When selecting anti-static foam packaging, you'll need to think about both density and ESD protection levels. Low-density foams (0.8-1.5 PCF) provide basic cushioning but may compress over time, while medium-density options (1.5-3.5 PCF) offer better durability. For sensitive electronics, choose between pink anti-static foam with surface resistance of 10^9-10^12 ohms/sq or black conductive foam measuring 10^3-10^6 ohms/sq. Higher density foams (3.5+ PCF) deliver superior compression strength and protection. The right combination of density and static control properties guarantees your components stay safe during storage and transport. Understanding these key differences will help you make an informed packaging decision.
Understanding Foam Density Measurements
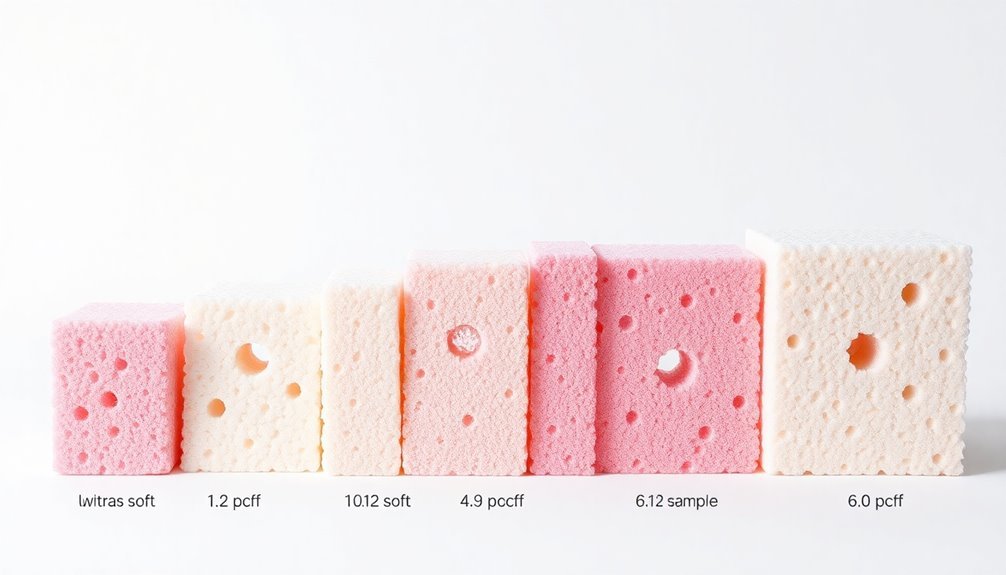
Understanding foam density involves measuring the weight of foam per unit volume, typically expressed in pounds per cubic foot (PCF). You'll calculate density by dividing the total weight of a foam layer by its volume, which helps you determine the material's suitability for specific applications. Higher density foam tends to provide better pressure relief and comfort.
The density scale typically ranges from 1.5 PCF to 5 PCF or higher, depending on the foam type.
When measuring foam density, you can use traditional weight and volume measurements or advanced methods like terahertz technology, which offers non-contact density measurement without compressing the material. You'll find that different materials may require specific measurement techniques, particularly when dealing with metal foams that use relative density measurements.
The density ranges fall into three main categories: low-density (0.8-1.5 PCF), medium-density (1.5-3.5 PCF), and high-density (3.5-5+ PCF). Each range serves different purposes, with higher densities generally offering greater durability and resilience.
You'll need to think carefully about these density measurements when selecting foam materials, as they directly impact performance, feel, and manufacturing requirements in anti-static packaging applications.
Common Anti-Static Foam Types
When selecting anti-static foam for your packaging needs, you'll encounter four primary types: PE, EVA, EPE, and PU foam. Each type offers distinct characteristics in regard to density, surface resistance, and cell structure to protect your electronic components.
Foam Type | Density | Surface Resistance |
---|---|---|
PE Foam | 45-67 kg/m³ | 10³-10⁵/10⁶-10⁹ Ω |
EVA Foam | 85 kg/m³ | 10³-10⁵ Ω |
EPE Foam | Softer than PE/EVA | 10⁸-10¹¹ Ω |
PU Foam | 2-6 lbs. pcf | Variable |
PE foam features a black color and closed-cell structure, making it ideal for general electronic packaging. You'll find EVA foam offers higher density and comes in various colors, while maintaining excellent conductivity. If you're looking for a softer option, EPE foam provides a non-cross-linked structure and typically comes in pink or red. PU foam stands out with its open-cell structure and is available in pink or charcoal colors. These materials typically have a life span of 5-8 years when properly stored and maintained. When choosing between these options, consider your specific needs for surface resistance and density to guarantee the best protection for your electronic components.
