You'll find ESD monitoring software delivers exceptional value through automated threat detection and preventive maintenance capabilities. By implementing real-time monitoring, you can reduce component damage, cut maintenance costs by 20-30%, and achieve ROI of up to 1,000% annually. The software streamlines compliance management, enhances employee productivity, and provides actionable insights through data-driven analytics. With features like automatic alerts, thorough activity logging, and IoT integration, you'll minimize downtime while maximizing operational efficiency. Discover how this powerful tool can transform your ESD control strategy and boost your bottom line.
Real-Time Threat Detection Benefits
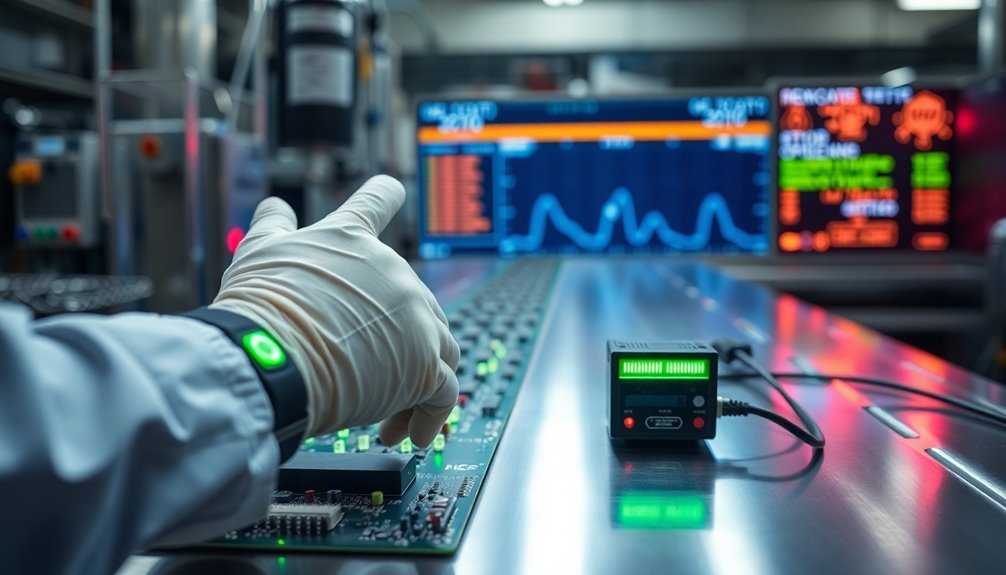
The speed of threat detection can make or break your organization's cybersecurity defenses. With real-time threat detection capabilities, you'll identify and respond to potential threats immediately, greatly reducing your risk exposure.
Your security teams will receive automatic alerts when suspicious activities occur, enabling them to take swift action before substantial damage occurs. File Integrity Monitoring helps track unauthorized system changes that could indicate a breach.
You'll benefit from thorough monitoring across your entire network, ensuring no malicious activity goes undetected. The advanced data analysis and comparison techniques help you spot both known threats and emerging attack patterns that might otherwise slip through traditional security measures. This proactive approach minimizes potential financial losses and protects your organization's reputation.
Your response times will improve dramatically as the system automates the detection process, reducing your mean time to detect (MTTD) and mean time to respond (MTTR).
You won't need to rely on manual checks, freeing your security team to focus on critical tasks that require human expertise. The continuous monitoring and behavioral analysis capabilities provide you with deep visibility into your network's security status, allowing you to identify and address vulnerabilities before they're exploited.
Cost Savings Through Automated Monitoring
Building on these robust detection capabilities, automated monitoring delivers considerable cost savings across your operations. By implementing IoT-enabled monitoring systems, you'll notably reduce manual workload while enhancing data accuracy and operational efficiency.
Your supervisors and operators can focus on critical tasks instead of routine data collection, leading to improved productivity and reduced human error. The integration of Cyber-Physical Systems enables seamless communication between physical devices and digital monitoring platforms.
