous static dissipation
- Conductive fillers like carbon black establish permanent pathways within the polymer matrix
- The resulting network maintains consistent performance, as verified through ASTM D257 resistivity testing
The integration of these networks provides long-lasting protection while maintaining your polymer's essential physical properties.
Long-Term Protection Benefits
Building upon the integrated network technology, permanent anti-static solutions deliver exceptional long-term protection that surpasses traditional temporary treatments. You'll find these solutions maintain their effectiveness regardless of environmental conditions, offering reliable static protection in both dry environments and high-friction situations. The incorporation of conductive carbon fillers enables rapid charge dissipation through the material matrix.
Feature | Benefit |
---|---|
Duration | Maintains performance without degradation over years |
Stability | Functions independently of atmospheric humidity |
Integration | Won't migrate or wear off from polymer matrix |
Versatility | Compatible with multiple processing methods |
Safety | Prevents fires and protects sensitive components |
Your manufacturing processes benefit from permanent anti-static solutions through consistent performance across various applications. You can incorporate these solutions into transparent materials without compromising clarity, making them ideal for cleanroom surfaces and medical devices. They're particularly valuable in environments where safety is paramount, such as petrochemical facilities and electronic manufacturing plants. The technology's non-migratory properties guarantee you won't need frequent reapplication, while its compatibility with different polymer matrices allows for customization to meet your specific requirements. This permanent protection substantially reduces long-term maintenance costs and enhances overall safety compliance in sensitive manufacturing environments.
Comparing Cost and Effectiveness
The decision between temporary and permanent anti-static solutions often comes down to balancing immediate costs against long-term value. While temporary solutions offer lower upfront costs, they require frequent reapplication, which can lead to higher cumulative expenses and increased labor costs.
Permanent solutions, though initially more expensive, typically provide better value through consistent protection and reduced maintenance needs. The additives form an immediate network within the polymer structure for reliable performance.
When you're evaluating effectiveness, permanent solutions clearly outperform their temporary counterparts. They offer reliable protection across various environmental conditions and maintain their effectiveness without requiring frequent reapplication.
Temporary solutions, while immediately effective, can be compromised by handling, cleaning, or environmental factors.
- Temporary solutions need regular reapplication and monitoring, increasing long-term operational costs
- Permanent antistats provide consistent protection and reduce warranty claims
- Environmental conditions affect temporary solutions more substantially than permanent ones
- Permanent solutions often meet stricter industry standards and compliance requirements
- Initial investment in permanent solutions typically yields better return through reduced maintenance and replacement costs
Consider your specific application requirements, environmental conditions, and long-term cost implications when choosing between these options. The right choice depends on your particular needs for static protection and budget constraints.
Industry-Specific Anti-Static Requirements
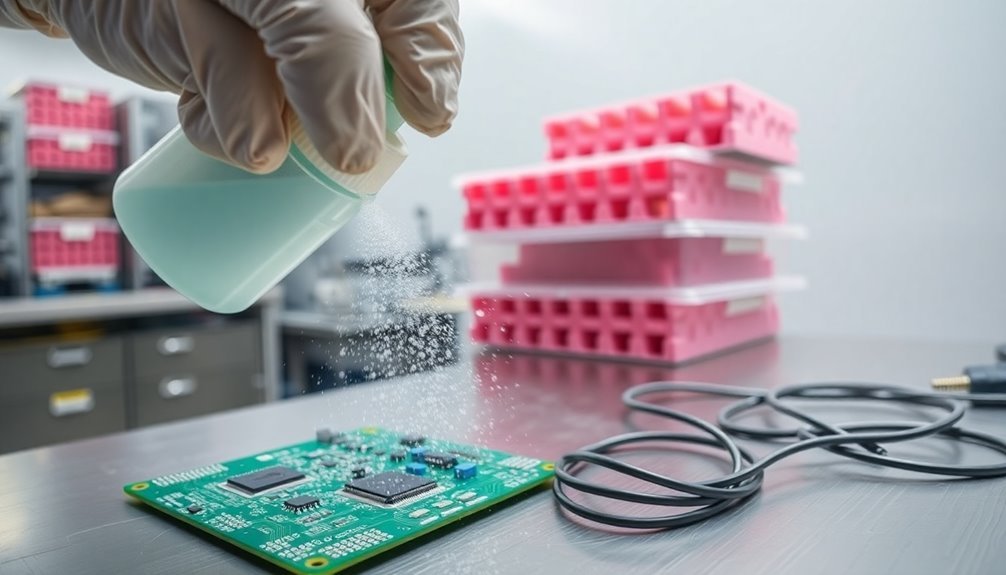
When you're working in electronics manufacturing, you'll need to follow strict EN 1149 standards to protect sensitive components from electrostatic discharge.