Density Impact On Performance
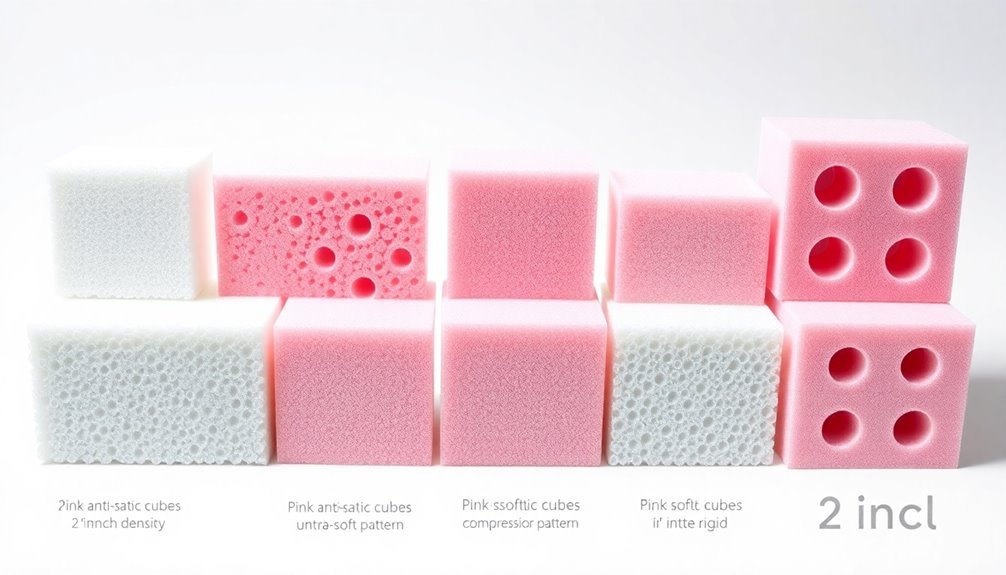
The density of your chosen foam directly influences its performance across multiple essential properties. When you're selecting anti-static foam for your packaging needs, understanding density's impact helps you make informed decisions.
Higher density foams offer superior compression strength and durability, which means your sensitive electronic components receive better protection during shipping and handling. While lower density foams might feel softer initially, they'll likely compress and lose their protective qualities over time. The foam's support factor rating helps determine its ability to prevent bottoming out under heavy loads.
You'll find that density measurements, calculated in pounds per cubic foot, serve as a reliable indicator of foam quality and longevity. Industrial-grade foam at 1.9 lbs offers basic protection, while premium options like high resilience foam at 3.0 lbs deliver exceptional durability for your valuable items.
- Don't risk your expensive electronics with inadequate protection – higher density foams maintain their shape and protective properties longer
- Secure your peace of mind by choosing the right density for your specific application – your products deserve ideal protection
- Save money in the long run by investing in appropriate density foam – prevent damage claims and customer disappointment
Remember that density differs from firmness, so you'll need to take into account both characteristics when selecting your anti-static foam solution.
Comparing ESD Protection Levels
Proper ESD protection levels form a critical framework for safeguarding your electronic components during handling and transport. You'll need to understand both HBM and CDM classifications to guarantee adequate protection for your components.
HBM levels range from 0Z (less than 50V) to 3B (8000V or higher), letting you quickly identify and group components based on their ESD sensitivity. Regular compliance verification testing ensures your ESD protection measures remain effective over time.
When selecting protective foam materials, you'll find different resistance levels that match various protection needs. Conductive foam offers the lowest resistance at 10^3-10^5 ohms, making it ideal for highly sensitive components. Anti-static foam provides moderate protection with 10^6-10^9 ohms, while pink static dissipative foam ranges from 10^8-10^11 ohms.
For system-level protection, you'll want to follow IEC 61000-4-2 standards, which specify requirements like 4 kV contact and 8 kV air discharge protection.
The SEED method helps you guarantee that both external and internal ESD protections work together effectively. Remember that EPP foam can be engineered with either antistatic or conductive properties, giving you flexibility in choosing the right protection level for your specific application.
