A surface resistance tester measures the electrical resistance across a material's surface in ohms per square (Ω/□). You'll find these devices commonly used to test thin films, coatings, and work surfaces – especially in electronics manufacturing where static discharge control is critical. The tester works by applying voltage between probes or electrodes and calculating the resistance to electrical current flow. Most models can measure from 10³ to 10¹² ohms and feature different test voltages (10V to 500V) depending on the material type. Understanding your material's surface resistance properties is just the first step in effective ESD prevention and control.
Understanding Surface Resistance
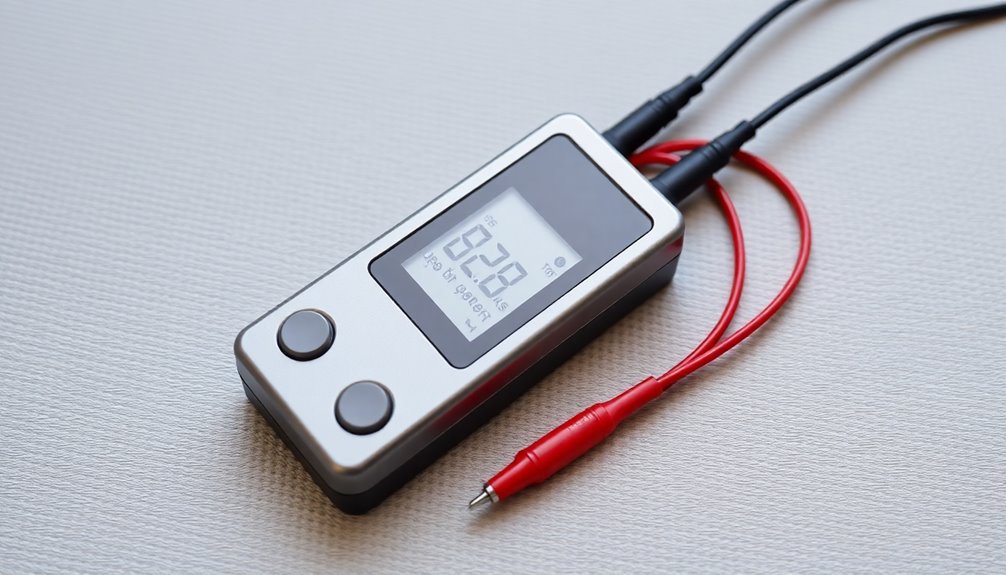
Surface resistance, measured in ohms per square (Ω/□), represents the electrical resistance a material offers across its surface area. You'll find it's particularly important when working with thin films, paints, and coatings where the material thickness varies. The thinner your material becomes, the higher its specific surface resistance can be.
When you're measuring surface resistance, you'll need to take into account several key factors. The material's thickness directly affects the readings, and you'll need to multiply the measured surface resistance value by the geometrical coefficient of your electrode fixture to compare surface resistivity and resistance accurately. Maintaining controlled environmental conditions during testing is essential for obtaining reliable measurements.
You can convert surface resistivities to surface resistances by dividing the surface resistivity value by the geometric factor.
You'll calculate surface resistance using the formula ps = R · RCF = ρv × (1 / t), where R represents the measured resistance, RCF is the resistance correction factor, ρv stands for specific volume resistance, and t indicates material thickness.
For precise measurements, you'll often use the four-point probe method, which is especially vital when working with materials in corrosion-prone environments.
Key Testing Methods
Four primary methods dominate the field of surface resistance testing, each designed for specific applications and material types. You'll find these methods used across various industries, from electronics manufacturing to material science research.
The most common testing approaches include:
- Parallel Bar Sensing, which uses two electrodes to measure resistance in ohms per square, making it ideal for electronics packaging materials. The ASTM Standard method ensures reliable measurements across different surface types.