You must implement extensive safety measures in hazardous environments, including proper grounding chains and anti-static footwear that meets EN ISO 20345 requirements.
Your cleanroom operations require the most rigorous controls, combining specialized PPE with environmental management systems that maintain precise humidity levels and air purification standards.
Electronics Manufacturing Standards
Modern electronics manufacturing demands strict adherence to established ESD (Electrostatic Discharge) standards, with ANSI/ESD S20.20 and IEC 61340-5-1 serving as primary regulatory frameworks.
You'll need to implement thorough control measures that meet specific resistance requirements and testing protocols. Your facility must maintain point-to-ground resistance below 1.0 x 10^9 ohms, while guaranteeing wrist straps don't exceed 3.5 x 10^7 ohms for effective grounding.
The EOS/ESD Association oversees these standards, providing detailed guidelines for testing and compliance verification. You'll need to regularly test and document all ESD control measures, including ionizers, anti-static materials, and grounding systems.
Your ESD protected areas must incorporate controlled environments with proper anti-static flooring and workstation equipment.
- All personnel must wear tested and approved ESD-safe garments and footwear
- Workstations require conductive materials with documented resistance values
- Ionization systems must meet discharge time specifications
- Grounding systems need regular verification and documentation
- ESD control items must undergo product qualification testing to meet resistance limits
These standards guarantee consistent protection across your manufacturing processes, helping prevent costly damage to sensitive electronic components.
Safety in Hazardous Environments
Safety in hazardous environments calls for specialized anti-static measures that go beyond standard ESD protocols. You'll need to implement thorough solutions that address both personnel safety and operational integrity.
Start by installing static-dissipative or conductive flooring systems to minimize charge buildup from routine activities like walking.
Your material selection is vital – consider using aluminum rigid wall panels or modular stainless steel panels to control static electricity effectively.
In medical device manufacturing, you must prevent static attraction that could compromise product quality, while fuel handling operations require antistatic additives to increase conductivity.
You'll also need proper grounding systems customized to your specific application.
Don't overlook the importance of personal protective equipment. Your workers should wear appropriate anti-static clothing and follow strict handling procedures.
Regular testing and certification of your anti-static equipment guarantee continued effectiveness and compliance with industry standards.
Remember to conduct thorough risk assessments to identify potential static hazards in your facility.
If you're operating a cleanroom, you'll need to meet specific classification requirements for static control based on your industry.
These measures aren't optional – they're essential for preventing accidents and maintaining product integrity in hazardous environments.
Clean Room Control Measures
Precision in cleanroom control measures demands a thorough approach to static management. You'll need to implement a complete system that addresses flooring, walls, clothing, and equipment.
Modern cleanrooms require dissipative or conductive flooring with specific resistance levels to ground static charges effectively, while anti-static wall panels work alongside these floors to create a controlled environment.
Your cleanroom's effectiveness depends on proper gowning procedures and equipment selection. You must enforce strict protocols for anti-static garments, including ESD cuffs and shoes, while maintaining air shower systems at entry points.
