You'll see significant cost reductions in protective packaging by optimizing material selection, choosing appropriately sized packaging for each product, and eliminating excess void fill. Investing in automated packaging systems can reduce labor costs while ensuring consistent quality. Standardizing your packaging dimensions helps secure bulk purchasing discounts and streamlines logistics operations. Building strong supplier relationships enables better pricing through economies of scale. Implementing sustainable solutions, like recyclable materials and custom-sized packaging, cuts both environmental impact and operational expenses. These strategic changes could save your business 25-40% on packaging costs – and that's just the beginning.
Optimize Material Selection and Storage
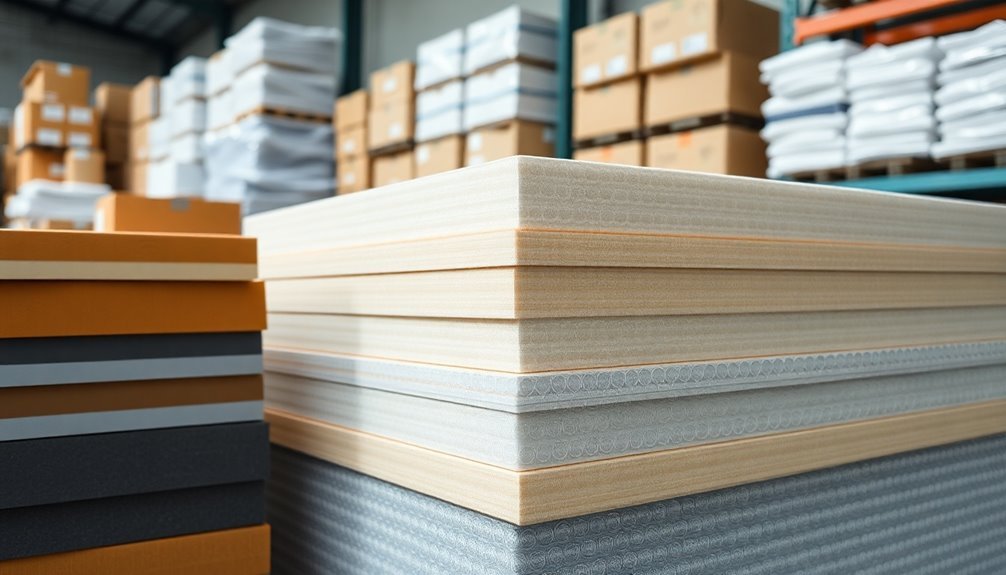
Businesses looking to cut packaging costs should start with strategic material selection and storage optimization.
You'll find that plastic materials like bubble wrap and poly mailers typically cost less than paper-based options, though eco-friendly alternatives can offer better long-term savings. Evaluate materials that can be customized to different strengths, allowing you to match protection levels to specific product needs without overspending. Consider using anti-static bags for electronics to prevent costly damage claims and returns.
To maximize cost savings, implement a diverse packaging strategy. You'll want to stock various sizes and material types to properly protect different products while minimizing waste.
For instance, flat poly bags work well for certain items, while corrugated bubble or honeycomb paper might be better for others. Don't forget to assess eco-friendly options like GreenWrap or Flexi-Hex Air Sleeves, which can be both cost-effective and environmentally responsible.
Focus on right-sizing your containers and storage space. You'll reduce material waste and shipping costs by choosing appropriately sized packaging for each product.
This approach not only minimizes excess material usage but also optimizes warehouse space and reduces logistics expenses. Remember to weigh both immediate costs and long-term benefits when selecting your packaging materials.
Invest in Automated Packaging Systems
Today's competitive market demands smarter packaging solutions, and automated systems offer a compelling return on investment. By implementing automated packaging systems, you'll substantially reduce labor costs while ensuring consistent package quality across your operations.
You'll notice immediate improvements in productivity as these systems handle time-consuming tasks with precision and speed. The integration of inline packaging systems allows products to be packaged directly on the production line.
You can expect substantial savings in material usage, as automated systems optimize packaging designs and eliminate excess void-fill materials. They're programmed to use exactly what's needed, reducing waste and associated disposal costs.
The precision of automated systems means you'll see fewer errors, less rework, and minimal product damage during shipping.
The operational benefits extend beyond just cost savings. You'll benefit from faster order fulfillment, reduced storage space requirements, and improved customer satisfaction due to uniform packaging quality.
The systems also support sustainable practices by minimizing material waste and incorporating eco-friendly packaging options. While the initial investment may seem considerable, the long-term benefits of automation – including reduced labor costs, increased efficiency, and consistent quality – make it a strategic choice for businesses looking to stay competitive.