- Four-Probe Method, utilizing four co-linear probes to measure sheet resistance through voltage drop calculations
- Resistance-to-Ground (RTG) Testing, measuring resistance between a surface point and ground using a 5-pound electrode
- Point-to-Point (RTT) Testing, which measures resistance between two points using dual 5-pound electrodes
When you're working with static dissipative surfaces, you'll need to follow ANSI/ESD S4.1 guidelines for both RTG and RTT testing.
For RTG measurements, you'll want to see readings between 1×10^6 and 1×10^9 ohms.
For RTT measurements, the readings should be at least 1×10^6 ohms. Remember to place your electrodes at least 2 inches from edges and 3 inches from grounded points for accurate RTT testing.
Equipment Components
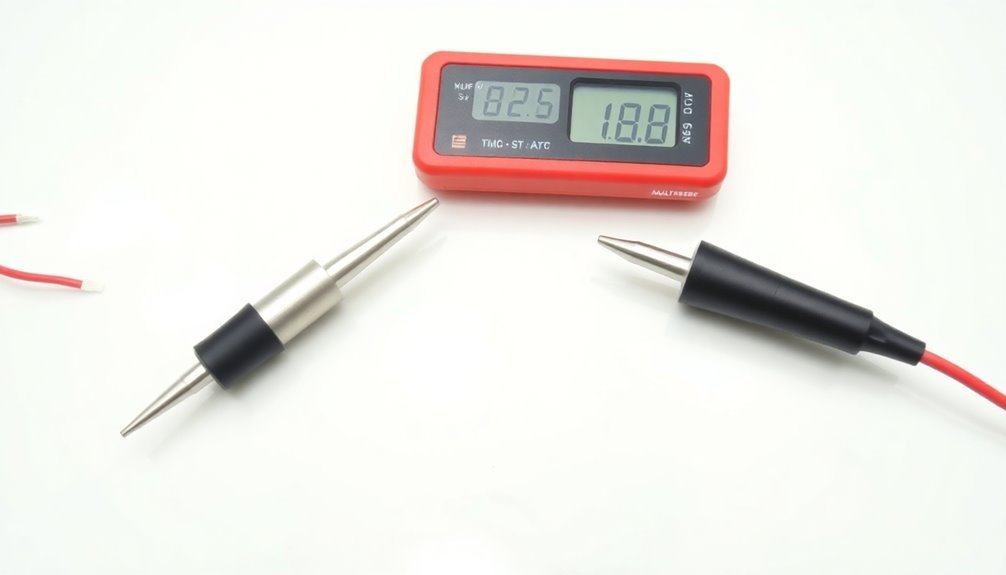
A resistance tester's core components work together to deliver precise measurements across various surface types. At its heart, you'll find a digital display featuring a 3.5-digit LCD screen that shows measurement values and exponent numbers.
The meter includes voltage selection options of 10V and 100V, with automatic switching capabilities to guarantee accurate readings. The device features automatic power shut off for energy efficiency.
The probe system consists of specialized concentric ring probes and 5-lb disk electrodes made from conductive rubber. These components are essential for measuring surface resistance, resistivity, and point-to-point resistance. The probes incorporate a geometry coefficient that simplifies resistivity calculations.
Your tester's advanced features include automatic zeroing for measurement accuracy, ambient condition monitoring for temperature and humidity, and function LEDs indicating measurement type and test voltage. You'll also benefit from a 15-second electrification period that guarantees reliable readings.
The device maintains accuracy levels within ±10% for standard measurements and ±20% for higher resistance values. It complies with key industry standards, including ANSI/ESD S4.1 and IEC 61340-2-3, making it suitable for factory audits, material evaluations, and compliance testing.
Industry Standards
Reliable surface resistance testing depends on strict industry standards that define measurement ranges and procedures. You'll need to follow specific guidelines for voltage settings: 10V for conductive materials, 100V for dissipative materials, and higher voltages like 500V for insulative materials.
The measurement range typically spans from 10^3 to 10^12 ohms, with accuracy levels of ±10% for most readings. Advanced qualification test meters provide higher precision for critical applications.
