To prevent static electricity in your clean room, you'll want to maintain humidity levels between 40-60%. This ideal range effectively reduces static buildup while avoiding issues like microbial growth or equipment damage. You can achieve these levels using HVAC systems with humidity controls, along with tools like steam humidifiers or desiccant systems. It's vital to monitor levels consistently, as even brief drops below 40% humidity can generate enough static to damage sensitive electronic components. Static prevention becomes especially challenging during seasonal changes, but proper humidity management techniques can help you maintain ideal conditions year-round.
Understanding Static in Clean Rooms
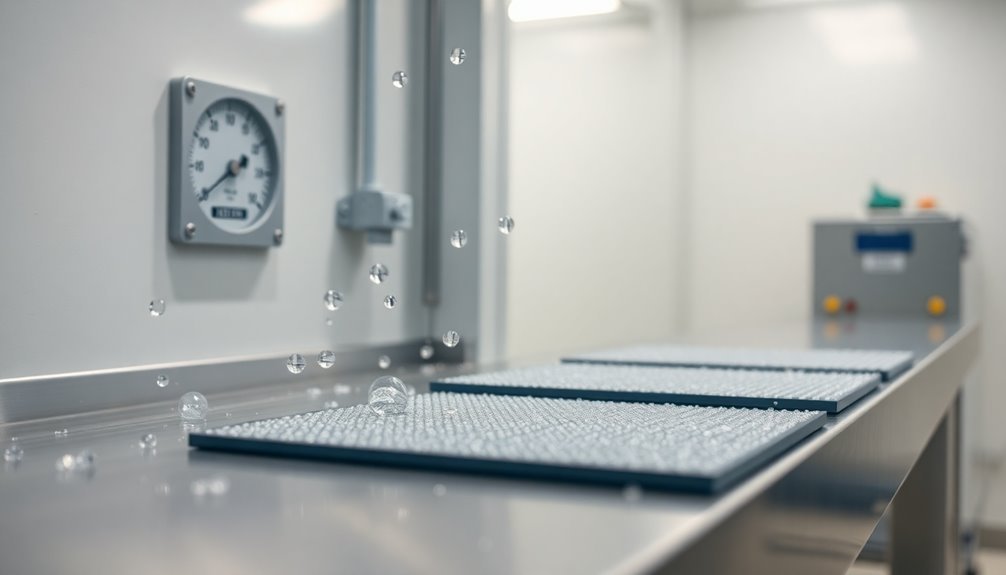
Working in clean rooms requires a thorough understanding of static electricity and its potential impacts. When you operate in these environments, you'll encounter static build-up from multiple sources, including human movement, HEPA filtration, and the interaction between different surfaces.
Environmental factors like light, heat, and cooling can also contribute to static charge generation. Maintaining proper humidity is essential for reducing electrostatic discharge potential.
You'll need to be particularly vigilant about static's effects on your operations. Even low voltages of 30+ can damage sensitive electronic components through electrostatic discharge (ESD). Static charges also attract and hold airborne particles, making it harder to maintain cleanliness standards and potentially compromising your production quality.
To control static effectively, you'll want to implement several preventive measures. Start by using anti-static materials in your clothing, curtains, and tools.
Install conductive materials like specialized shoe covers and tape to safely channel electrostatic charges. You should also incorporate dissipative materials in your floors and walls, while using ionizers in your air circulation system.
Remember to follow a sequential approach: establish proper grounding first, then replace insulating materials with dissipative ones, and finally implement ionization technology where needed.
Optimal Humidity Range
Maintaining a humidity level between 40-60% is essential for cleanroom operations, particularly in aerospace and similar sensitive industries.
Your control measures must include proper HVAC systems with humidity monitoring sensors and technologies like steam injection or desiccant solutions to maintain this ideal range.
Without these essential controls in place, you risk static buildup, product damage, and potential health concerns for your employees. Employee discomfort can increase particle release and contaminate the cleanroom environment.
Maintaining 40-60% Balance
Three vital factors make the 40-60% relative humidity range essential for cleanroom operations. First, this range prevents static electricity buildup that can damage sensitive equipment and products.
Second, it minimizes the risk of microbial growth and contamination that occurs in higher humidity environments. Temperature fluctuations in HVAC systems can quickly disrupt these optimal conditions.
Third, it maintains optimal working conditions for both personnel and equipment, ensuring consistent product quality.
You'll need to implement proper monitoring and control systems to maintain this delicate balance. Using hygrometers and automated control systems, you can track and adjust humidity levels in real-time. When you're operating outside this range, you risk compromising your cleanroom's effectiveness.
Here's what you can expect when maintaining proper humidity levels:
- Reduced risk of static electricity damage to sensitive electronics
- Prevention of condensation that could lead to microbial growth
- Enhanced stability and quality of manufactured products
- Improved comfort for cleanroom personnel
- Decreased likelihood of biological contamination
Industry-specific requirements may vary slightly, but the 40-60% range serves as a universal standard across pharmaceuticals, medical devices, and electronics manufacturing. You'll find that automated systems with both humidification and dehumidification capabilities offer the most reliable method for maintaining this vital balance.