Establish Strong Supplier Partnerships
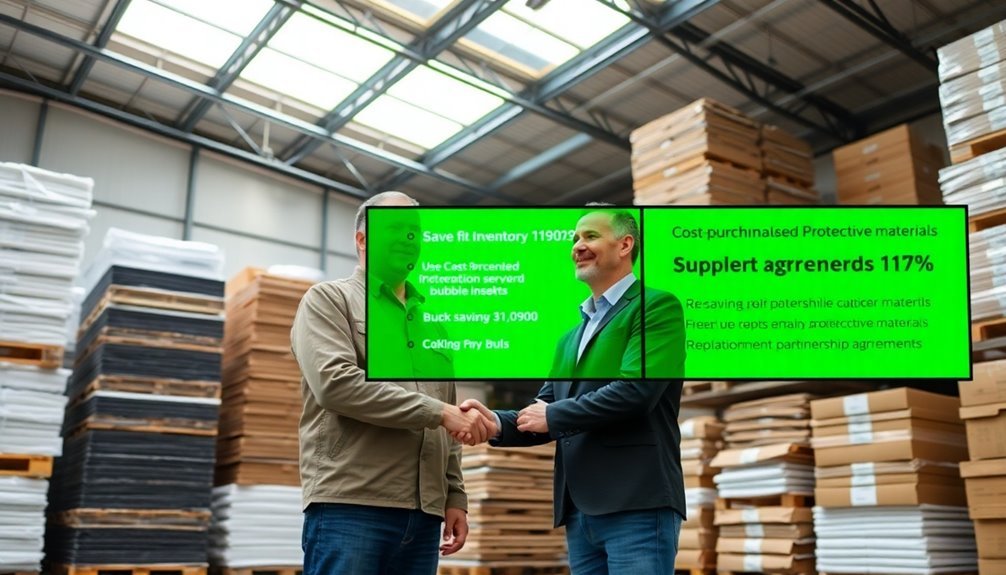
While automated systems enhance internal operations, strong supplier partnerships multiply your cost-saving potential. By consolidating your orders and working with fewer, more reliable suppliers, you'll gain better pricing through economies of scale. You'll also benefit from shared expertise in process optimization and joint innovation efforts. Your suppliers can help implement lean manufacturing principles to further streamline operations and minimize waste.
Work with your suppliers to implement a Plan for Every Part (PFEP) system, standardizing packaging dimensions and refining inbound materials. This collaboration helps reduce waste, optimize storage space, and lower logistics costs across your supply chain.
Partnership Benefits | Implementation Strategies |
---|---|
Volume Discounts | Bundle orders across facilities |
Quality Consistency | Select financially stable suppliers |
Innovation Opportunities | Collaborate on design improvements |
Resource Optimization | Share demand forecasts regularly |
Focus on building long-term relationships based on transparency and mutual benefit. You'll want to regularly review packaging data together and identify areas for continuous improvement. Consider implementing returnable packaging solutions and automated PFEP software to track initiatives. By maintaining open communication channels and working toward shared efficiency goals, you'll create sustainable cost savings that benefit both parties.
Standardize Packaging Dimensions
In accordance with global shipping standards, standardizing your packaging dimensions delivers substantial cost savings across your entire supply chain. When you adopt uniform packaging sizes, you'll benefit from bulk purchasing discounts and streamlined logistics operations. Uniform packaging leads to better pallet utilization, maximizing efficiency in warehouse operations. Studies show that global electronics manufacturers have achieved up to 25% reduction in packaging costs through standardization alone.
By implementing standardized dimensions, you'll optimize space utilization in storage and transit, leading to significant shipping cost reductions. You'll also simplify your inventory management processes, resulting in faster shipping times and fewer packing errors.
Companies like Dell have saved over $13 million annually by standardizing their packaging dimensions, while fitting 13% more laptops per pallet.
Imagine the satisfaction of seeing your warehouse operate with clockwork precision, thanks to uniform packaging that fits perfectly every time.
Picture the relief of your logistics team when they can process orders faster and more accurately.
Feel the confidence that comes from knowing you're maximizing every square inch of storage and shipping space.
Remember to balance standardization with practical considerations – while uniformity brings efficiency, certain products may still require custom sizing to minimize waste and guarantee adequate protection.