Key standards you must follow include:
- ANSI/ESD S4.1 for surface resistance measurements
- ESD TR53 for testing methodology
- ANSI/ESD S20.20 for overall ESD control
- NIST traceable calibration requirements
Your testing procedures should involve proper electrode placement, staying at least 2 inches from edges and 3 inches from groundable points. You'll need to use two 5-lb electrodes placed 10 inches apart for RTT measurements, while RTG testing requires one electrode with a ground connection.
Remember to record environmental conditions, including temperature and relative humidity, during testing. Your documentation must include test results, conditions, and equipment details to maintain compliance with industry standards.
Common Applications
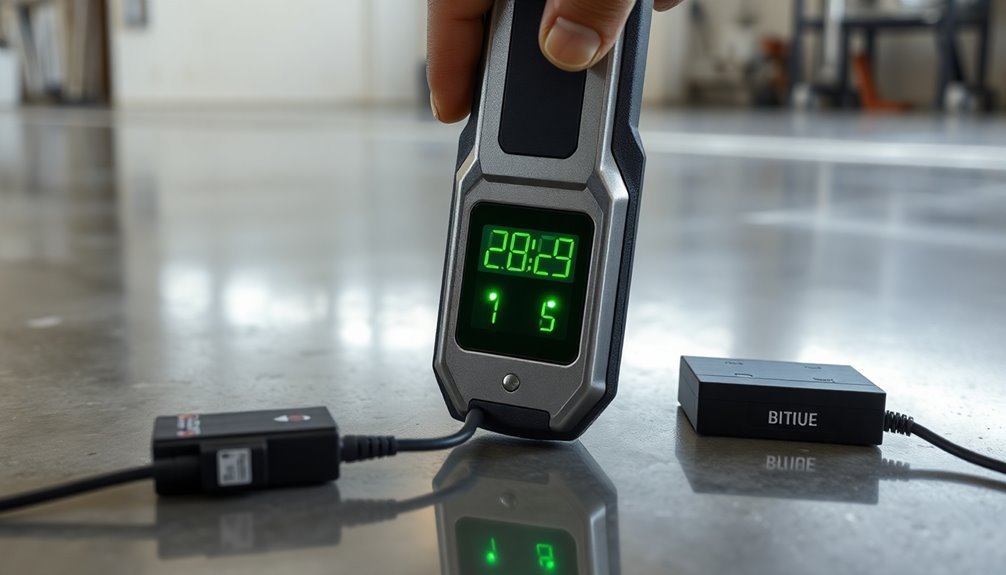
Surface resistance testers play a vital role across diverse industrial applications, from electronics manufacturing to quality control programs. They are extensively used in testing packaging materials, particularly in the electronics industry where they evaluate ESD packaging products and various conductive and static dissipative materials. Following industry standards for compliance, these testers help verify materials meet required specifications.
In workplace settings, you can use these testers to assess ESD table mats, flooring, and other work surfaces essential to electronics manufacturing. They are important for factory audits and test lab evaluations where precise measurements of surface resistance are necessary for quality control.
When it comes to ESD control products, you'll need these testers to audit work surfaces, evaluate different material types, and test critical safety equipment like wrist straps, footwear, and ESD chairs. They are particularly valuable in manufacturing environments where static control is crucial.
You can also rely on surface resistance testers for broader applications in manufacturing and static control programs. They help verify compliance with ESD prevention protocols, classify materials according to their resistance properties, and make certain incoming materials meet specifications in static-controlled areas.
These measurements are vital for maintaining safety standards and product quality in sensitive manufacturing environments.
Test Voltage Requirements
Test voltage selection stands at the heart of accurate surface resistance measurements. You'll need to apply different voltages depending on the material's conductivity level. Conductive materials require 10V, while dissipative materials need 100V. For insulative materials, you might need to increase the voltage to 500V to get reliable readings.
Modern surface resistance testers often come with both automatic and manual voltage selection capabilities. When using automatic mode, your meter will switch between voltages based on the detected resistance range. However, you can override this feature if you need to maintain a specific test voltage. Environmental conditions like temperature and humidity can affect your measurement results.
