You need to test your ESD wrist strap's resistance daily to prevent dangerous electrical shocks and protect sensitive electronic equipment from damage. A properly functioning strap should maintain resistance between 750K ohms and 35 megohms, according to ANSI/ESD standards. Regular testing identifies faulty components like broken wires, dirty cuffs, or poor skin contact that could compromise your safety. With certified testers providing quick pass/fail results, you'll know immediately if your strap needs replacement. Understanding proper testing procedures and maintenance requirements will help you maintain a safe, compliant ESD protection system that saves lives and equipment.
Safety First: Testing Saves Lives
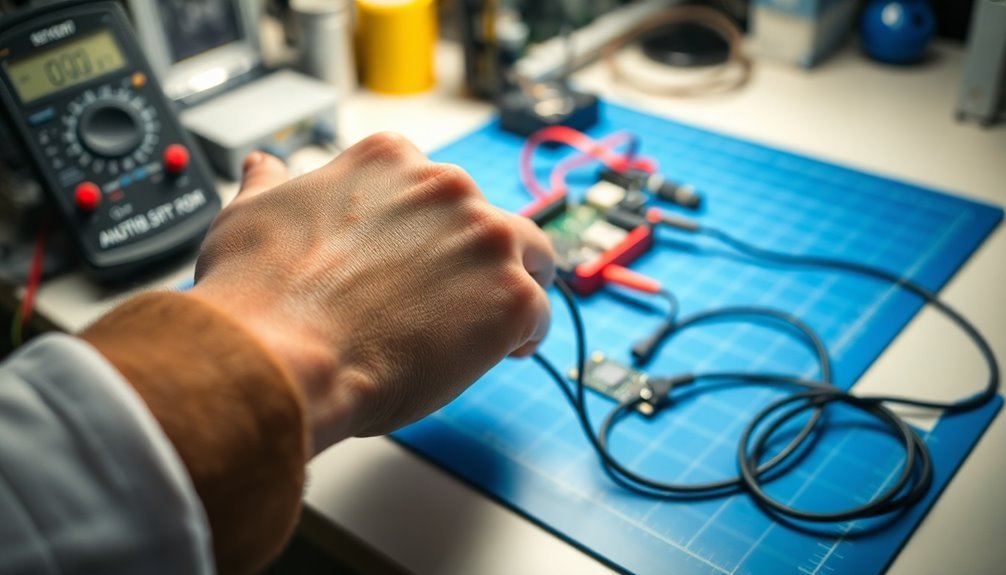
Testing your ESD wrist strap isn't just a routine task—it's a critical safety measure that protects both you and your sensitive electronic components. When you work with electronic devices, you're exposed to potential electrical hazards that a faulty wrist strap can intensify.
Testing ensures your wrist strap maintains resistance below 35 megohms. Regular testing helps identify defective resistors that could otherwise lead to dangerous electrical shocks. You'll want to make testing your wrist strap a daily habit before handling any ESD-sensitive devices. Daily verification is essential since portable testers can quickly assess performance during workshop activities.
Using a certified ESD wrist strap tester, you can quickly verify if your equipment meets the required resistance specifications. When you get a green light, you're safe to proceed; a red light means you need to address the issue immediately.
Don't underestimate the consequences of skipping these tests. Untested wrist straps can result in severe injuries and costly damage to electronic components.
By maintaining detailed test logs and following proper testing procedures, you're not only protecting yourself but also ensuring compliance with industry standards like ANSI/ESD S1.1 and IEC 61340-5-1.
Understanding ESD Resistance Standards
Industry safety benchmarks establish clear requirements for ESD wrist strap resistance that you'll need to understand and follow. The two primary standards, ANSI/ESD S1.1-2021 and IEC 61340-5-1, specify that your wrist strap's resistance must be less than 3.5 x 10E7 ohms, while ANSI/ESD S20.20 requires the impedance between you and ground to stay under 35 megohms.
You'll need to verify your wrist strap's compliance through daily testing using specialized ESD testers that measure ground resistance. Visual inspections alone are insufficient for detecting failures in your grounding equipment. Broken coiled cords are a common cause of wrist strap failure that requires regular testing to identify. These devices will give you a clear pass/fail indication, ensuring your grounding system meets the required specifications. If you're using continuous monitors, you'll receive immediate alerts when problems arise, eliminating the need to maintain manual test records.
To maintain proper resistance levels, you'll want to keep your wrist strap clean and well-maintained. Apply ESD lotion to improve skin contact, and clean the strap regularly with mild detergent – Woolite™ works well for elastic bands.
Remember to dry metallic expansion bands thoroughly to prevent corrosion, and never use bleach, as it can damage the strap's materials. Keep detailed records of all your testing activities to demonstrate your compliance with these essential standards.
