Seven essential tools help you maintain effective static control in your facility. You'll need surface resistivity meters to measure material conductivity, wrist strap testers to verify proper grounding of personnel, and footwear testing systems to guarantee safe foot grounding. Environmental static field meters monitor ambient charges, while charge plate analyzers evaluate ionization effectiveness. Continuous monitoring systems provide real-time alerts for grounding failures, and digital ESD data loggers automatically document your test results for compliance. Understanding these critical tools and their proper application will strengthen your ESD protection program's foundation.
Surface Resistivity Measurement Devices
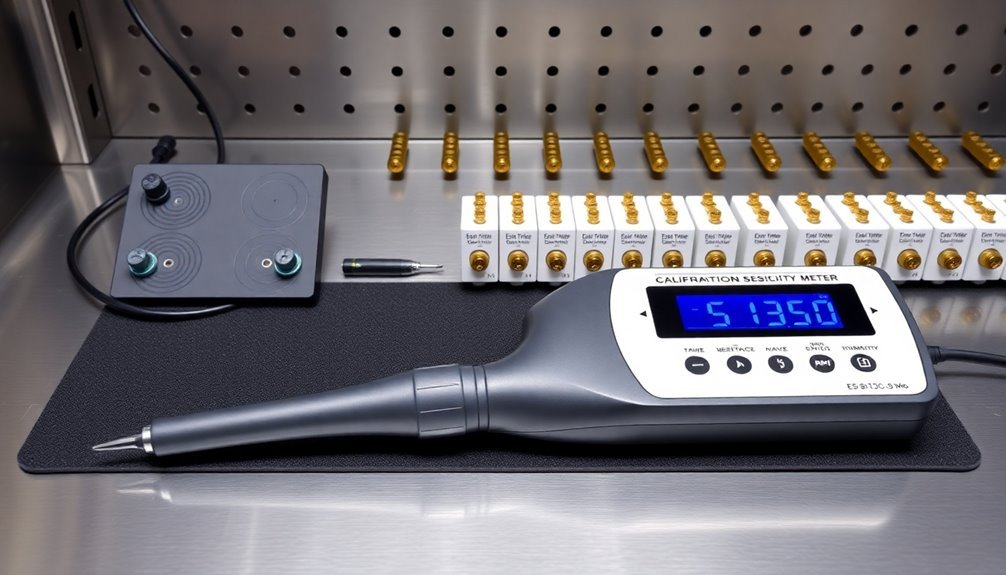
The measurement of surface resistivity requires specialized devices that follow standardized testing methods like ASTM D257. You'll need to use electrodes rather than point probes to get consistent readings, as this accounts for the varied composition of compounded thermoplastics.
When you're measuring, the device will multiply the resistance by a geometry coefficient to calculate the surface resistivity in ohms per square. These instruments can accurately measure a wide range 10³-10¹² ohms per square of resistance.
You'll find several types of measurement devices available for your static control testing needs. Handheld units like the 740 Surface Resistance Meter offer quick, repeatable measurements for conductive, static dissipative, and insulative surfaces.
If you're looking for more detailed testing capabilities, you'll want to evaluate complete meter kits that can perform both resistance point-to-point and resistance to ground measurements.
Most modern surface resistivity meters come with convenient features you'll appreciate, including automatic ranging and illuminated LEDs that display the decade in ohms per square. They're typically battery-operated for portability and designed to function reliably within specific environmental conditions (5-50°C and 0-90% rH).
You'll find these devices essential for ESD prevention programs and manufacturing environments where static control is vital.
Wrist Strap Testing Equipment
You'll need to test your wrist straps daily using a reliable tester that measures system resistance and provides clear pass/fail indicators to meet compliance standards.
For continuous protection, you can implement constant monitoring systems that instantly alert you to any grounding disconnections or failures during your work. Dirty wrist strap cuffs can cause serious grounding failures and must be regularly cleaned.
Your compliance verification process should include proper documentation of all test results and immediate replacement of any wrist straps that don't meet the required resistance specifications of less than 35 megohms.
Daily Testing Best Practices
Regular wrist strap testing forms a critical foundation of any effective ESD control program. You'll need to test your wrist straps and ESD footwear at least once daily before handling any sensitive devices, confirming you're maintaining proper grounding protection throughout your workday.
- Always log your test results for quality control documentation, which supports ANSI ESD S20.20 compliance requirements.