When selecting equipment, you'll want to focus on ESD-safe furniture and monitoring devices to track static levels continuously.
- Install dissipative flooring with appropriate ohm measurements for your specific application
- Implement complete gowning protocols with anti-static garments and ESD-safe footwear
- Position ionizing blowers strategically to neutralize static electricity
- Use ESD monitoring equipment to maintain consistent static control
- Integrate sticky mats and air showers at entry points for contamination control
These control measures work together to create a robust static management system that protects sensitive equipment and maintains cleanroom integrity.
Material Compatibility Considerations
Selecting compatible materials stands as a critical factor when implementing permanent anti-static solutions across different polymer types. You'll need to carefully consider the melting point of your base polymer, as low-melting materials like PE and PP require different additives than high-melting polymers such as PA6 and ABS.
When you're working with medical or food contact applications, you'll want to choose specific grades like biobased Pebax(R)Rnew 30R51 SA 01, which meets necessary regulatory requirements.
These permanent solutions maintain their effectiveness regardless of humidity levels, while preserving the host polymer's mechanical strength and chemical resistance.
You can incorporate anti-static additives through various processing methods, including injection molding, extrusion, and blow molding. During manufacturing, you'll find that these additives allow for uniform color distribution without compromising the anti-static properties.
For industrial applications, particularly in electronics and automotive sectors, you'll achieve reliable ESD protection that meets international standards. The key advantage is that you won't sacrifice the material's core properties while gaining permanent static dissipation capabilities across your chosen polymer matrix.
Environmental Impact of Protection Methods
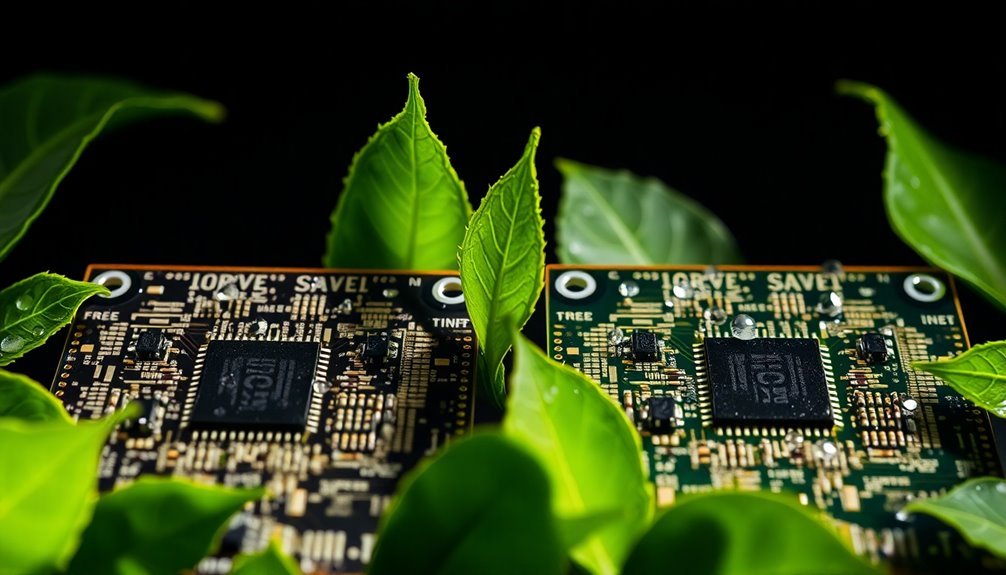
Many anti-static protection methods carry significant environmental implications that you'll need to take into account when implementing ESD solutions. Permanent protection methods often use non-biodegradable materials that contribute to long-term environmental damage and pose waste management challenges. They typically have a higher carbon footprint during production and disposal.
In contrast, temporary ESD protection methods generally offer better environmental outcomes. They use less material, have shorter lifecycles, and often provide recycling options. You can choose temporary solutions that align with current environmental regulations while maintaining effective static control.