The long-term financial benefits of automated ESD monitoring become evident through:
- Elimination of costly manual data collection and verification processes
- Prevention of expensive component damage and product recalls
- Reduction in maintenance and repair costs through proactive monitoring
- Decreased downtime due to fewer ESD-related incidents
- Lower labor costs from automated data analysis and reporting
You'll find that automated monitoring scales effectively with your growing manufacturing needs while maintaining cost efficiency. The continuous data collection provides real-time insights that help you make informed decisions quickly, preventing potential issues before they become expensive problems.
When you factor in the reduced workload for your team, minimized error rates, and enhanced operational control, the return on investment becomes clear. The combination of IoT technology and ESD monitoring creates a streamlined, cost-effective solution that protects both your products and bottom line.
Enhanced Product Reliability Metrics
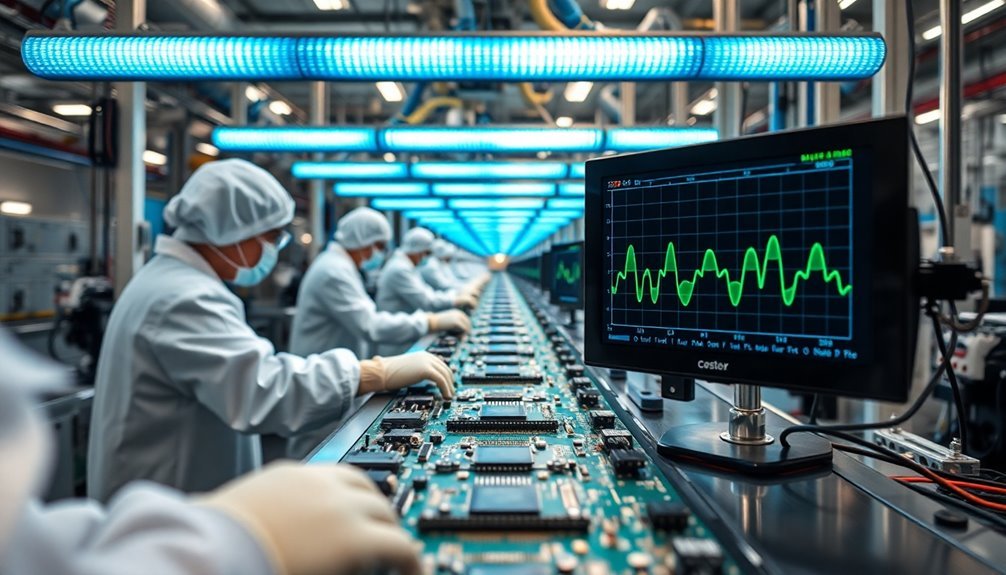
Through extensive reliability metrics, your ESD monitoring software provides essential insights into product performance and system health.
You'll gain access to vital measurements like MTTF, MTTR, and MTBF, which help you understand how long your systems operate without failure and how quickly they can be restored when issues arise. The ROCOF metric allows you to track unexpected events, while uptime percentage gives you a clear picture of overall system availability. A measurement of two failures per 100 hours helps teams accurately forecast maintenance needs.
These metrics enable you to identify vulnerabilities in your system before they become critical issues. You'll be able to track reliability growth over time and guarantee compliance with your service level agreements.
By integrating monitoring tools with your existing infrastructure, you're equipped to gather and analyze data effectively, leading to meaningful insights for system improvement.
The benefits are substantial: you'll predict failures before they occur, reduce repair times, and maintain higher customer satisfaction levels. Your operational efficiency will improve as you implement centralized reporting and follow an iterative improvement process.
With proper metric alignment to your business goals, you'll maximize the value of your ESD monitoring investment while assuring consistent service delivery.
Data-Driven Decision Making
Modern organizations thrive on data-driven decision making to eliminate guesswork from their operations. By integrating ESD monitoring software into your facility, you'll transform raw data into actionable insights that drive operational excellence and continuous improvement. Regular employee training programs ensure sustained success with your data-driven initiatives. This disciplined approach guarantees you're making decisions based on solid evidence rather than instinct.
