You'll need to follow three essential ionizer standards for certified cleanrooms: First, guarantee compliance with ISO 14644-1 and GMP guidelines for your facility's cleanliness classification, maintaining proper air changes per hour based on your ISO level. Second, implement regular performance monitoring using a Charged Plate Monitor (CPM) to evaluate discharge times from 1000V to 100V, following ESD TR53 protocols. Third, establish strict maintenance schedules that include cleaning, recalibration, and emitter point replacement to prevent system failures. Understanding these foundational standards will help you create a more efficient and compliant cleanroom operation.
Cleanroom Classification Requirements
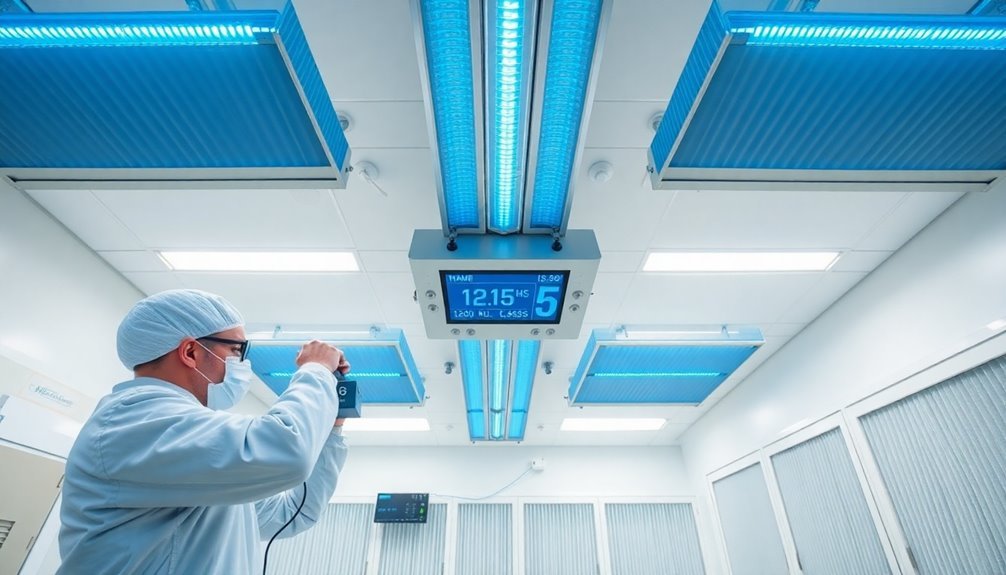
Within the highly regulated world of cleanroom operations, understanding classification requirements is critical for maintaining controlled environments.
You'll need to follow both ISO 14644-1 standards and GMP guidelines, which establish specific cleanliness levels from ISO 1 (cleanest) to ISO 9 (least clean). Proper ventilation is essential, requiring air changes per hour ranging from 240-360 for ISO 5 to 10-25 for ISO 8 environments.
For pharmaceutical and medical applications, you'll encounter four GMP grades that correspond to ISO classifications. Grade A areas, equivalent to ISO 5, require the strictest controls with no more than 3,520 particles ≥0.5µm per cubic meter. Regular environmental monitoring includes assessing temperature and humidity levels to prevent microbial growth.
If you're working in Grade B or C environments (ISO 7), you'll need to maintain particle counts below 352,000 per cubic meter. Grade D spaces (ISO 8) allow up to 3,520,000 particles.
You'll need to verify your cleanroom's compliance through a rigorous qualification process. This includes design qualification to confirm your plans meet regulations, installation qualification to guarantee proper setup, and operational qualification to validate performance.
Whether you're using a pharma-wall, modular, or soft-wall design, you must establish appropriate monitoring systems to maintain these classification requirements and document your compliance with industry-specific standards.
Performance Monitoring And Testing
Maintaining cleanroom classification standards requires rigorous performance monitoring of all equipment, including ionizers. You'll need to follow ESD TR53 compliance guidelines, which mandate testing using ANSI/ESD STM3.1 and SP3.3 standards for discharge time and offset voltage measurements.
To properly evaluate ionizer performance, you must use a Charged Plate Monitor (CPM) with a 15 cm x 15 cm isolated conductive plate that has a total capacitance of 20 ± 2 picofarads. Testing should include plate voltage discharge from 1000V to 100V for accurate measurements. Sensors play a vital role in ensuring continuous operation despite potential emitter point contamination.
You'll need to contemplate different test locations and measurement distances based on your specific ionizer type, whether you're using air-assist bars, soft X-ray ionizers, or non-airflow alpha ionizers.
Your maintenance schedule should align with your cleanroom's critical requirements. While EIA-625 suggests checking ionizers every six months, you may need more frequent inspections depending on your program's needs.
You'll want to implement regular cleaning, recalibration, and emitter point replacement. Contemplate installing real-time monitoring systems to track performance and reduce scrap rates.
When selecting ionizers, you must evaluate your application requirements, including area coverage and ion density, while accounting for ambient air conditions and contamination risks.