Weight Distribution Among Foams
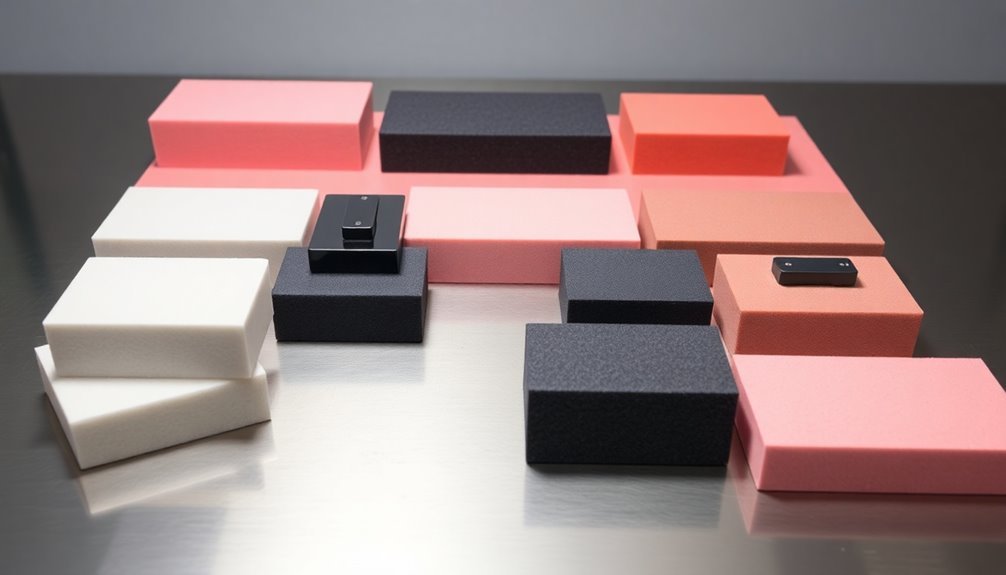
Understanding foam weight distribution starts with recognizing that density doesn't directly equate to overall weight. While density measures mass per unit volume (typically in lbs./ft³ or kg/m³), the total weight of your foam will depend on its size and thickness. Denser materials tend to be more economically viable for extended use applications.
You'll need to take into account both factors when calculating shipping costs or planning installations.
When selecting foam for your application, you'll find that higher-density materials aren't necessarily heavier overall, but they pack more material into each cubic unit. This concentration affects how the foam performs under pressure and over time.
For instance, a low-density foam might be perfect for one-time shipping, while you'll want higher-density options for long-term furniture applications.
- Your foam's longevity depends heavily on proper weight distribution – choosing the wrong density could mean premature sagging and reduced protection.
- You're investing in your product's future when you select appropriate density levels – don't let cost savings today lead to performance issues tomorrow.
- Your shipping costs will directly reflect your foam choices – balance density requirements with practical transportation considerations.
The key is matching density to your specific needs, whether you're protecting sensitive electronics or creating comfortable seating solutions.
Static Control Properties
When selecting foam for static-sensitive items, you'll need to understand the difference between conductive and anti-static varieties, with conductive foam offering more robust protection through its lower resistivity range of 10^3 to 10^5 ohms/cm.
You'll find that anti-static foam properties are substantially influenced by humidity levels, performing better in more humid conditions with its typical resistivity range of 10^10 to 10^12 ohms/cm. Unlike traditional anti-static solutions, permanent static additives provide consistent performance regardless of humidity conditions.
Your choice between these foam types should align with your specific static protection requirements, considering factors like item sensitivity, handling frequency, and environmental conditions.
Understanding Static Protection Levels
Static protection in foam packaging plays an essential role in safeguarding sensitive electronic components from electrostatic discharge (ESD) damage. You'll find that protection levels vary based on the material's surface resistance, which typically ranges from 1.0 x 10^3 to 1.0 x 10^11 ohm/sq.
When you're selecting foam packaging, you'll need to evaluate three main types: anti-static, dissipative, and conductive materials. The growing electronics market continues to drive increased demand for these protective solutions.
To achieve these protective properties, manufacturers incorporate static control additives like Ionphase for long-term protection and Atmer for temporary applications. You can verify the effectiveness of your chosen packaging by ensuring it meets IEC 61340 standards and ANSI/EOS/ESD S11.11-2001 requirements, which specify surface resistance ranges for adequate ESD protection.
Protect your valuable electronics with packaging that's proven to withstand discharges up to 20 kV.
Trust in scientifically-tested materials that actively prevent static buildup and discharge.
Safeguard your investment with foam materials that create a protective Faraday cage effect.