Your ESD monitoring software investment enables advanced monitoring techniques that can analyze complex systems with multiple sensors and interactions. You'll benefit from real-time detection of anomalies and initial failures, while eliminating the need for time-consuming periodic testing and manual logging.
- Track KPIs aligned with your strategic goals
- Visualize data trends and patterns for quick anomaly detection
- Implement continuous monitoring for instant feedback
- Update data-driven models easily as new information becomes available
- Leverage clustering and data mining for thorough system analysis
With data-driven decision making, you're not just collecting information – you're transforming your industrial operations by making data an integral part of your strategic planning.
This approach optimizes maintenance, reduces costs, and guarantees your products are manufactured in a controlled environment that meets ESD protection standards.
IoT Integration Advantages
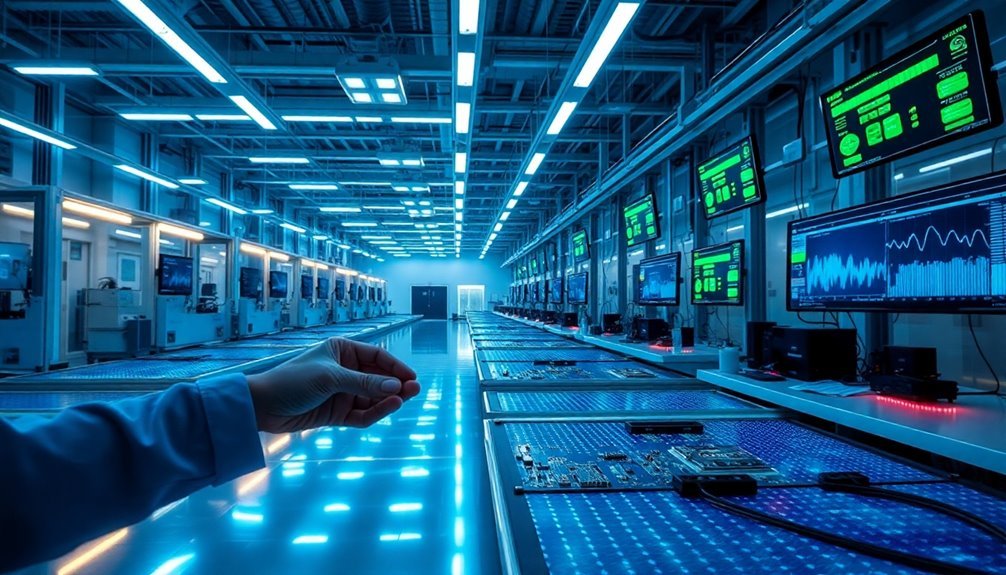
Integrating IoT sensors into your ESD monitoring system transforms raw data collection into a powerful, automated intelligence network.
You'll benefit from real-time threat detection, as sensors continuously monitor field voltage, EMI, temperature, and humidity changes. This proactive approach helps you prevent ESD events before they cause costly damage to your products.
With IoT integration, you'll eliminate the need for manual data entry and scheduled checks, allowing your operators and supervisors to focus on core tasks. The use of AI-driven analytics helps optimize operations by automatically adjusting machine settings for maximum efficiency.
The system works 24/7, providing immediate alerts when potential threats arise and enabling faster response times. You'll see enhanced quality in your manufacturing processes as automated data collection reduces human error and improves overall reliability.
Your investment in IoT-enabled ESD monitoring delivers measurable returns through reduced repair costs, decreased downtime, and optimized resource usage.
The system's scalability means it'll grow with your manufacturing needs, while seamlessly integrating with your existing ESD control infrastructure.
You'll gain extensive data visualization capabilities that support predictive maintenance and help you identify specific areas of concern, ensuring your ESD control program remains effective and efficient.
Streamlined Compliance Management
Building on the advantages of IoT integration, a streamlined compliance management system takes your ESD control program to the next level.
