You'll need to budget between $100-1,250 per square foot to set up proper cleanroom charge monitoring, with costs varying based on your facility's requirements. Basic equipment like anti-static PPE starts around $100, while advanced monitoring systems can add $50-150 per square foot. Your location, facility size, and compliance needs will impact installation expenses. Don't forget ongoing costs – maintenance, data management, and alert systems can run from $2,000-15,000, plus monthly subscriptions of $100-500. Understanding the complete cost breakdown will help you make smarter investment decisions for your specific situation.
Basic Static Control Equipment Costs
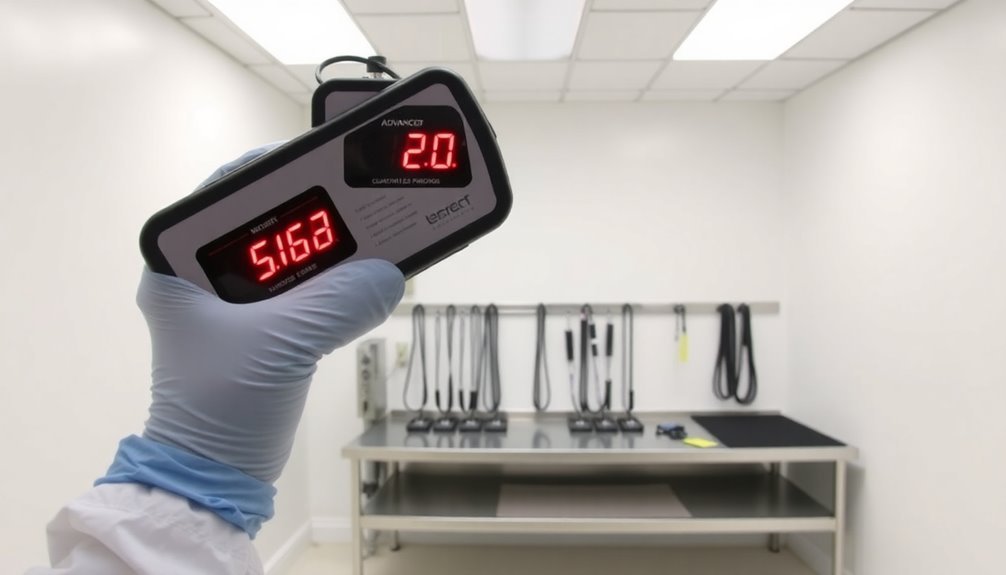
A cleanroom's basic static control equipment represents the foundation of ESD protection measures. When you're setting up your static control system, you'll need to invest in essential personal protective equipment (PPE) that prevents static discharge during operations.
Your basic PPE costs will include anti-static gloves at $4.19 per pair, lab coats starting at $36.99, and finger cots from $18.99. You'll also need anti-static swabs starting at $19.99 and wipes from $14.97 to maintain cleanliness without generating static charges. These items form your first line of defense against ESD events.
To create a protected work environment, you'll need ESD-safe workstations and chairs, though prices vary by manufacturer. ESD matting and flooring are vital components, and you'll need to connect them using grounding cables at $9.99 each. Like many specialized equipment solutions, choosing the right static control components requires careful cost analysis considerations to ensure maximum value for your investment.
Don't forget ESD-safe shoes, which cost around $51.99 – they're important for maintaining a continuous ground connection for personnel.
These basic components work together to create a thorough static control system. While initial costs may seem substantial, they're markedly less expensive than potential damage from uncontrolled static discharge events.
Installation and Setup Price Factors
When you're planning a cleanroom charge monitoring system installation, you'll need to factor in location-specific costs including travel expenses for technicians and shipping of specialized equipment to your site.
Your site preparation requirements will greatly impact the total cost, as proper electrical infrastructure, ventilation systems, and structural modifications may be necessary to support the monitoring equipment.
The technical complexity of integrating new monitoring systems with your existing cleanroom infrastructure can drive up installation costs, particularly if custom programming or specialized interfaces are needed. Implementing wireless monitoring solutions can significantly reduce installation complexity and associated labor costs compared to traditional hardwired systems.
Location and Travel Costs
Location and travel expenses greatly impact the overall costs of cleanroom charge monitoring installations. You'll find that your facility's location, size, and layout directly influence both initial setup and ongoing maintenance costs. Different cleanliness levels across various areas of your cleanroom can drive costs from $1,500 to $6,000 per square meter for traditional setups, while modular solutions range from $100 to $150 per square foot.