- Use testers with both visual LED indicators and audible alarms to quickly identify pass/fail status.
- Select testing equipment that matches your facility's needs, whether it's wall-mounted, portable, or combination units.
When you're conducting your daily tests, you'll want to connect your wrist strap to the tester using the standard banana plug connection. Some testers can also evaluate ESD protective clothing like smocks and lab coats.
Many advanced testers now offer digital readouts displaying resistance values in Ohms, which can help you track trending data.
If you're using a combo tester, you can check both your wrist strap and foot grounders simultaneously.
Remember that your testing equipment requires periodic verification – most units need annual calibration to maintain accuracy.
For the most reliable results, consider using NIST-certified calibration services to confirm your testing equipment remains precise and dependable.
Continuous Monitoring Solutions
Modern continuous monitoring solutions represent a significant advancement over traditional periodic testing methods. These systems provide instant feedback on wrist strap and worksurface failures, catching even split-second issues that you'd miss with routine testing.
You'll find both single wire (impedance) and dual wire (resistance) configurations available from leading brands like SCS, Desco, and Transforming Technologies. Similar to continuous controls monitoring, these systems automate the validation of safety measures in real-time.
You won't need to perform daily testing and logging when you've installed a continuous monitoring system, which saves valuable time and reduces operational costs. The systems operate with a static resistance range of 750 kilohms to 35 meg ohms, meeting EN IEC 61340 specifications.
They'll alert you to failures through visual and audible signals, ensuring immediate awareness of any protection issues.
You can choose from various monitoring solutions to match your needs. Whether you need a portable tester, a complete wall-mounted station, or a custom solution, you'll find options that support your specific requirements.
If you're looking to maintain compliance while improving efficiency, these systems deliver both benefits. They'll help you maintain consistent static control while eliminating the time and resources previously spent on periodic testing.
Compliance Verification Methods
Proper wrist strap testing equipment forms the backbone of any ESD compliance verification program. You'll find several types of testers available, each designed to meet specific testing requirements and compliance standards set by ANSI/ESD S20.20. Regular testing is critical since wrist straps are susceptible to wear and tear failure over time.
- Handheld testers offer portability and quick testing capabilities
- Wall-mounted stations create designated testing areas for consistent verification
- Dual test stations enable simultaneous testing of both wrist straps and footwear
When you're implementing a compliance verification program, you'll need to guarantee your testers meet the resistance limits specified in ANSI/ESD S1.1, keeping measurements below 3.5 x 10^7 ohms.
Your testing equipment should include clear LED indicators for pass/fail results and operate within the standard resistance range of 0.75 to 35 meg-ohms.
You must conduct daily testing to maintain compliance, following a straightforward procedure: secure the wrist strap, connect the grounding cord to the tester, and press the test button.
Don't forget about annual calibration – it's essential for maintaining NIST traceability and guaranteeing accurate measurements.
Footwear Grounding Verification Systems
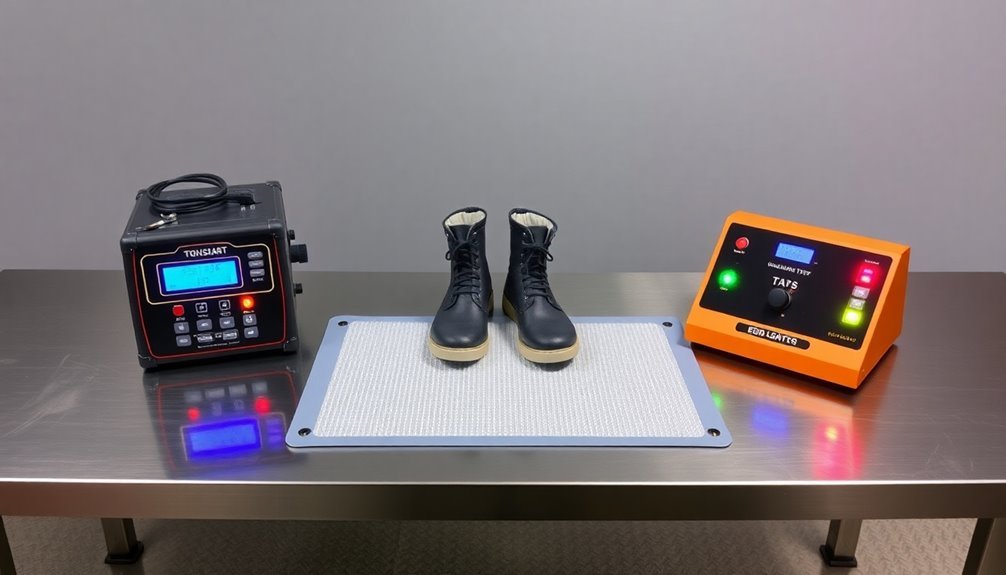
You'll need to test your ESD footwear daily using proper verification systems to maintain safety standards and prevent static discharge risks.