Personnel training records and certifications can be efficiently tracked to ensure all staff maintain current ESD safety knowledge.
You'll benefit from centralized data management that standardizes storage and automates reporting processes while maintaining a detailed audit trail of all compliance activities.
The system's all-encompassing approach enhances your compliance workflow through:
- Real-time monitoring and notifications that keep you informed of upcoming audits and deadlines
- Automated task management that reduces administrative burden and human error
- Customizable workflows that adapt to your specific ESD control requirements
- Advanced data analysis tools that identify trends and anomalies
- Integrated audit management with detailed checklists and corrective action tracking
You'll find that scheduled audits become more efficient with statistical sampling techniques and thorough verification procedures.
The software's ability to generate automated reports saves significant time while ensuring accuracy in compliance documentation.
When regulatory requirements change, you can quickly adapt your procedures and update documentation through the centralized platform.
This systematic approach not only streamlines your compliance processes but also provides concrete evidence of your commitment to ESD control standards.
Preventive Maintenance Capabilities
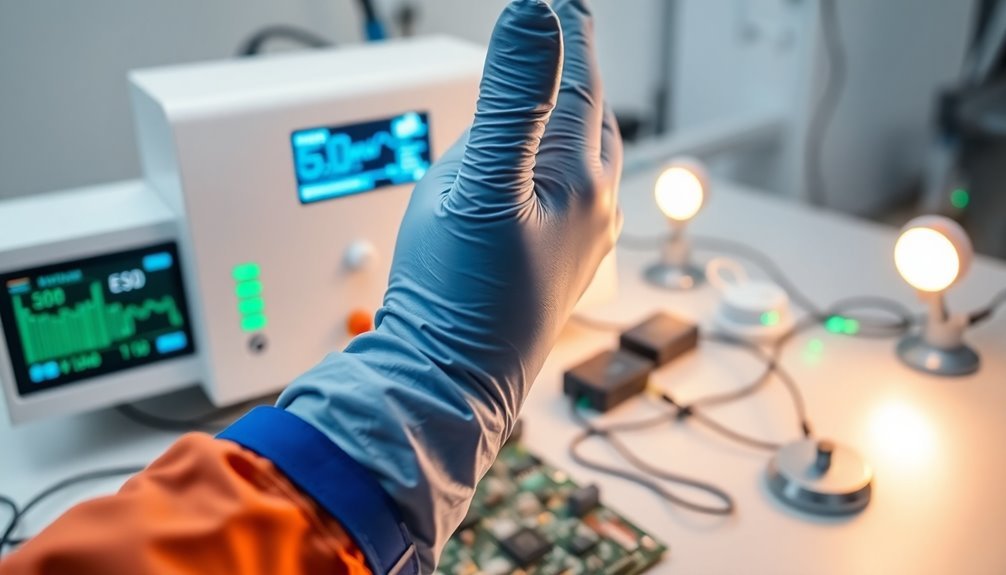
ESD monitoring software's advanced fault detection capabilities can alert you to potential issues before they escalate into critical failures.
You'll optimize maintenance schedules through data-driven insights that identify patterns and predict when equipment needs attention.
Your preventive maintenance program becomes more effective as the software continuously analyzes real-time data to spot early warning signs of ESD-related problems.
Companies implementing these solutions typically see maintenance cost reductions of 20-30% through proactive intervention and optimized scheduling.
Early Fault Detection Systems
Advanced systems for early fault detection stand at the forefront of modern ESD control, offering extensive monitoring and predictive maintenance capabilities.
You'll find these systems integrate seamlessly with your existing infrastructure, using noncontact fieldmeters and RF sensors to track static charge buildup and potential failures before they occur. Integrating these sensors with Internet of Things networks enhances overall operational efficiency and monitoring capabilities.
With real-time data collection and analysis, you can quickly identify and address ESD-related issues. The integration of continuous monitoring with predictive maintenance strategies guarantees you're always one step ahead of potential problems.