Location Factor | Cost Impact | Consideration |
---|---|---|
Cleanliness Level | High | ISO classification requirements |
Site Accessibility | Medium | Equipment transportation needs |
Regional Variables | Medium | Local regulations and resources |
When planning your cleanroom installation, you'll need to account for specialized labor travel costs, including accommodations and per diems. Your site's accessibility can notably affect equipment transportation expenses, particularly for heavy or sensitive monitoring components. If you're in a remote location, you'll face higher costs for both initial installation and recurring maintenance visits. The availability of local infrastructure, especially adequate power supply for heating and cooling systems, will influence your overall expenses. Implementing Fan Filter Units can significantly reduce installation costs compared to traditional central air handling systems. You'll also need to take into account that time-sensitive installations might require premium rates for expedited travel and labor arrangements.
Site Preparation Requirements
Site preparation requirements consistently drive essential portions of your cleanroom charge monitoring costs.
You'll need to carefully evaluate your existing floor conditions, particularly whether you have level concrete flooring, as this directly impacts installation expenses. Physical obstacles like columns and low truss heights can complicate the setup process and increase labor costs.
Your site's accessibility plays a vital role in determining installation expenses. If you're installing in a challenging location, such as a high-rise building or an area with limited access, you'll face increased logistical costs. Additional costs of up to $300 per square foot may apply for unique installations in challenging locations.
You'll also need to assess your building's existing environmental control systems, as they can either reduce or elevate your HVAC requirements and associated costs.
The availability and configuration of power outlets at your site greatly affect your setup expenses. You'll need to take into account whether you have the right electrical setup for your monitoring equipment, including proper phasing and capacity.
If you're in a seismic zone, you'll need to factor in additional costs for required modifications and endorsements.
Don't forget to assess your HVAC integration needs, as connecting your cleanroom's system with the building's existing infrastructure can add considerable complexity and cost.
Technical Integration Complexity
Technical integration complexity considerably drives your cleanroom monitoring costs through various interconnected factors.
When you're integrating a monitoring system, you'll need to take into account how it interfaces with your existing infrastructure and equipment. Systems like JUMO mTRON T offer modular inputs and outputs, but you'll still face challenges in guaranteeing seamless communication between components. The need for continuous documentation compliance has made these systems an essential part of quality management.
Your technical integration costs will largely depend on your system's configuration choices. While decentralized setups can reduce installation complexity and costs, you'll need to balance this against your need for centralized control.
Fast Ethernet-based systems like EtherCAT can streamline data communication, but they'll require proper networking infrastructure.
The complexity of your system's tamper-proof documentation requirements and GMP compliance features will also impact costs. You'll need to verify your setup provides secure, long-term data retention while maintaining audit safety.
Additionally, you'll want to factor in the time and resources needed for staff training on new interfaces. While intuitive operating concepts can help minimize training periods, you'll still need to account for the learning curve as your team adapts to the new system.
Monitoring System Size Requirements
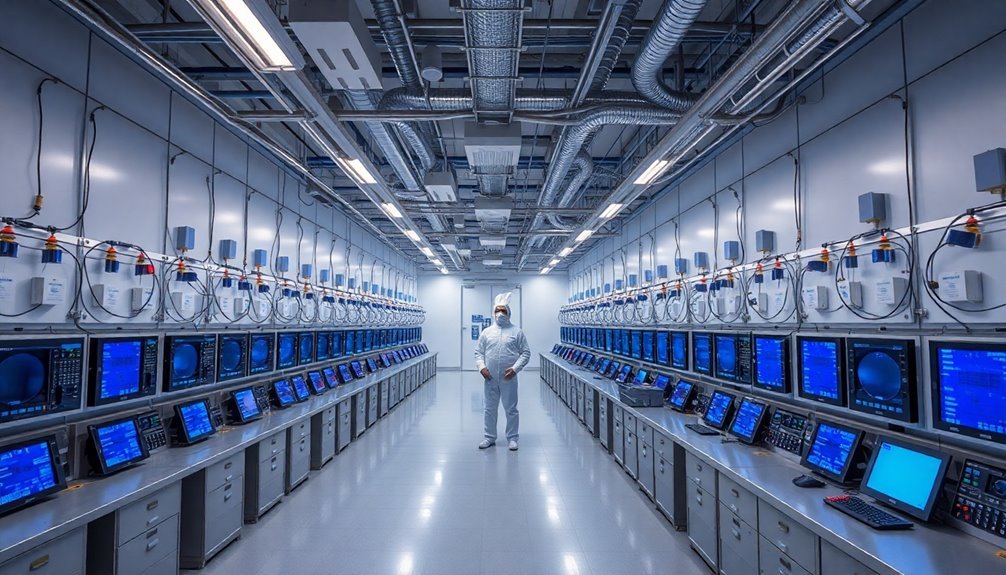
When determining your cleanroom monitoring costs, you'll need to analyze the total square footage to calculate the number and placement of particle counters needed for complete coverage.