Your resistance measurement checks should focus on both shoes independently, ensuring each meets the required electrical resistance specifications when tested against a ground plate.
Static sparks from improperly protected footwear can create ignition hazards in flammable atmospheres. When verifying your personnel equipment, you must follow standardized procedures and document test results to confirm your footwear continues to provide adequate static dissipation properties.
Daily Testing Best Practices
Establishing a robust daily testing routine for ESD footwear stands as a critical component of any effective static control program. You'll need to conduct these tests before entering any ESD Protected Area (EPA) to guarantee proper grounding protection throughout your workday. The 750 kiloohms to 35 megohms range indicates proper grounding performance during testing.
- Configure your ESD footwear tester to match your facility's resistance requirements, typically between 1 x 10^6 to 1 x 10^8 ohms.
- Test each foot independently using a split footplate system while wearing your ESD footwear.
- Document all test results, including any failures or near-fail alerts, for quality control tracking.
When using your footwear tester, guarantee it's properly grounded to a reliable point and verify both heel and toe grounders are worn on each foot.
If you receive a FAIL result, immediately stop work and investigate the source by testing the foot grounder and contact strip separately.
You'll want to pay attention to near-fail alerts, as they'll help you identify worn devices before they cause problems.
Remember to use testing equipment with digital readouts for precise measurements and consider testers with automatic data collection capabilities to streamline your documentation process.
Resistance Measurement Techniques
In accordance with industry standards, footwear grounding verification requires thorough testing of each component in your ESD protection system. You'll need to test your footwear daily while wearing it, ensuring proper functionality of both the foot grounder and contact strip, as well as the interface between the strip and your skin's perspiration layer. Static decay measurements should confirm that footwear can dissipate charges effectively when grounded.
To conduct these tests effectively, you'll want to use specialized equipment like the GTS900K Premium Combination Testing Station, which can test both feet simultaneously and independently. This three-state touch tester complies with ANSI ESD S20.20 requirements and doesn't require annual calibration, though you should use verification tools like the CAL1000 unit periodically.
For more extensive testing, you'll need to perform resistance measurements using both surface and volume resistance methods. When measuring work surfaces, follow ANSI/ESD S4.1 guidelines by conducting resistance top-to-top (RTT) and resistance-to-groundable point (RTG) tests.
You can use the AEMC Instruments Ground Resistance Tester Model 6424 for simplified fall-of-potential tests, which is particularly suitable for smaller systems. Remember to maintain proper environmental conditions during testing, as compliance tests require measurements at different relative humidity levels.
Personnel Equipment Verification
A thorough footwear grounding verification system forms the backbone of personnel ESD protection in sensitive manufacturing environments. You'll need both wrist strap testers and dedicated footwear testers to guarantee complete protection, with many modern systems combining both functions into a single unit.
Daily testing protocols require you to verify your footwear while wearing it, making contact with the body contact area, and logging results for quality control.
Your testing station should be positioned at ESD Protected Area entrances, often integrated with access control systems.
You'll want continuous monitoring capabilities for high-value production areas, with regular calibration checks every six months.
When implementing your verification system, you'll need to choose between continuous footplates or split footplates for testing both feet. Remember that your equipment must comply with ANSI/ESD S20.20 and IEC 61340-5-1 standards.
Don't forget to maintain detailed records of all tests – they're essential for your quality control program. If you detect any failures during testing, replace the faulty footwear immediately to maintain your ESD protection integrity.
Environmental Static Field Meters
Environmental Static Field Meters stand out as essential tools for measuring electrostatic charge without making direct contact with objects. These devices measure the force between induced charges in their sensors and convert it to voltage readings, providing you with accurate measurements regardless of probe-to-surface distance variations.
You'll find these meters particularly valuable in ESD-sensitive environments where static control is important. The meters feature chopper-stabilized sensors and a ranging mechanism that guarantees accurate readings at different distances.