Key voltage requirements you must consider:
- Maintain voltage stability within ±5% accuracy under load conditions
- Follow ANSI/ESD S4.1 testing procedures for compliant measurements
- Hold the test voltage steady for the standard 15-second testing period
- Select appropriate voltage based on material type (10V for conductive, 100V for dissipative)
Your meter's ability to maintain constant voltage throughout the testing process is vital for accurate measurements. Whether you're using automatic or manual selection, ensuring the correct test voltage will substantially impact your measurement's reliability and compliance with ESD testing standards.
Measurement Ranges
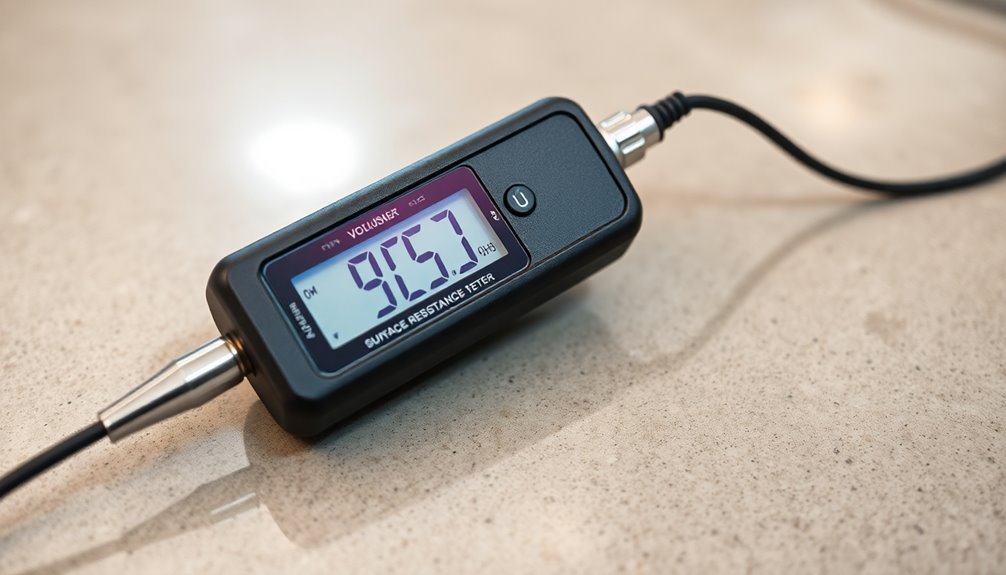
Modern resistance testers offer measurement ranges spanning from 10³ to 10¹² Ohms/Square, covering the full spectrum of material classifications. While entry-level meters typically provide this basic range, high-end devices can measure from 1 Ohm up to 1.2 Tera Ohm. You'll find these ranges essential for testing conductive, dissipative, and insulative materials with precision.
The measurement accuracy you can expect typically falls within ±10%, with repeatability at ±5%. When you're conducting qualification testing, you'll need higher accuracy, but verification testing can often work with lower precision levels. This is especially important since surface resistivity values provide an inherent property measurement independent of electrode configuration.
Material Type | Resistance Range | Typical Applications |
---|---|---|
Conductive | 10³-10⁵ Ω/sq | Static Discharge |
Dissipative | 10⁵-10⁹ Ω/sq | ESD Protection |
Insulative | >10⁹ Ω/sq | Electrical Safety |
You'll encounter two primary measurement techniques: parallel bar sensing and concentric ring probe. While the geometry of electrodes affects surface resistance measurements, it won't impact resistivity readings. Most modern testers include automatic ranging and can measure both surface resistance and resistivity, making them versatile tools for your testing needs.
Environmental Effects
Environmental factors dramatically influence the accuracy of your surface resistance measurements. When you're testing surfaces, you'll need to account for temperature fluctuations, humidity levels, and contamination that can substantially affect your readings.
Temperature changes cause materials to expand or contract, altering their conductivity and potentially creating mechanical stress that impacts surface resistance. The formation of multiple dry bands on surfaces can significantly increase surface resistance measurements.