Your sensor coverage requirements will vary based on ISO classification, with stricter cleanroom grades requiring more monitoring points per square meter to maintain compliance.
You can minimize future expenses by choosing a scalable monitoring system that lets you add sensors and expand coverage zones without replacing the entire infrastructure. Involving stakeholders from different departments helps ensure monitoring requirements are accurately defined for your facility's unique needs.
Square Footage Impact Analysis
Inside cleanroom facilities, the square footage directly influences monitoring system requirements and complexity. Your cleanroom's classification, from ISO 1 to ISO 9, determines specific particle count limits and air change rates that affect your monitoring system's scope. The larger your cleanroom space, the more extensive your particle counting and environmental monitoring equipment must be. A standard ISO 7 cleanroom requires 60 HEPA air changes per hour for proper monitoring and control.
When analyzing square footage impact, you'll need to evaluate these critical factors:
- Air changes per hour requirements that scale with room size, affecting the number and placement of monitoring points.
- Equipment space allocation, including proper dimensions for monitoring devices and their associated tubing systems.
- Filter coverage needs based on CFM per square foot calculations, which vary by cleanroom classification.
Your monitoring system's physical setup must accommodate the specific requirements of your space while maintaining accuracy and reliability.
You'll need to verify your particle counters meet ISO classification standards and can effectively monitor your entire cleanroom area. The URS should clearly specify available space dimensions and equipment capacity requirements, taking into account both "at rest" and "in operation" conditions for GMP facility grades.
Sensor Coverage Requirements
Throughout your cleanroom facility, proper sensor coverage directly impacts both compliance and operational efficiency. You'll need to carefully evaluate which monitoring parameters are essential for your specific operations, as configurations can range from basic room pressure monitoring to extensive systems that track multiple variables.
Your sensor requirements will depend on your regulatory obligations under ISO 14644, cGMP, USP, and FDA standards. For basic setups, you might only need pressure sensors, but if you're handling temperature-sensitive materials or maintaining specific environmental conditions, you'll require temperature and humidity sensors as well. Particle counting sensors are crucial for maintaining product quality and detecting potential contamination risks.
Don't forget specialized monitoring needs, such as refrigerator temperature sensors for cold storage areas.
Consider your installation options carefully. If you're working with an existing facility, WIFI-based systems can offer more flexibility and easier installation compared to hardwired solutions that require ceiling grid removal and licensed electricians.
When placing sensors, you'll need to account for potential interference sources and protect humidity sensors from direct moisture exposure. Your system should also allow for future expansion through modular upgrades, ensuring you won't need a complete overhaul as your monitoring needs grow.
Scalability Assessment Factors
Building upon your sensor coverage plan, you'll need to evaluate the scalability of your monitoring system to ascertain it meets both current and future requirements. Your assessment should focus on how your monitoring infrastructure can expand alongside your cleanroom operations while maintaining compliance with ISO 14644-2 standards.
Start by analyzing your cleanroom's modular design elements and equipment specifications to determine your scaling potential. You'll want to reflect on both physical expansion capabilities and data management requirements.
When evaluating scalability factors, focus on these critical areas:
- Infrastructure Capacity – Confirm your monitoring system's backbone can handle additional sensors, network connections, and utility requirements without requiring a complete overhaul.
- Data Management Flexibility – Your system should easily accommodate increased data volume from new monitoring points while maintaining efficient processing and storage capabilities.
- Equipment Interchangeability – Select monitoring components that are standardized and interchangeable to facilitate future upgrades without compatibility issues.
Remember to document your scalability assessment findings thoroughly, as they'll inform your investment decisions and help justify costs associated with implementing a more robust, future-proof monitoring system.