Different manufacturing environments require specific levels of protection, so you'll need to match your foam's static protection properties to your product's electrostatic sensitivity requirements.
Conductive Vs Anti-Static Foam
Selecting the right static control foam requires understanding key differences between conductive and anti-static varieties. You'll notice conductive foam is black due to its carbon content, while anti-static foam typically comes in pink.
The key distinction lies in their surface resistance and how they handle static charges.
Conductive foam offers surface resistance less than 10^6 ohms and acts as a Faraday cage, blocking electromagnetic fields. While it's highly effective, you'll need to be careful as it can drain batteries if they come in contact with the foam's conductive ends. The material's high carbon content makes it especially durable for repeat use applications.
Anti-static foam, with surface resistance between 10^9 and 10^12 ohms, prevents static buildup while allowing charges to pass through.
For controlled static dissipation, you might consider static dissipative foam, which offers middle-ground protection with resistance between 10^5 and 10^9 ohms. It's available in both carbon-impregnated black and surface-treated pink varieties.
When choosing your foam, consider that conductive foam works best for high conductivity needs, while anti-static foam suits moderate static control requirements. Remember that pink anti-static foams may require additional shielding and can lose effectiveness over time.
Humidity Impact Factors
Beyond choosing the right foam type, understanding humidity's role in static control can greatly impact your material's effectiveness. When you're working with anti-static packaging materials, humidity levels between 40% and 60% RH provide the best protection against electrostatic discharge.
In low humidity conditions (below 30% RH), you'll notice increased static buildup, which can compromise your components' safety.
Your anti-static foam's performance directly correlates with ambient moisture levels. Materials featuring "sweat layers" become more effective in humid conditions, while conductive foams maintain consistent performance across varying humidity levels.
You'll need to take into account that office air conditioning can create problematically dry environments, unlike the controlled conditions of manufacturing facilities.
- Your sensitive electronics face up to 100x higher risk of ESD damage in low-humidity environments
- You're losing significant protection when humidity drops below 20% RH, even with anti-static materials
- Your packaging investment could be compromised without proper humidity control
Temperature variations affect surface resistivity, so you'll want to monitor both humidity and temperature in your storage areas. For critical applications, consider implementing precision humidity control systems to maintain the best protective conditions for your anti-static packaging materials.
Foam Material Selection Guide
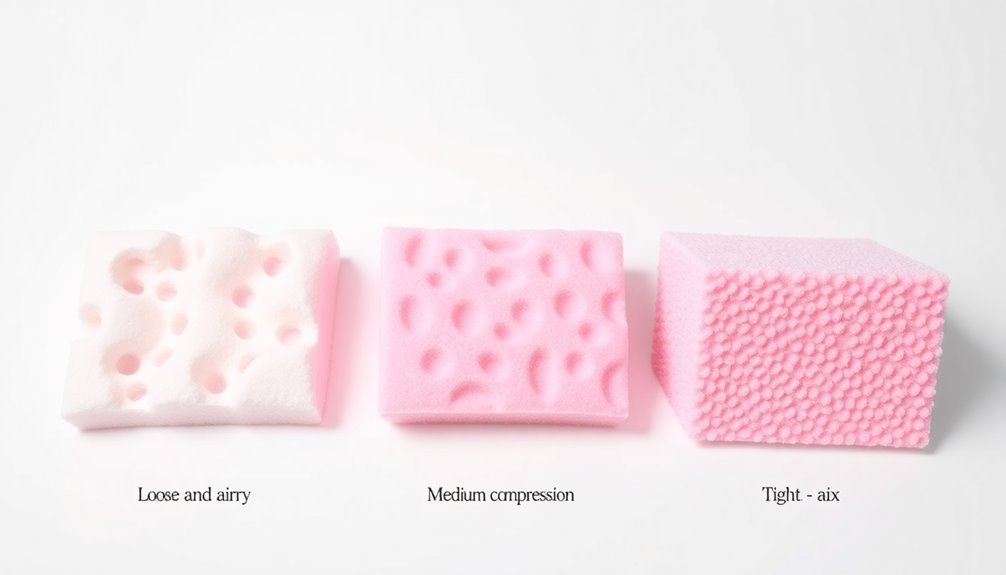
Success in foam packaging hinges on choosing the right material for your specific needs. When selecting foam materials, you'll need to take into account several critical factors, including density, cell structure, and specific application requirements.
For fragile items, you'll want to opt for polyurethane foams, which offer excellent shock absorption and flexibility.