Implement Sustainable Packaging Solutions
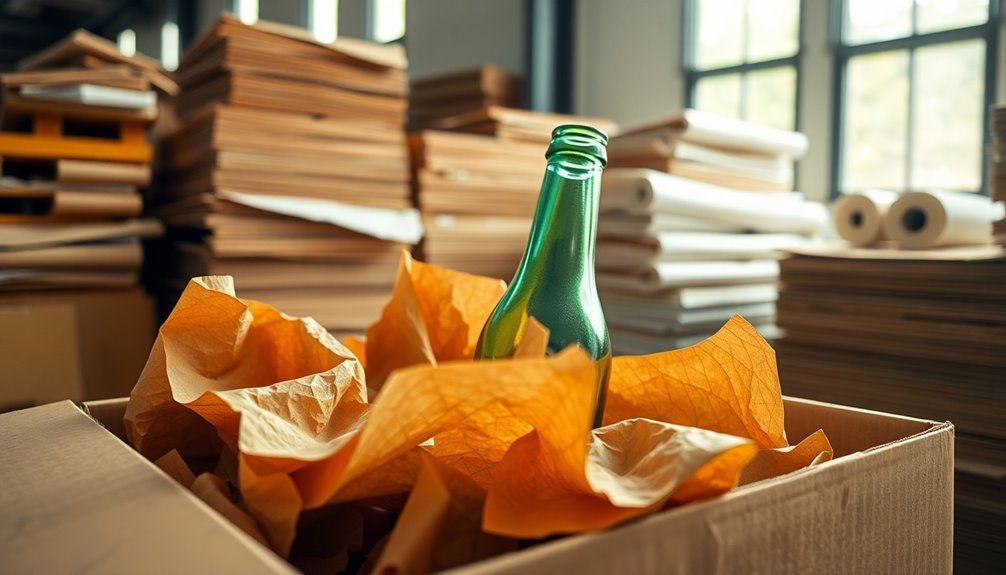
Sustainable packaging solutions offer a powerful way to reduce costs while minimizing environmental impact. You'll find significant savings by switching to flexible packaging materials that use less energy and fewer resources while maintaining a higher product-to-packaging ratio.
Consider implementing 100% recyclable materials and post-consumer recycled films to reduce your environmental footprint. Transport fewer trucks means reduced fuel consumption and lower shipping costs across your supply chain.
Explore innovative eco-friendly alternatives like compostable packaging made from renewable sources, mushroom-based solutions using agricultural waste, or seaweed packaging that utilizes agar. Hemp-based bioplastics and recycled paper pulp offer additional sustainable options that can lower your production costs while appealing to environmentally conscious consumers.
To maximize cost savings, focus on reducing package dimensions and consolidating shipments. You'll cut expenses by working with sustainable manufacturing partners and implementing reusable packaging systems.
Choose biodegradable materials that minimize both production costs and environmental impact. By incorporating eco-friendly cardboard and water-based inks, you'll create lightweight, recyclable solutions that reduce shipping expenses.
Remember to forecast demand accurately to prevent over-packaging and optimize your supply chain efficiency, ensuring you're using materials responsibly while maintaining your bottom line.
Frequently Asked Questions
How Long Does It Take to See Cost Savings From Packaging Optimization?
You'll typically see initial cost savings from packaging optimization within the first few months, but it often takes about 2.5 years to fully recoup your investment and realize substantial, compounding financial benefits.
What Are the Minimum Order Quantities for Bulk Packaging Discounts?
You'll find MOQs vary by supplier, but typically range from 100-1,000 units for basic packaging. Your bulk discounts usually start at these minimums, with deeper savings at higher quantities like 5,000+ units.
Which Packaging Materials Provide the Best Protection in Extreme Temperatures?
For high temperatures, you'll want Biosoluble Fibre Packings (up to 1,200°C) or E-Glass Fibre (up to 700°C). For cold conditions, you can rely on EPS or Polypropylene Foams for excellent insulation.
How Do Different Shipping Carriers' Requirements Affect Packaging Cost Decisions?
You'll need to balance each carrier's specific requirements with your budget. USPS allows lighter materials for small packages, while common carriers demand heavy-duty packaging, which can substantially impact your overall shipping costs.
What Insurance Considerations Should Be Made When Reducing Protective Packaging Materials?
When reducing packaging, you'll need to guarantee you're meeting insurance requirements, maintaining proper documentation, and balancing cost savings with risk. Non-compliance could lead to denied claims and higher premiums.
In Summary
You've got the tools to substantially reduce your protective packaging costs while maintaining product safety. By optimizing materials, automating processes, building supplier relationships, standardizing dimensions, and embracing sustainability, you'll see immediate savings and long-term benefits. Don't wait to implement these proven strategies – they're essential for staying competitive in today's market while keeping your products secure and your bottom line healthy.
Leave a Reply