They're equipped with digital displays for easy reading and include advanced features like data logging and alarm systems for high static levels.
When you're using an Environmental Static Field Meter, you'll need to place the probe within 1-5mm of the surface you're measuring. The meter's electronic circuitry drives the probe body to match the measured surface's potential, preventing arc-over during high voltage measurements.
The device's conductive case serves as the ground reference for its measuring circuit.
These meters play a key role in your ESD control procedures, helping you identify sensitive areas, verify grounding effectiveness, and maintain compliance with ESD safety standards. They're designed for both laboratory and on-site use, making them versatile tools for your static control needs.
Charge Plate Analysis Tools
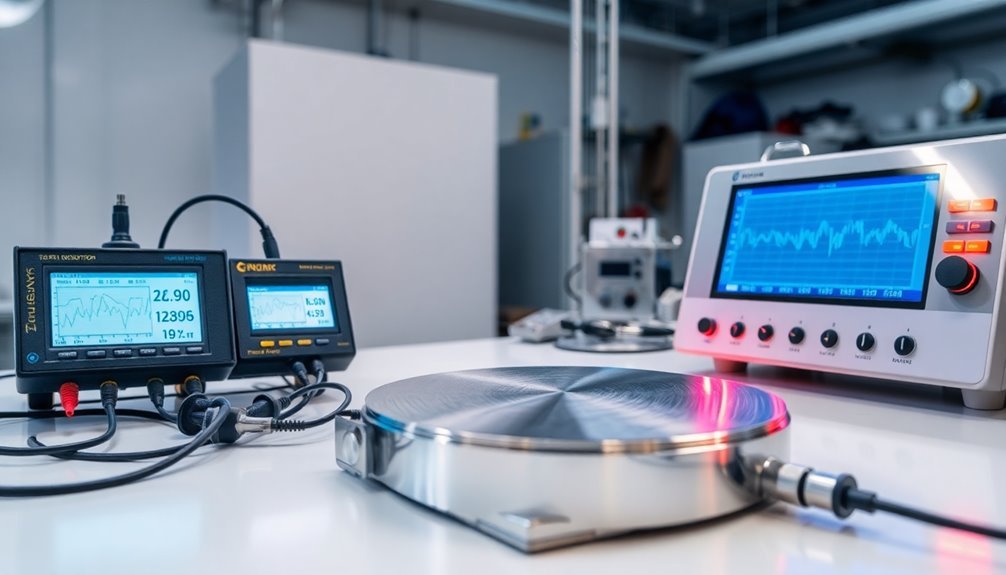
Charge plate analysis tools serve as sophisticated instruments for evaluating ionizer performance and measuring static decay characteristics. They've become essential in ESD control programs, offering high-precision voltage measurements and extensive testing capabilities for static-sensitive environments.
- You'll find these analyzers equipped with dual polarity power supplies up to 1200 Volts, allowing you to conduct thorough ionizer balance tests within the ANSI/ESD S20.20-2014 standard's ±35 Volt range.
- Modern units feature precision timing systems that can measure decay times up to 60 seconds in 0.3-second increments, or 6 seconds in 0.03-second increments for specialized applications.
- You can rely on high-resolution LCD displays that show voltage readings with 1-volt resolution and clear polarity indicators.
When you're working with charge plate analyzers, you'll appreciate their portable design and user-friendly features like rotating sensor heads and interchangeable detector plates.
These tools provide essential data through buffered outputs and high-impedance monitoring systems, helping you maintain compliance with standards like ESD STM3.1 and SAE J1645.
You can easily define maximum discharge times and receive immediate feedback when testing ionizer performance or evaluating static dissipation materials.
Continuous Monitoring Systems
Inside modern ESD-protected environments, continuous monitoring systems serve as vigilant guardians of your personnel and equipment grounding. These systems provide instant feedback on wrist strap functionality and continuously monitor your operators' connection to ground, detecting even split-second failures before they become serious issues.
You'll find several types of monitoring systems to choose from. Capacitance and impedance monitors use single-wire technology to detect ground connections, while resistance monitors employ dual-wire systems to track the complete resistance loop. Dual-wire systems offer enhanced reliability by maintaining ground connection even if one conductor fails.
Your continuous monitoring system works by constantly checking the ground path and displaying status through LED indicators. It'll monitor both wrist straps and worksurface connections, automatically calibrating to maintain compliance with standards.
You won't need to perform periodic testing anymore, which saves time and labor costs.