Long-Term Maintenance Expenses
Managing long-term maintenance expenses requires a strategic approach to balance operational efficiency with cost control.
You'll need to account for routine expenses like cleaning, sanitization, filter replacements, and equipment calibrations that accumulate considerably over time. Your ongoing costs will also include consumables and energy consumption for HVAC systems.
You can reduce these expenses by implementing preventive maintenance programs and upgrading to energy-efficient systems. Consider bulk purchasing consumables and optimizing your cleaning protocols to save both time and money.
You'll find that investing in automated monitoring systems and digital maintenance logs helps prevent larger issues while streamlining documentation.
Your compliance and validation requirements will considerably impact your maintenance budget. You'll need to maintain continuous documentation and undergo periodic validations, which become more stringent and frequent with higher classification levels.
To manage these costs effectively, you'll want to focus on employee training to minimize mistakes and implement analytics for predicting maintenance needs.
Don't forget that energy recovery solutions in your HVAC systems can help optimize power usage and reduce long-term operational costs.
Essential Components and Their Prices
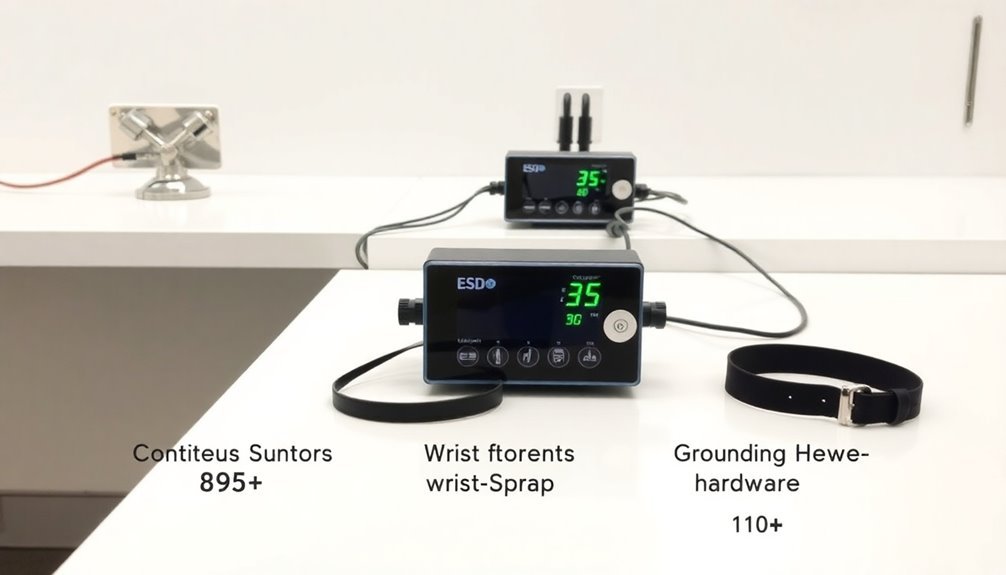
Proper cleanroom charge monitoring relies on several key components that work together as an integrated system.
You'll need particle counters that use laser beam technology, temperature sensors with thermal sensing capabilities, and pressure sensors featuring piezoelectric or capacitive technologies. These components form the backbone of your monitoring infrastructure, with costs varying considerably based on quality and specifications.
When considering the essential monitoring equipment, you'll encounter these typical price ranges:
- Basic monitoring package: Includes particle counters and environmental sensors at $32/hr for academic use, scaling up to $60/hr for commercial applications.
- Advanced monitoring systems: Features integrated data logging and reporting capabilities, with remote staff assistance adding $100/hr to your operational costs.
- Specialized equipment: Items like Scanning Electron Microscopes cost $44/hr for academic use and $105/hr for commercial applications.
You'll need to factor in the networking infrastructure that connects these components to your central monitoring hub.
While the initial investment might seem steep, it's vital to remember that accurate monitoring directly impacts product quality and regulatory compliance.
The type of sensors you choose will depend on your specific cleanroom classification and monitoring requirements.
Data Logging Technology Investment
Data logging technology represents a substantial portion of your cleanroom monitoring investment, with costs ranging from ₹11,025 to ₹16,275 for advanced systems.
You'll need to take into account several technology options, including digital data loggers for real-time recording, wireless systems for remote monitoring, and Ethernet-connected loggers for secure data collection.