Humidity plays a vital role in your measurements as it can create moisture layers that facilitate ionic conduction and promote corrosion. You'll notice that high humidity environments particularly affect surface resistivity and can lead to electrical leakage or short-circuiting.
Key environmental factors you must consider include:
- Temperature variations that affect atomic vibration and material properties
- Moisture accumulation that impacts surface conductivity
- Pollution and contamination levels that decrease surface resistance
- Surface cleanliness and material composition that influence resistivity
When you're conducting surface resistance tests, you'll need to monitor these environmental conditions closely. The interaction between temperature, humidity, and pollution can create complex effects on your measurements.
For accurate results, you should maintain consistent environmental conditions and guarantee proper surface preparation before testing.
Material Classification Guide
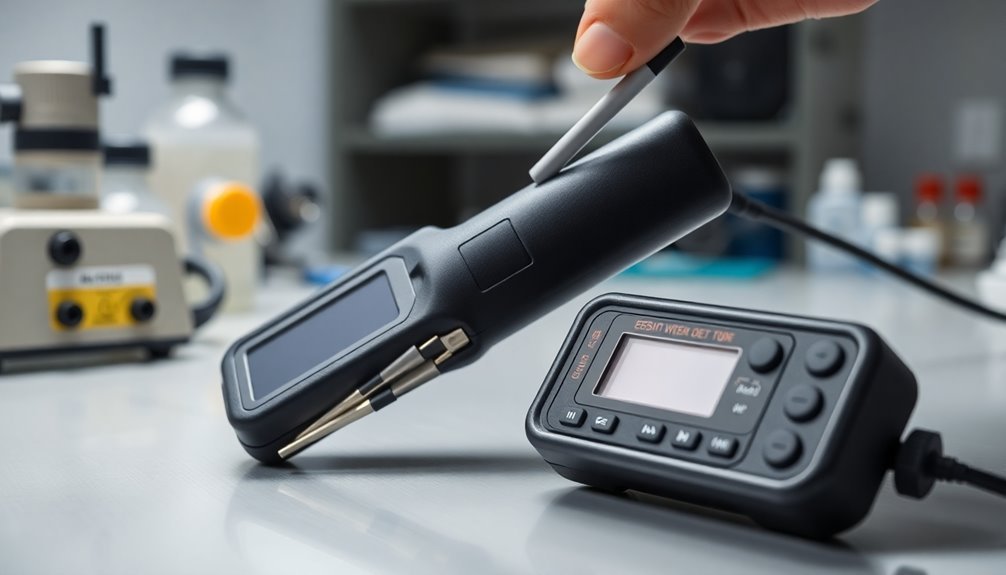
When testing materials with a surface resistance meter, you'll find conductive materials measure between 10^3 and 10^5 Ohms per square.
Static dissipative materials fall within the range of 10^5 to 10^11 Ohms per square, making them ideal for ESD-sensitive applications.
Materials measuring above 10^11 Ohms per square are classified as insulative, which effectively block current flow.
Conductive Range: 10^3-10^5 Ohms
According to established ESD standards, materials with surface resistivity between 10^3 and 10^5 Ohms do not fall into the conductive range classification as stated. Instead, materials are considered conductive if they have a surface resistivity of less than 1 x 10^5 Ω/square or a volume resistivity of less than 1 x 10^4 Ω-cm, as defined by the ESD Association's guidelines, particularly ESD ADV1.0-2017.
When you're working with conductive materials, you'll need to understand these key characteristics:
– They allow for easy flow of electric current through their surface.
Testing must begin by understanding the correct range for conductive materials.
- Measurements are displayed in either digital format or decade scale.
- Surface resistivity is measured in Ohms/square (Ω/sq).
Proper classification is vital for ESD protection applications. When you're using a surface resistance tester, it'll typically offer both automatic and manual voltage selection options. These measurements help you determine if your material meets the conductive range requirements and whether it's suitable for your specific ESD protection needs.