Your maintenance team can receive immediate alerts through CMMS systems when anomalies are detected, allowing for swift corrective actions.
- Noncontact fieldmeters continuously track E-field changes and static charge buildup
- RF sensors detect early signs of failing assets and potential ESD risks
- Real-time monitoring systems generate static charge heat maps for precise localization
- Computer vision technology enables accurate tracking of devices under test
- Advanced analytics help optimize your ESD management strategies
Maintenance Schedule Optimization
Optimizing maintenance schedules through preventive maintenance software delivers essential advantages for your ESD control system. The software automates your maintenance routines, ensuring you'll never miss critical equipment inspections or service intervals based on manufacturer guidelines.
You'll benefit from systematic tracking that keeps your ESD monitoring equipment in peak condition. You can establish precise scheduling for ionizer maintenance, fieldmeter calibration, and other ESD-critical equipment checks.
The software's data-driven approach helps you make informed decisions about when to perform maintenance tasks, preventing unexpected failures that could compromise your ESD protection.
You'll also gain valuable insights from thorough static charge heat maps, helping you identify areas that need more frequent attention.
Employee Productivity Improvements
Modern employee monitoring software delivers substantial productivity improvements by addressing multiple aspects of workplace performance. You'll gain real-time insights into employee activities, allowing immediate response to performance issues while identifying bottlenecks in your work processes. This data-driven approach allows you to make informed decisions about resource allocation and workflow optimization.
Your monitoring software will enhance workplace productivity through:
- Extensive activity logging that tracks application usage and time spent on tasks
- Performance benchmarks that help recognize high performers and identify training needs
- Real-time analytics that enable quick responses to productivity challenges
- Automated time tracking that provides visibility into how employees spend their time
- Enhanced security measures that protect sensitive data while monitoring access
With these capabilities, you'll create a more focused work environment where employees stay accountable and engaged with their core tasks.
The software's detailed insights help you set realistic, achievable goals based on actual performance data. You can identify struggling employees early, provide targeted support, and implement custom solutions to improve their efficiency.
This proactive approach to performance management facilitates continuous improvement while maintaining a balanced monitoring system that benefits both your business and employees.
Return on Investment Analysis
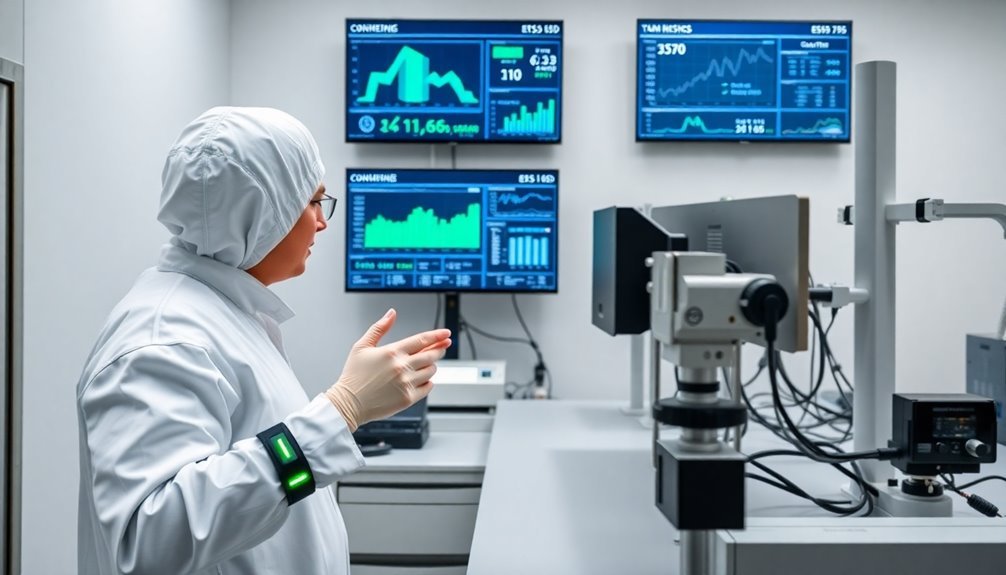
Your ESD monitoring software investment can yield substantial cost savings through reduced manual labor, fewer equipment failures, and increased operational efficiency.