If you're packaging items with sharp edges, Edge Armor's dual-density polyethylene construction provides targeted protection where it's needed most.
For heavier objects, standard polyethylene foam delivers reliable protection at a reasonable cost.
Your selection should also account for density requirements. High-quality open-cell polyurethane starts at 0.8LB density, while 2.8LB represents the premium end of the spectrum.
You'll find that closed-cell foams offer superior protection against moisture and gases, making them ideal for sensitive electronics or moisture-prone items.
For electronic components requiring anti-static protection, you'll need to take into account specialized ESD-safe foams like PE, EVA, or PU variants. These materials come in specific densities (45kg/m³ or 67kg/m³) and provide the necessary electrostatic discharge protection.
Remember to calculate your product's static loading and G-factor to guarantee maximum protection levels.
Manufacturing Process Effects
Cross-linking in foam manufacturing strengthens your material's structure, creating a more stable and durable product you can rely on.
You'll find that proper cell structure development during manufacturing directly impacts your foam's performance characteristics, including compression resistance and recovery properties.
Your foam's overall integrity depends heavily on achieving the right balance of cross-linking agents and controlling cell formation throughout the manufacturing process.
Cross-Linking Creates Stability
The stability of foam relies heavily on molecular cross-linking during manufacturing. You'll find that higher cross-link density substantially improves your foam's compression strength, temperature resistance, and dimensional stability.
When manufacturing foam, you'll want to aim for polyols with M/f values between 75 and 150 to avoid brittleness while maintaining peak performance.
You can enhance your foam's mechanical properties through cross-linking agents like diethanolamine, which markedly improves the rebound rate. However, you'll need to carefully monitor the MC value, as anything below 1200 will result in poor compression set values.
The process creates a direct relationship between cross-link density and strength, though you'll notice lower elongation rates in heavily cross-linked foams.
- Imagine achieving up to 40% better compression strength with proper cross-linking
- Think about the satisfaction of creating foam that maintains its shape even under extreme conditions
- Consider the competitive advantage of producing foam that outperforms standard alternatives
When working with cross-linked foams, you're balancing between stability and flexibility. The density of aromatic rings, urethane, and urea groups will influence your foam's high-temperature performance, so you'll need to adjust these factors based on your specific application requirements.
Cell Structure Impacts Performance
Understanding cell structure proves critical when manufacturing high-performance foam, as both size and distribution directly influence material strength. You'll find that smaller cell sizes increase both tensile and impact strengths, with reductions in cell diameter showing up to 30% improvement in impact resistance.
When you're manufacturing foam, you'll need to control your expansion process parameters carefully. Steam pressure, temperature, and dwell time work together to determine your final cell structure and density. Higher pressures and temperatures create more expansion and lower density, while lower settings produce denser foam.
Process Parameter | Effect on Structure | Performance Impact |
---|---|---|
High Steam Pressure | Increased Expansion | Lower Density |
Extended Dwell Time | Larger Cell Size | Reduced Strength |
Chemical Additives | Controlled Distribution | Enhanced Properties |
To maintain consistent quality, you'll want to monitor these parameters continuously. Regular testing of both raw materials and finished products confirms you're meeting specifications. Remember that ambient conditions like humidity and temperature can affect your results, so maintain strict environmental controls throughout the manufacturing process.
Foam Durability Factors
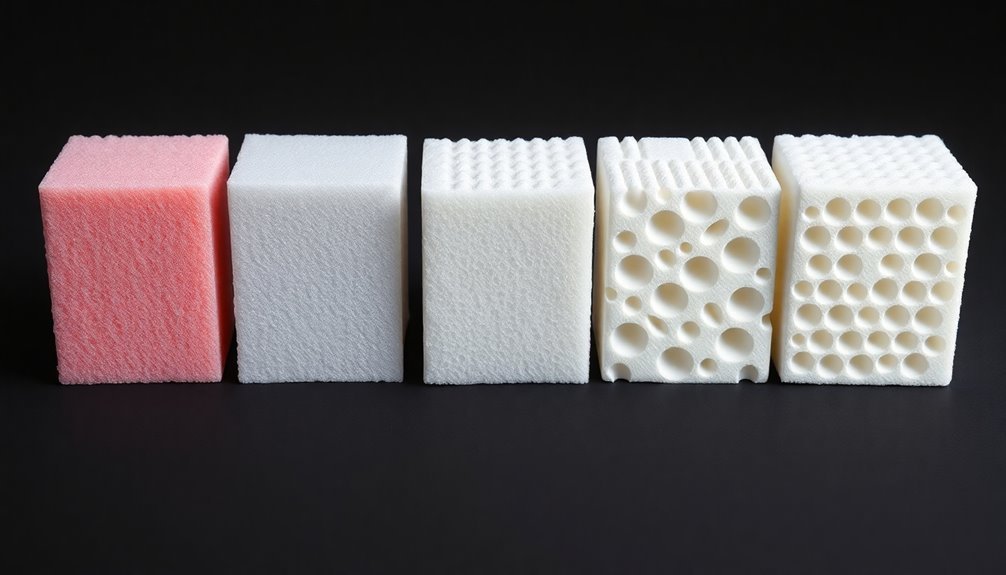
Durability of foam materials depends on several key factors that work together to determine their longevity and performance. You'll find that density plays an essential role, as higher-density foams typically offer better durability and longer-lasting support.