The detailed results you obtain are essential for accurate material classification and application selection. However, the statement that conductive materials are specifically tested using surface resistance meters operating at 10V for the range between 10^3 and 10^5 Ohms is not accurate. Surface resistance meters for ESD measurements are recommended to operate within the range of 10-100V according to ESD norms.
When working with ESD materials, it's crucial to adhere to the correct standards and testing methods to ensure proper classification and functionality.
Dissipative Limits: 10^5-10^11 Ohms
Testing dissipative materials requires understanding their distinct resistance range of 10^5 to 10^11 Ohms per square. When you're measuring these materials with a surface resistance tester like the 740 SRM, you'll find they fall between conductive and insulative categories, offering controlled charge dissipation that's essential for protecting sensitive electronic components.
You'll notice that dissipative materials are designed to suppress initial electrostatic charges while allowing them to flow to ground in a controlled manner. These materials are often color-coded for easy identification and commonly appear in electronics manufacturing environments as work surfaces and packaging materials.
To measure dissipative properties accurately, you'll need to use surface resistance testers that apply voltage and measure current flow through parallel bar sensors or concentric ring electrodes. The tester will automatically calculate surface resistivity in Ohms per square, following ASTM standard methods.
When selecting materials for ESD protection, you must verify they meet these specific resistivity standards. Common examples include conductive composites and specially filled polymers that provide reliable static discharge protection while preventing sudden electrical discharges that could damage sensitive electronic devices.
Insulative Properties Above 10^11
Materials classified as insulators exhibit surface resistance values above 10^11 ohms per square, marking a distinct shift from dissipative materials. These highly resistant materials are vital in applications where charge accumulation needs to be prevented from flowing across surfaces.
When you're using a surface resistance tester like the 740 Surface Resistance Meter, readings above this threshold clearly indicate insulative properties.
Understanding insulative materials' characteristics is essential for proper material selection. When you're testing surfaces, you'll want to look for these key indicators:
- Surface resistance measurements consistently showing values between 10^11 and 10^19 ohms per square
- Clear distinction from dissipative materials in resistance meter readings
- Stable measurements under standard testing conditions following ASTM D-257 guidelines
- Reliable results across multiple test points on the surface
You can accurately measure these high resistance values using parallel bar sensing technology, which provides repeatable results. The automatic ranging feature in modern surface resistance testers helps you quickly identify when a material falls into the insulative category, making classification straightforward and reliable for your specific application needs.
Frequently Asked Questions
How Often Should Surface Resistance Testers Be Recalibrated?
You should calibrate your surface resistance tester annually, but you'll need more frequent checks if you're dealing with critical ESD items or harsh environments. Consider your specific risks and corporate procedures.
Can Surface Resistance Testers Measure Through Protective Coatings or Films?
Yes, you can measure through protective coatings using surface resistance testers. They'll use techniques like four-point probe or concentric ring methods to accurately assess resistance, even when there's a protective layer present.
What Causes Sudden Changes in Surface Resistance Measurements?
You'll notice sudden changes in surface resistance when there's rapid temperature fluctuation, humidity shifts, surface contamination, or damage to protective coatings. Environmental changes and material stress can also cause unexpected measurement variations.
Are Wireless Surface Resistance Testers as Accurate as Wired Ones?
You'll find wired testers are generally more accurate due to their stable connections. While wireless models can match accuracy under ideal conditions, they're more susceptible to electromagnetic interference and power fluctuations during measurements.
Do Surface Resistance Measurements Vary Between Different Brands of Testers?
You'll notice slight variations in measurements between different brands of testers, but if they're properly calibrated and meet industry standards, the differences shouldn't substantially impact your testing results or material classification.
In Summary
You'll find surface resistance testers are essential tools for measuring a material's ability to dissipate static electricity. Whether you're testing floors, work surfaces, or packaging materials, these devices help you determine if your materials fall within ESD-safe parameters. By understanding the readings and following industry standards, you'll guarantee your workplace maintains proper static control measures and protects sensitive electronic components.
Leave a Reply