You'll find the payback period for this technology remarkably quick, with some organizations reporting full cost recovery in as little as nine weeks.
Cost Savings Breakdown
Investment in ESD monitoring software delivers substantial returns through multiple cost-saving channels. You'll find that the automation of ESD monitoring processes creates both immediate and long-term financial benefits, with studies showing up to a 95:1 payback ratio on your investment.
The most significant cost savings come from several key areas:
- Labor cost reduction through automated data collection and verification, eliminating the need for manual checks
- Prevention of ESD-related damage, which directly reduces repair costs and scrap rates
- Increased productivity as your staff can focus on core responsibilities instead of ESD monitoring tasks
- Decreased downtime due to 24/7 automated monitoring and early issue detection
- Reduced support and maintenance costs through proactive problem prevention
These savings compound over time as your ESD monitoring software continues to optimize operations.
With potential annual ROI reaching up to 1,000%, you're not just buying a monitoring system – you're investing in operational excellence.
The software's ability to provide real-time feedback also enables continuous process improvement, leading to enhanced product reliability and customer satisfaction.
Payback Period Calculations
Building on these impressive cost savings, understanding the exact payback period for ESD monitoring software helps validate your investment decision.
You'll calculate this by dividing your total software investment costs by the annual savings you expect to achieve. For ESD control programs, you can typically expect a payback period of one year or less, with potential returns reaching up to 1000% depending on your industry and implementation effectiveness.
To determine your specific payback period, you'll need to account for several key factors.
Consider both direct savings from reduced ESD damage and indirect benefits like decreased downtime, improved productivity, and lower maintenance costs. You should also factor in any recurring costs such as software maintenance fees or updates.
For a more extensive assessment, you'll want to look beyond simple payback calculations.
Include a thorough ROI analysis that considers both tangible and intangible benefits. Regular audits of your ESD control program will help you track actual savings against projected figures, allowing you to adjust your calculations and optimize your investment.
Remember that accuracy in your initial estimates is essential for reliable payback period calculations.
Frequently Asked Questions
How Long Does It Typically Take to Train Staff on ESD Monitoring Software?
You'll need between 2 to 8 hours for basic ESD monitoring software training. For more thorough understanding, you can expect up to four days of training spread across four weeks.
Can ESD Monitoring Software Integrate With Existing Quality Management Systems?
Yes, you'll find that ESD monitoring software readily integrates with your quality management systems through API connectivity, ensuring compliance with standards like ANSI/ESD S20.20 while maintaining seamless data exchange between platforms.
What Backup Systems Are in Place if the Monitoring Software Fails?
You'll have multiple safeguards: cloud backup systems, real-time data streaming, hardware redundancy, and automatic software restart features. If needed, you can also implement manual ESD control measures while the system recovers.
How Often Should the ESD Monitoring Software Be Updated or Upgraded?
You'll need to update your ESD monitoring software quarterly for routine checks and annually for compliance. Consider immediate upgrades when there's new technology, regulatory changes, or manufacturing process modifications that affect monitoring requirements.
Are There Different Software Versions for Different Industry-Specific Compliance Requirements?
Yes, you'll find specialized ESD monitoring software versions tailored to meet different industry standards, including semiconductor manufacturing (JEDEC), military (MIL-STD), and general electronics manufacturing (ANSI/ESD S20.20 and IEC 61340-5-1) requirements.
In Summary
You'll find ESD monitoring software delivers clear value through its extensive protection of your manufacturing assets and processes. By combining real-time threat detection, automated monitoring, and data analytics, you're not just preventing costly damage – you're optimizing operations and ensuring compliance. When weighing the investment against potential losses from ESD events, the software's preventive capabilities and efficiency gains make it a smart business decision.
Leave a Reply