The manufacturing process and material selection are equally important, with polyurethane foams standing out for their exceptional durability when properly produced.
Environmental conditions can markedly impact your foam's lifespan. You'll need to protect it from moisture, extreme temperatures, and harsh chemicals that can break down its structure. If you're using foam in areas with high humidity or temperature fluctuations, closed-cell varieties will serve you better due to their superior moisture resistance.
Your foam's durability directly affects your bottom line – don't risk equipment damage with inferior materials.
Poor foam quality can lead to costly replacements and potential product damage during shipping.
Installing high-quality foam correctly the first time saves you money and headaches in the long run.
Testing and proper installation are fundamental for ensuring top performance. You should look for foams that have undergone rigorous flex fatigue and tensile strength testing, as these measurements provide reliable indicators of long-term durability.
Regular maintenance and proper handling will help extend your foam's useful life.
Storage Environment Considerations
Proper storage environments play a critical role in maintaining foam quality and performance over time. You'll need to store your foam materials in a dry, cool, and well-ventilated area to prevent deterioration and maintain their protective properties.
Keep the storage space away from any ignition sources, including sparks and open flames, to guarantee safety.
Always store foam products on raised pallets to prevent moisture accumulation from ground contact. You'll want to use suitable packaging like bulk containers, boxes, or PE bags for storage.
When shipping foam, make sure you're using ventilated trailers to prevent vapor or dust buildup.
Environmental factors substantially impact foam storage conditions. Don't expose your foam to direct sunlight or outdoor weather conditions, as these can cause damage.
You'll need to maintain proper ventilation to control humidity levels and prevent moisture accumulation. After opening storage area doors, allow proper air circulation to control vapor emissions.
Regular inspection of your stored foam is essential. You should check for signs of damage or degradation periodically.
When handling foam materials, do so with care to prevent unnecessary damage during storage and guarantee optimal performance when needed.
Frequently Asked Questions
Can Anti-Static Foam Be Recycled or Reused Safely?
Yes, you can safely recycle and reuse anti-static foam. You'll need to follow specific recycling processes where EVA foam can be transformed into smaller pieces, while PU foam gets ground into new products.
What Cleaning Methods Are Safe for Maintaining Anti-Static Foam Properties?
You'll need to spray antistatic cleaners onto a cloth, not directly on the foam. Wipe gently and avoid harsh chemicals. Always use ESD-safe products to maintain the foam's protective properties.
How Long Does Anti-Static Foam Maintain Its Protective Properties?
You'll typically get 1-3 years of protection from anti-static foam, with premium products like ETHAFOAM AS lasting over 3 years. However, your storage conditions and handling practices will affect its longevity.
Does Cutting Anti-Static Foam Affect Its Static-Control Capabilities?
You can safely cut anti-static foam without compromising its protective properties. The static-control additives remain integrated throughout the material, so your cut pieces will maintain their original dissipative capabilities and surface resistivity.
Are There Temperature Limitations for Using Different Types of Anti-Static Foam?
You'll find most anti-static foams work best between -10°C and 85°C. Be careful when using them above 49°C, as they'll start to soften. Don't exceed 70°C for extended periods to maintain stability.
In Summary
You've now learned how foam density directly affects your ESD packaging choices. When selecting anti-static materials, you'll want to take into account both density measurements and performance requirements. Don't forget to factor in your storage environment and weight distribution needs. Remember, the manufacturing process impacts durability, so choose your foam type carefully. By comparing density levels and protection ratings, you'll make the right selection for your packaging needs.
Leave a Reply