Common Causes of High Fails
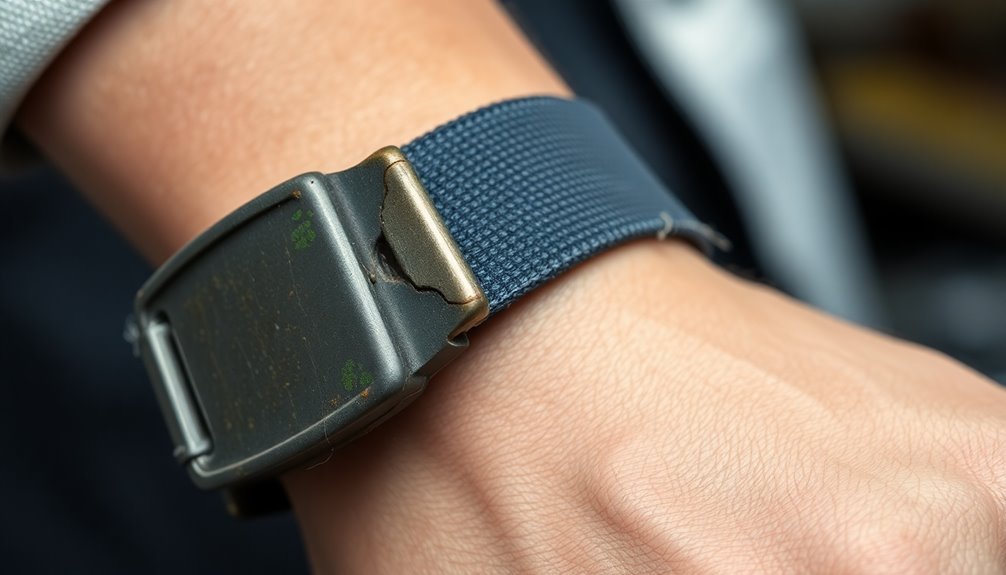
Even with proper testing procedures in place, you'll likely encounter high resistance fails during wrist strap testing. Understanding the common causes can help you identify and resolve these issues quickly.
Equipment problems often trigger high fails, including broken wires in coil cords and dirty cuff interiors. You'll also face failures if you're wearing the strap incorrectly, such as having it too loose or over clothing. High skin resistance and built-up skin oils between your wrist and the conductive fabric can compromise the strap's effectiveness. Wrist straps while worn should be tested for the most accurate results.
Poor maintenance practices greatly contribute to failures. If you're not regularly cleaning and inspecting your wrist straps, they'll develop issues that lead to high resistance. When you notice wear and tear, don't continue using damaged equipment – replace it immediately. Regular audits and maintenance are critical for ensuring ongoing compliance with ESD standards.
Additionally, improper storage can damage your wrist straps over time.
Your working environment plays an essential role too. If you're operating in high static environments without proper precautions or using improperly grounded work surfaces, you'll experience more failures.
Regular monitoring and testing are vital – don't wait for failures to occur before implementing proper ESD control measures.
Preventing Low Resistance Issues
You'll need to test your ESD wrist straps regularly to identify and prevent dangerous low resistance conditions that could put you at risk.
Regular testing helps ensure the resistor effectively limits electrical current to safe levels.
If you're getting low resistance readings, immediately check for damaged ground paths, faulty wiring, or worn-out straps that might allow unsafe current flow.
Fast static discharge through quality wrist straps occurs in less than 0.1 seconds when properly functioning.
Replace any defective components right away to maintain the proper safety resistance level of 1MΩ between you and ground.
Safety Through Regular Testing
Safety testing protocols for ESD wrist straps must address potential low-resistance issues that can create dangerous current paths. You'll need to test your wrist strap daily to verify the resistance falls between 750K ohms and 35 megohms, guaranteeing both protection and safety. This testing isn't optional – it's a critical requirement under ANSI/ESD S20.20 and related standards.
Your testing should include the entire system: the wristband, ground cord, and skin interface. The 1 megohm resistor in your wrist strap plays a crucial role by limiting current to 250 microamps at 250 Volts rms AC, protecting you from electrical hazards. Don't compromise this safety feature by using non-compliant grounding setups or alligator clips.
You'll need to maintain daily test records to demonstrate compliance with standards like ANSI/ESD S1.1-2021 and IEC 61340-5-1. If you're working with particularly sensitive applications, you might need to implement continuous monitoring systems.
While ESD lotions can improve your skin's conductivity, make certain they don't interfere with the safety resistor's function. Remember, multiple grounding paths or damaged coil cords can create dangerous low-resistance situations you'll need to avoid.
Identifying Dangerous Current Flow
Every ESD wrist strap operator needs to recognize dangerous current flow conditions that can arise from low resistance issues. When your wrist strap's resistance falls below recommended levels, you're at risk of experiencing harmful electrical currents through your body. Understanding these dangers will help you maintain safe working conditions while handling ESD-sensitive components.