Safety And Compliance Protocols
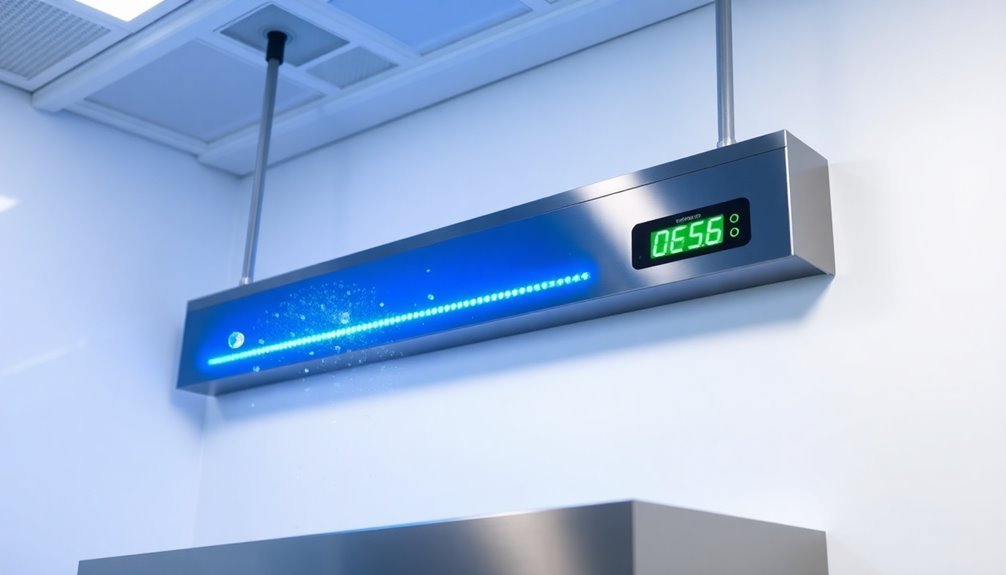
Proper safety and compliance protocols lay the groundwork for successful ionizer operation in cleanroom environments.
You'll need to implement strict installation guidelines, starting with proper wiring separation between power and high-voltage lines to prevent interference. Before operation, verify all wiring connections and flush piping systems to eliminate contaminants that could compromise your system's integrity. HEPA filtration systems are essential for maintaining cleanroom air quality to ISO standards.
You must maintain specific environmental conditions, keeping temperatures between 0-50°C and relative humidity within 35-80%. Regular ionizer maintenance ensures optimal performance and prevents system failures that could compromise cleanroom standards.
Don't install ionizers in enclosed spaces, as they generate ozone and nitrogen oxides that require proper ventilation. Monitor your facility for exposure to corrosive gases and explosive vapors, implementing necessary safeguards to maintain a controlled environment.
Your personnel safety program should include thorough training, mandatory protective equipment usage, and clear protocols for chemical handling and waste disposal.
To meet cleanroom standards, you'll need to follow ISO classifications strictly, utilizing ULPA filters for ISO 1-5 environments.
Regularly test particle counts, airflow patterns, and air-pressure differentials to guarantee ongoing compliance. Remember to document all safety incidents and equipment malfunctions promptly, maintaining detailed records for regulatory compliance and quality assurance purposes.
Frequently Asked Questions
How Does Humidity Affect Ionizer Performance and Calibration Requirements?
You'll notice that high humidity reduces your ionizer's efficiency by neutralizing ions and causing unwanted recombination. You must calibrate regularly and use external sensors to maintain proper ion balance in varying humidity conditions.
Can Different Types of Ionizers Be Used Simultaneously in One Cleanroom?
Yes, you can use different ionizers simultaneously in your cleanroom. You'll benefit from combining overhead, benchtop, and handheld ionizers to achieve thorough static control and address various application needs throughout your workspace.
What Causes Uneven Ion Distribution Despite Proper Ionizer Placement?
You'll face uneven ion distribution when your emitters are degraded, airflow is turbulent, or obstacles block ion flow. Environmental factors like high humidity and temperature changes can also disrupt ion balance in your space.
How Often Should Ionizer Emitter Points Be Cleaned or Replaced?
You'll need to clean your ionizer points monthly in clean environments and daily in dirty settings. Replace them when they're damaged or show significant buildup that cleaning can't fix. Check manufacturer guidelines.
Do Emergency Power Systems Affect Ionizer Performance During Backup Power Operation?
Your ionizer's performance can remain stable during backup power if you have proper voltage regulation and surge protection in place. You'll need quality power conditioning to maintain consistent ion balance and operation.
In Summary
You'll need to maintain rigorous standards for your cleanroom ionizers through proper classification protocols, regular performance monitoring, and strict safety compliance. Don't overlook the importance of staying up-to-date with industry certifications and testing requirements. By following these three vital standards, you'll guarantee your cleanroom maintains ideal ionization levels and meets all necessary regulatory specifications for your specific application.
Leave a Reply