Your investment will extend beyond initial equipment costs.
You'll need to budget for software licensing fees, particularly for specialized analysis tools from providers like Delphin Technology AG.
Installation and setup charges can add significant costs, especially if you're implementing complex systems that require professional expertise.
Don't forget about ongoing maintenance and calibration expenses to guarantee your equipment remains accurate and reliable.
The ROI justifies these costs through multiple benefits.
You'll see reduced manual logging errors, improved compliance with FDA and GMP guidelines, and enhanced risk management through continuous monitoring.
Your operational efficiency will increase with real-time data access, and you'll save money through optimized cleanroom operations.
Choose systems that offer scalability and verify they integrate with your existing infrastructure while maintaining robust data security measures.
Real-Time Alert System Pricing
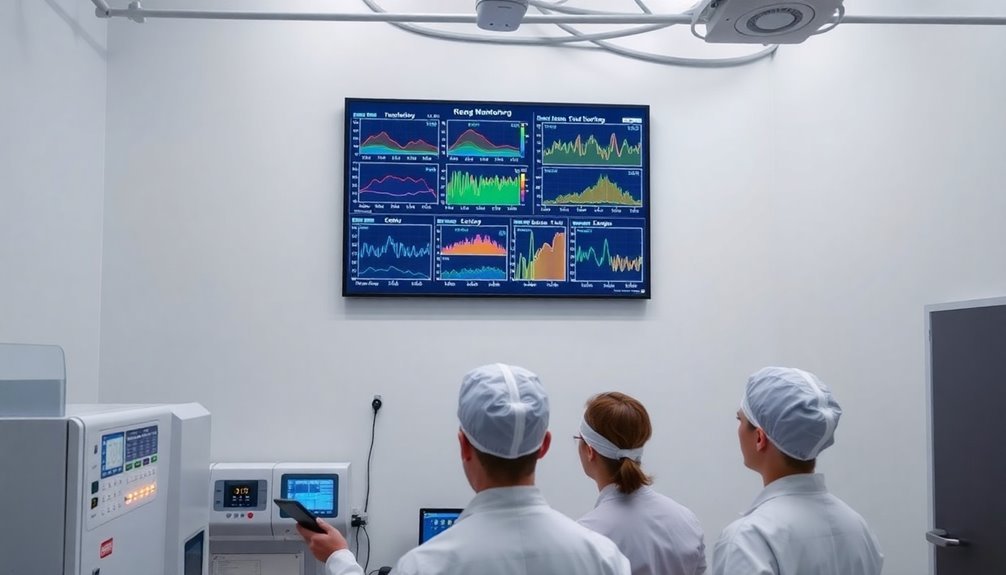
You'll find that real-time alert systems for cleanroom charge monitoring come with varying hardware costs, including sensors, control units, and display interfaces ranging from $2,000 to $15,000 based on coverage area.
When considering subscription services, most vendors offer tiered pricing from basic monitoring at $100/month to advanced analytics packages at $500/month, with features like automated reporting and compliance tracking.
Mobile integration expenses typically add $1,000-3,000 to your initial setup, covering app development, push notification capabilities, and secure data transmission protocols.
Alert Hardware Cost Breakdown
Real-time alert system hardware comes with varying price structures that include both upfront and monthly costs.
You'll find that Lively devices require an initial equipment fee ranging from $79.99 to $119.99, plus a $35 activation fee. Life Alert's hardware costs are more complex, requiring professional installation for their Master Unit and an additional $20 monthly fee for their Mobile + GPS option.
When comparing hardware expenses, you'll want to evaluate these key factors:
- Upfront Equipment Costs: Entry-level devices like the Lively Mobile2 and Jitterbug Flip2 start at $79.99, while the Jitterbug Smart4 costs $119.99.
- Installation Requirements: Life Alert systems need professional installation, which adds to your initial investment.
- Warranty Coverage: Lively provides a one-year warranty on their equipment, protecting your investment.
You won't need to commit to long-term contracts with Lively, giving you more flexibility.
The hardware operates on Verizon's network for reliable cellular coverage, and you can add optional features like GPS tracking and additional alert buttons to customize your system.
Watch for seasonal promotions that could reduce your initial hardware costs.
Subscription Service Price Tiers
Beyond the initial hardware investment, subscription service tiers form the backbone of ongoing alert system costs.