Digital ESD Data Loggers
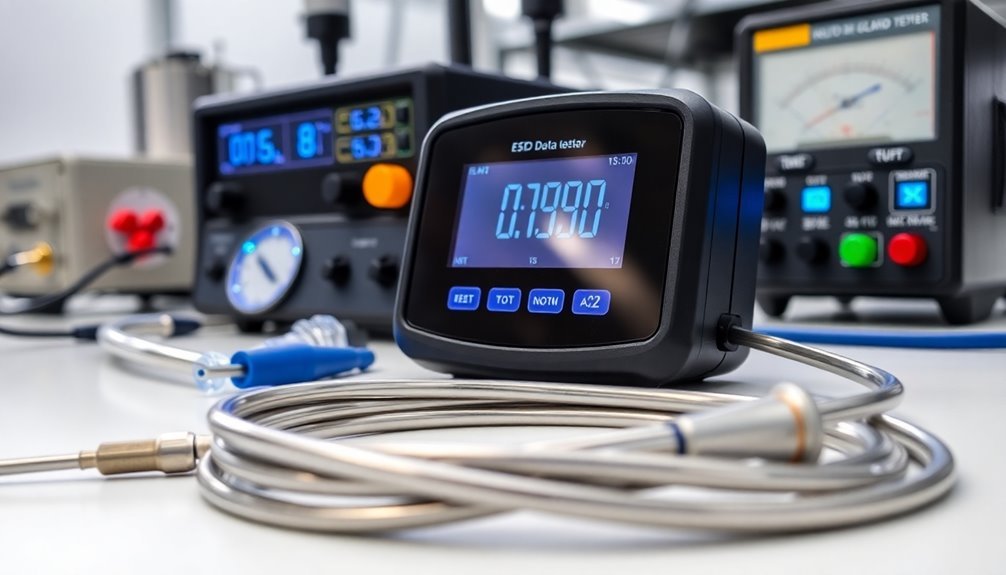
Digital ESD data loggers take your static control program to the next level by automatically documenting test results for ESD wrist straps, footwear, and heel grounders. These essential tools guarantee you're meeting ANSI/ESD S20.20 requirements while eliminating manual record-keeping errors and streamlining your compliance process.
- Real-time logging with RFID or touchscreen keypads for immediate operator identification
- Integration with automatic door systems to control access based on test results
- Extensive data storage of resistance measurements, time stamps, temperature, and humidity readings
You'll find various models available, including the EMIT Smartlog Pro 2 and Warmbier 7100.PGT120.COM, each offering USB connectivity for easy data transfer.
These systems don't just log data – they're your gateway to automated testing and enhanced security in ESD protected areas.
When you're preparing for audits, you'll appreciate how these loggers generate detailed reports with complete audit trails. They'll help you maintain reliable records while improving your facility's efficiency.
Frequently Asked Questions
How Often Should ESD Testing Equipment Be Recalibrated?
You should recalibrate your ESD testing equipment every six months to two years, depending on your manufacturer's guidelines, usage frequency, and environment. Always follow accredited calibration services for reliable results.
Can ESD Meters Be Used in Humid Environments?
Yes, you can use ESD meters in humid environments. While high humidity reduces static buildup, it doesn't eliminate ESD risks. Your meter will still function effectively, though you'll typically see lower readings above 60% humidity.
What Happens if ESD Equipment Fails During Production?
You'll face immediate production stops, potential equipment damage, and financial losses. Your products may suffer latent defects, and you'll need to halt operations while investigating and implementing emergency ESD protection measures.
Are Wireless ESD Monitoring Systems as Reliable as Wired Ones?
No, your wireless ESD monitoring systems aren't as reliable as wired ones. You'll face potential interference issues, slower data transmission, and battery life concerns, while wired systems provide more stable, continuous monitoring capabilities.
How Long Do ESD Testing Equipment Batteries Typically Last?
You'll typically get 1-2 days of continuous use from a single charge, but your ESD testing equipment's battery life varies based on usage patterns, battery type, and environmental conditions like temperature.
In Summary
You'll need all seven of these critical static control testing tools to maintain a thorough ESD protection program. Whether you're measuring surface resistivity, verifying personal grounding, or monitoring environmental conditions, these instruments work together to help you prevent costly damage to sensitive electronics. Don't overlook the importance of regular testing and documentation – it's essential for maintaining ESD control standards.
Leave a Reply