The emergence of sustainable alternatives is changing the ESD protection landscape. You'll find innovative options like biodegradable plastics and natural rubber materials that can effectively protect against static while reducing environmental impact.
These sustainable solutions often provide additional benefits:
- Lower waste management costs
- Improved regulatory compliance
- Reduced carbon footprint
- Better recyclability options
- Enhanced corporate environmental responsibility
When selecting your ESD protection method, you'll want to reflect on both immediate effectiveness and long-term environmental impact. By choosing sustainable options, you're not only protecting your equipment but also contributing to environmental preservation while potentially reducing costs.
Regulatory Standards for Both Options
The complex web of regulatory standards shapes both temporary and permanent anti-static protection solutions in industrial settings. You'll need to comply with key standards like NFPA 77, IEC 60079, and ANSI/ESD S20.20 to guarantee proper implementation of anti-static measures.
Standard | Temporary Protection | Permanent Protection |
---|---|---|
NFPA 77 | Grounding and bonding guidelines | Static electricity control procedures |
IEC 60079 | Hazardous environment requirements | Equipment specifications for explosive areas |
ANSI/ESD S20.20 | ESD control program development | Long-term static discharge management |
ASTM F855 | Protective equipment capacity | Permanent grounding infrastructure |
When implementing protective measures, you must guarantee your equipment meets specific requirements. For temporary solutions, you'll need properly inspected ground cable sets and antistatic sheeting that complies with NFPA 99 standards. All installations require careful attention to grounding locations and potential hazards.
To maintain compliance, you'll need regular inspections of both temporary and permanent protective equipment. This includes checking personal safety gear, verifying grounding connections, and guaranteeing all high-capacitance elements are properly short-circuited and grounded before work begins. Remember, certification through accredited ISO9000 bodies confirms your ESD control program's effectiveness.
Performance in Different Environments
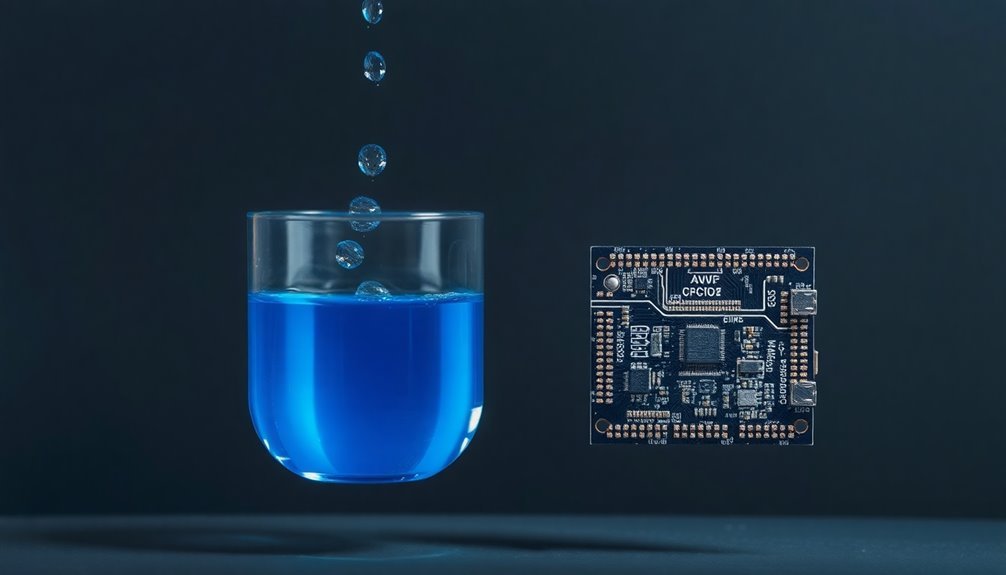
Building upon regulatory compliance, environmental conditions substantially impact the performance of anti-static solutions.