You'll typically encounter several pricing structures that impact your total expenditure, including flat subscription fees based on user count and message-based charges that factor in your alert volume.
Most providers offer tiered service levels, ranging from essential monitoring to extensive enterprise solutions. You'll find that basic tiers start with a minimum number of protected nodes, like Alert Logic's 25-node baseline, while higher tiers incorporate advanced features and dedicated support.
Your actual costs will vary based on your organization's specific needs and usage patterns.
The pricing model you'll encounter often combines multiple factors. You're charged for the number of users accessing the system, the volume of alerts generated, and any additional features you require.
For instance, you might pay per CRPU-hour for specialized services like AWS Clean Rooms at $4.00 per hour.
Watch for potential overage fees if you exceed your allocated message limits. Consider scalability in your decision-making process, as most services allow you to adjust your subscription level as your needs change.
Mobile Integration Expenses
Mobile integration costs for cleanroom alert systems comprise several essential components that affect your total investment. When you're planning to implement mobile monitoring capabilities, you'll need to account for both the initial setup and ongoing operational expenses.
The system's complexity and your specific monitoring requirements will greatly influence the final cost structure.
Your mobile integration expenses will typically depend on three primary factors:
- Connectivity Requirements: You'll need to budget for Wi-Fi or cellular connectivity infrastructure, which varies based on your facility's size and coverage needs.
- Real-Time Monitoring Features: The more sophisticated your monitoring needs, the higher the cost – from basic parameter alerts to extensive data analysis capabilities.
- Mobile App Development and Maintenance: Whether you're using vendor-provided apps or custom solutions, you'll need to factor in development, updates, and ongoing support costs.
While mobile integration might seem costly upfront, it's often cost-effective in the long run.
You'll benefit from reduced labor costs through automation, immediate response capabilities, and enhanced compliance tracking.
The key is to choose a solution that matches your specific monitoring requirements while providing scalability for future expansion.
Environmental Factors Affecting Costs
Environmental factors play a decisive role in determining both initial and ongoing cleanroom charge monitoring costs.
You'll find that temperature and humidity control requirements greatly impact your expenses, as they demand sophisticated HVAC systems and specialized equipment like chillers and air handling units. These systems not only require substantial upfront investment but also drive up your energy consumption and maintenance costs.
Air filtration represents another major cost factor you'll need to take into account. Your cleanroom will require high-efficiency HEPA or ULPA filters, along with proper air change rates and systems to control VOCs and toxic gases.
You'll also need to budget for separate ductwork and regular filter replacements.
Your environmental monitoring systems will add another layer of expense, including equipment to track temperature, humidity, and air quality. If you need vibration control or chemical extraction systems, expect additional costs.
The location of your cleanroom matters too – remote sites or urban areas can increase your construction and operational expenses due to logistics and accessibility challenges.
Reflect on whether your site has existing infrastructure, as installing new services like compressed air or medical gas lines will impact your total costs.
Facility Integration Cost Breakdown
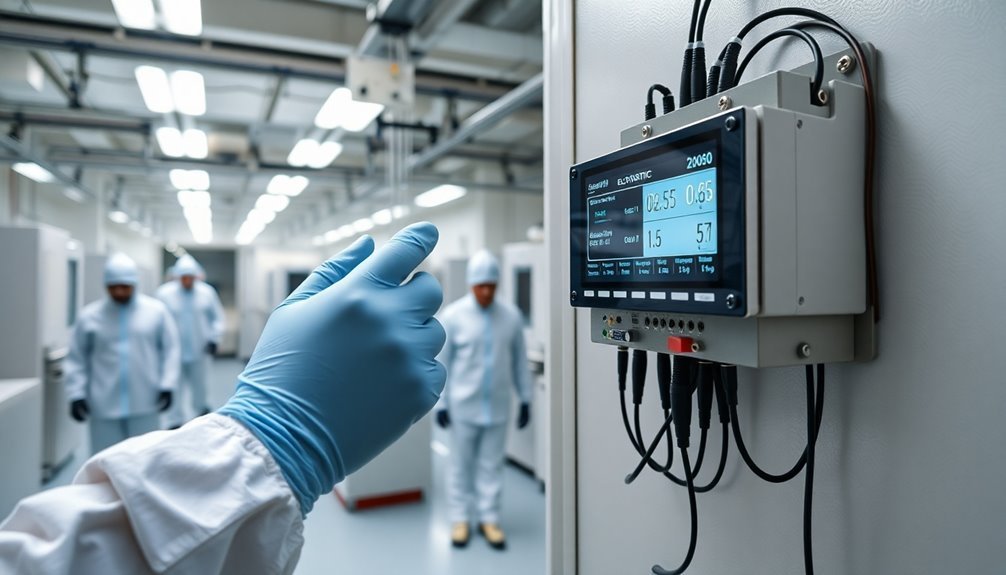
Breaking down facility integration costs reveals considerable variations in cleanroom implementation expenses.