Your safety depends on maintaining the proper resistance range, which should be less than 3.5 x 10E7 ohms but not so low as to create a hazardous current path. If you detect unusually low resistance during testing, you'll need to immediately address the issue, as it could indicate a dangerous short circuit in your grounding system.
Key indicators of dangerous current flow conditions include:
- Resistance readings considerably below the standard threshold
- Signs of damage or wear in the wrist strap or cord
- Unusual sensations while wearing the strap
You'll need to perform daily testing of your wrist strap to guarantee it maintains proper resistance levels. Using an ESD wrist strap tester, you can quickly verify that your equipment meets ANSI/ESD S1.1-2021 standards and provides safe, effective static discharge protection without risking dangerous current flow.
Replace Faulty Ground Paths
Most faulty ground paths stem from worn-out components and improper maintenance of ESD wrist straps. You'll need to replace your wrist strap when it shows signs of physical wear, stretching, or fails resistance testing. Don't wait until your strap completely fails, as this puts sensitive electronics at risk.
Condition | Required Action |
---|---|
Stretched Band | Replace immediately – poor skin contact |
Failed Resistance Test | Replace strap – safety hazard |
Dry Skin Issues | Apply ESD lotion before replacement |
If you're experiencing intermittent grounding issues, check that you're wearing the strap directly against your skin, not over clothing. The 1 megohm resistor in your strap must maintain its integrity to protect you from electrical shock while guaranteeing proper static discharge. You'll need specialized testing equipment to verify the strap's resistance levels meet ESD standards.
Regular maintenance helps identify problems before they cause damage. When replacing your ground path components, verify you're using materials that meet industry standards. Remember, proper grounding isn't just about having a functional strap – it's about maintaining consistent protection for sensitive electronic components and guaranteeing your safety through controlled current flow.
Proper Testing Equipment Selection
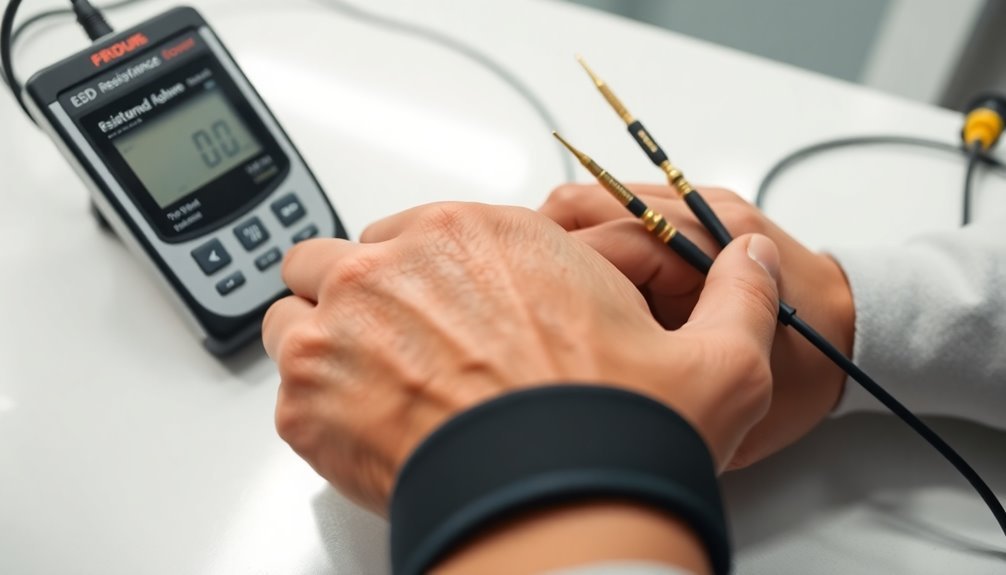
Selecting the right ESD wrist strap testing equipment requires careful consideration of three main categories: general purpose testers, advanced test stations, and constant monitoring systems.
General purpose testers like the SI-500 and WST200 offer simple push-button operation with clear LED readouts for pass/fail results, making them ideal for frequent testing routines.
Key features you'll want to evaluate include:
- Connectivity options that support various terminations like banana jacks and snap fasteners
- Visual and audible indicators for clear pass/fail results and low battery warnings
- Data logging capabilities if you need to maintain testing records
For more sophisticated needs, consider advanced test stations like the Warmbier 7100.PGT120.COM, which offers computer integration and data storage.
If you're looking for continuous protection, constant monitoring systems such as the CM400 eliminate manual testing requirements while providing immediate notification of failures.
When making your selection, don't forget to check for included calibration certificates and warranty coverage.
Most quality testers, like the SI-500, come with one-year calibration certificates and warranties, ensuring your investment's reliability and accuracy.