You'll find that humidity levels play a vital role, with permanent anti-static additives maintaining their effectiveness even at low humidity levels of 12-15%.
Temperature variations also affect performance, as higher temperatures can lead to migration of anti-static agents and potential damage to electronic components.
Different environments require specific anti-static approaches based on their unique challenges. When you're working in electronics manufacturing or medical device production, you'll need stringent ESD control measures due to the sensitive nature of components.
In pharmaceutical cleanrooms, anti-static solutions prevent both static buildup and contamination.
- Low humidity environments demand permanent anti-static additives or ionizing blowers for consistent protection
- Temperature fluctuations can compromise the effectiveness of anti-static plastics and coatings
- Controlled environments in manufacturing facilities maintain ideal conditions for ESD prevention
- Warehouse and distribution centers require durable anti-static solutions for storage and handling
- Medical and pharmaceutical environments need combined protection against static and contamination
The key is matching your anti-static solution to your specific environmental conditions while considering humidity, temperature, and application requirements.
Maintenance and Durability Factors
Maintaining anti-static solutions requires a systematic approach to guarantee their long-term effectiveness and durability. You'll need to follow manufacturer guidelines and industry standards like ANSI/ESD S20.20 to guarantee peak performance. Regular cleaning with IPA-absorbent cloths and frequent inspections help prevent static buildup and extend equipment lifespan.
The durability of anti-static materials depends largely on their composition and maintenance. Anti-static silicone offers superior longevity due to its heat resistance and chemical stability, while ESD plastics provide consistent static control when properly maintained.
Factor | Impact | Maintenance Need |
---|---|---|
Environment | Dust exposure affects effectiveness | Regular cleaning required |
Temperature | High heat can degrade some coatings | Temperature monitoring |
Usage | Frequent handling reduces lifespan | Periodic inspection |
Material Type | Different materials age differently | Material-specific care |
Cleaning Method | Improper cleaning damages coating | Follow guidelines strictly |
You'll maximize your anti-static solution's durability by controlling environmental conditions and implementing a regular maintenance schedule. For solar panels specifically, anti-static coatings can markedly extend their operational life when combined with proper cleaning routines and environmental protection measures.
Frequently Asked Questions
Can Anti-Static Solutions Affect the Color or Appearance of Treated Materials?
Yes, your choice of anti-static agent can affect appearance. Traditional agents like carbon black darken materials, but modern options like graphene nanotubes and Pebax polymers let you maintain color and transparency.
How Quickly Do Temporary Anti-Static Treatments Need to Be Reapplied?
You'll need to reapply temporary anti-static treatments based on usage: daily for work surfaces, every 1-2 months for high-traffic areas, and every 2-4 months for less-used spaces. Environmental conditions affect timing.
Do Anti-Static Solutions Interfere With Product Labeling or Barcodes?
You'll find that anti-static solutions don't interfere with your product labels or barcodes. They actually improve labeling processes by reducing static-related positioning errors and help protect barcode scanners from damaging electrostatic discharge.
Are There Health Risks Associated With Handling Anti-Static Treated Materials?
Yes, you should be cautious as anti-static treatments can contain harmful chemicals like PFAS, phthalates, and BPA. These substances may cause cancer, hormone disruption, and respiratory issues through skin contact.
Can Anti-Static Protection Be Compromised by Cleaning or Disinfection Procedures?
Yes, your anti-static protection can be compromised during cleaning and disinfection, especially with electrostatic methods. You'll need to regularly reapply protective coatings and carefully choose compatible cleaning products to maintain effectiveness.
In Summary
You'll need to weigh both temporary and permanent anti-static solutions based on your specific needs. While temporary solutions offer flexibility and lower upfront costs, permanent protection provides long-term reliability and reduced maintenance. Consider your industry requirements, environmental conditions, and budget constraints when choosing. Remember, the most effective solution isn't always the most expensive – it's the one that best matches your application.
Leave a Reply