When you're planning to integrate a cleanroom into your facility, you'll need to account for both immediate installation costs and long-term operational expenses. Base installation costs typically range from $100 to $1,000 per square foot, but GMP-compliant facilities can push that figure to $1,250 per square foot.
Your total facility integration costs will depend on several key components:
- HVAC system implementation and integration ($250-500 per square foot)
- Monitoring and control systems setup ($50-150 per square foot)
- Custom features and specialized equipment ($100-300 per square foot)
You'll find that equipment costs vary considerably based on your specific needs, with assisted rates running $50/hour for internal operations and $100/hour for external support.
When integrating these systems, you're looking at annual operating costs around $1 million for a Class 10 environment. The integration of air filtration systems, specialized lighting, and advanced control systems will add to your base costs, but they're essential for maintaining required cleanliness levels and ensuring proper facility operation.
Return on Investment Analysis
While facility integration represents a major expense, understanding the return on investment helps justify these substantial costs. You'll find that smart cleanroom monitoring delivers substantial long-term savings through improved efficiency, reduced contamination risks, and streamlined compliance processes.
ROI Category | Financial Impact |
---|---|
Operational Savings | Reduced manual labor costs, lower energy consumption through smart HVAC control |
Risk Mitigation | Decreased product loss, fewer regulatory fines, minimized contamination incidents |
Asset Longevity | Extended equipment life through predictive maintenance, reduced replacement costs |
Your investment in smart monitoring technology pays off through multiple channels. You'll see immediate benefits in productivity as automated systems replace manual logging and provide real-time alerts for deviations. The predictive maintenance capabilities will extend your equipment's lifespan while preventing costly breakdowns. Digital twin technology enables process optimization, leading to reduced operational costs over time.
When calculating ROI, consider that effective monitoring systems typically reduce facility downtime, improve product quality, and guarantee consistent regulatory compliance. These benefits translate into quantifiable savings that often exceed the initial investment within a reasonable timeframe, despite the significant upfront costs.
Frequently Asked Questions
How Does Cleanroom Monitoring Impact Employee Productivity and Workflow Efficiency?
While you'll face reduced employee morale and increased stress from monitoring, you'll gain significant workflow benefits through automated data collection, real-time contamination control, and streamlined processes that enhance overall operational efficiency.
Can Existing Building Management Systems Be Integrated With Cleanroom Monitoring?
Yes, you can integrate your existing building management systems with cleanroom monitoring. You'll benefit from shared sensors, real-time data exchange, and streamlined operations, though you'll need to address technical compatibility and data consistency challenges.
What Are the Insurance Implications of Different Cleanroom Monitoring Systems?
You'll find your insurance premiums are influenced by your monitoring system choice. Better systems with real-time alerts and data storage typically lower your liability risks and can reduce your coverage costs considerably.
How Do Regulatory Changes Affect Monitoring System Upgrade Requirements?
You'll need to upgrade your monitoring systems when regulations like Annex 1 and 21 CFR Part 11 change. These updates often require continuous monitoring, better data management, and enhanced sensor capabilities for compliance.
What Training Costs Are Associated With New Cleanroom Monitoring Technology?
You'll need to budget £236-£1,695 for initial training courses, depending on duration. Don't forget early enrollment discounts of 20%. Consider both one-day online sessions and extensive three-day virtual cleanroom training programs.
In Summary
You'll find that cleanroom charge monitoring costs vary considerably based on your facility's size and requirements. While initial equipment expenses of $5,000-$15,000 might seem steep, they're offset by reduced product loss and improved quality control. Factor in yearly maintenance costs of $2,000-$4,000 and potential system upgrades. When properly implemented, you can expect ROI within 12-18 months through prevented static-related damage.
Leave a Reply