Daily Testing Best Practices
When protecting sensitive electronic components, daily ESD wrist strap testing serves as your first line of defense against static damage. You'll need to follow specific procedures to guarantee accurate testing and maintain compliance with industry standards like ANSI/ESD S1.1-2021 and IEC 61340-5-1.
Testing Step | Action Required | Critical Points |
---|---|---|
Pre-Test Setup | Use dedicated test station | Guarantee equipment is calibrated |
System Check | Test entire wrist strap system | Include band, cord, and skin contact |
Result Analysis | Check pass/fail indication | Look for resistance within 35 megohms |
Documentation | Record test outcomes | Maintain logs for quality control |
Always test your wrist strap before handling any ESD-sensitive devices. If you get a failing result, immediately stop work and troubleshoot the issue. Check both the wristband and coil cord separately to identify the faulty component. You'll find that many modern test stations offer automated logging capabilities, which can streamline your documentation process.
Consider implementing continuous monitoring systems for real-time feedback on your wrist strap's functionality. This additional layer of protection helps prevent potential failures between scheduled tests and enhances your overall ESD protection strategy.
Maintaining Your Wrist Strap System

Proper maintenance protocols guarantee your ESD wrist strap system remains reliable and effective over time.
You'll need to regularly inspect your strap for signs of wear, including cracks in the conductive material and corrosion at connection points. Don't overlook the importance of testing conductivity to verify it meets current ESD standards.
To maintain peak performance, you should follow these essential practices:
- Wear the strap snugly against bare skin, never over clothing
- Check the grounding point's security and functionality daily
- Apply ESD lotion when needed to improve skin conductivity
Your maintenance routine should include regular diagnostic testing using specialized equipment to measure electrical resistance.
When you're conducting these tests, make sure to check the strap while it's being worn to confirm proper skin contact. If you notice any damage or deterioration, replace the strap immediately rather than risking potential equipment damage.
Remember to use continuous monitors whenever possible, as they'll alert you instantly if your strap fails during use.
Don't connect your strap to an ESD mat stud, as this can increase system resistance and compromise protection.
Cost Benefits of Regular Testing
Regular testing of ESD wrist straps delivers substantial cost savings across multiple aspects of manufacturing operations.
You'll prevent costly damage to ESD-sensitive devices, potentially saving thousands of dollars in repairs and replacements. The initial investment in testing equipment quickly pays for itself through reduced product losses and improved quality control.
You'll also minimize your liability risks by maintaining proper testing records and compliance with industry standards like ANSI/ESD S1.1-2021 and IEC 61340-5-1. This protection becomes vital when dealing with warranty claims or potential legal issues stemming from ESD-related product failures.
Your operational efficiency will improve markedly with regular testing. By implementing continuous monitoring systems, you'll detect failures immediately and avoid production delays.
These systems eliminate the need for manual testing while providing real-time feedback on wrist strap performance. You'll maintain smoother operations with fewer interruptions and reduce downtime through early detection of potential issues.
In your Electrostatic Protected Area (EPA), daily testing guarantees both employee safety and equipment protection.
The thorough tracking of equipment performance helps you predict and prevent failures before they impact your production line, leading to sustained cost efficiency.
Frequently Asked Questions
Can I Wear My ESD Wrist Strap Over Long Sleeves?
You shouldn't wear your ESD wrist strap over long sleeves. Direct skin contact is essential for proper grounding, and sleeves can interfere with this connection. Roll up your sleeves or wear short sleeves instead.
How Often Should I Replace My ESD Wrist Strap Band?
You'll need to replace your ESD wrist strap band every 6-12 months with regular use. Don't wait for failure – frequent use and wear can reduce effectiveness even if it looks fine externally.
Does Perspiration Affect the Accuracy of ESD Wrist Strap Readings?
Yes, your perspiration can affect ESD wrist strap readings. While sweating isn't directly listed as a cause for test failures, it can influence your skin's resistance, potentially impacting the accuracy of your measurements.
Can Multiple People Share the Same ESD Wrist Strap?
You shouldn't share ESD wrist straps with others. It's unsafe, violates compliance standards, and increases equipment damage risks. Each person needs their own strap to guarantee proper grounding and maintain workplace safety.
Are Wireless ESD Wrist Straps as Effective as Traditional Wired Ones?
No, wireless ESD wrist straps aren't as effective as traditional wired ones. You won't get proper grounding without a direct connection, and they can't meet ANSI/ESD S20.20 standards. Stick with traditional wired straps.
In Summary
Testing your ESD wrist strap's resistance isn't optional – it's vital for your safety and equipment protection. You'll save money by preventing costly damage to sensitive electronics and avoid potential injury from electrical shorts. Make testing part of your daily routine, and you'll maintain a reliable static-safe work environment. Don't skip this essential step; it's your first line of defense against ESD hazards.
Leave a Reply