Essential Control Measures
While maintaining cleanroom humidity levels requires precision, understanding the essential control measures makes the task manageable. You'll need to maintain relative humidity between 30-40% year-round to prevent both bacterial growth and static electricity issues. This range is vital, though specific requirements may vary by industry. Regular humidity level testing helps ensure compliance with environmental standards.
You'll find that temperature and humidity work hand in hand. When you lower the temperature, relative humidity decreases, while higher temperatures cause it to rise. To maintain ideal levels, you'll need to monitor and adjust for external environmental conditions, particularly during seasonal changes.
High air exchange rates can pose challenges, especially in winter months.
Your HVAC system serves as the primary control method, using sensors for real-time adjustments. You can employ various tools like resistive steam humidifiers for precise control or ultrasonic humidifiers for energy-efficient operations.
When you need to achieve lower humidity levels, desiccant systems effectively capture moisture. By implementing these control measures, you'll guarantee consistent humidity levels that prevent experimental delays, maintain employee comfort, and meet strict cleanroom standards while reducing static electricity problems.
Risk Factors for Static Buildup
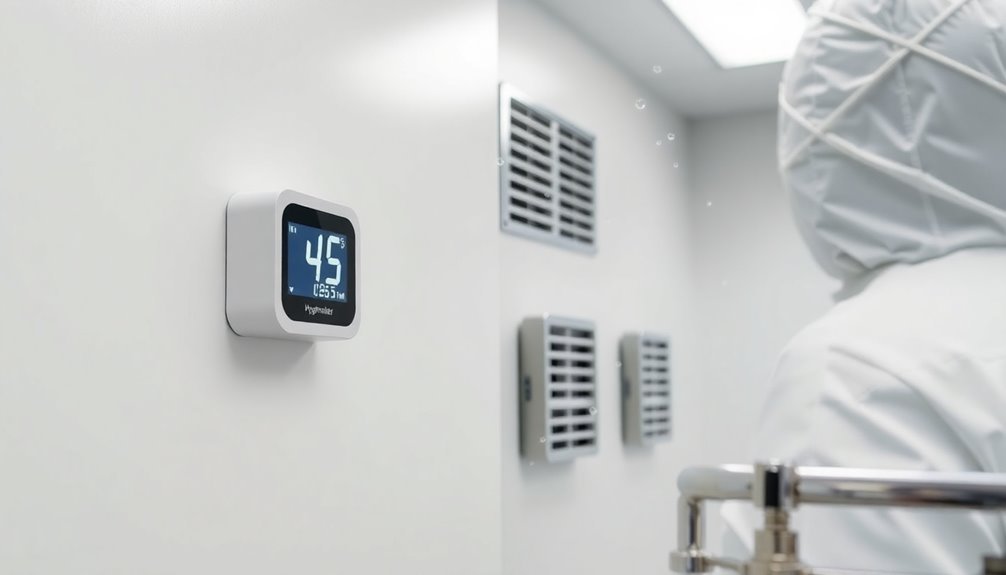
In clean room environments, static electricity poses considerable risks that can compromise both operations and product quality. You'll find that certain materials and conditions substantially increase the likelihood of static buildup.
Insulating materials like plate glass, Teflon, and polymers are particularly problematic as they can become highly charged, while even conductive surfaces can present unexpected risks to personnel and sensitive devices. Static build-up issues can lead to dangerous electrical failure of critical medical equipment.
Environmental conditions play a vital role in static accumulation. When humidity levels drop, you're more likely to experience static-related issues. Temperature fluctuations and HVAC system changes can create unstable conditions that promote static electricity generation.
The most common risk factors for static buildup include:
- Low humidity environments that allow charges to accumulate
- Insulating materials and surfaces in workstations
- Personnel wearing non-conductive footwear
- Rapid air movements around sensitive equipment
- Improper material handling and storage procedures
Your day-to-day operations can also contribute to static buildup through routine activities. You'll need to be particularly careful with individual workstations, where the combination of insulating materials, electronic equipment, and human interaction creates perfect conditions for static accumulation.
Humidity Control Best Practices
You'll need to monitor key control points throughout your cleanroom, including areas near entrances and equipment zones, to maintain ideal humidity levels.
Implementing desiccant wheel systems can provide reliable dehumidification for precise humidity management in sensitive manufacturing environments.
Create streamlined maintenance procedures that include regular sensor calibration, filter inspection, and system performance checks to guarantee consistent humidity control.
Setting up automated alert systems will notify your team immediately when humidity levels fall outside acceptable ranges, allowing for quick corrective actions before problems escalate.
Monitor Key Control Points
Monitoring key control points throughout your cleanroom's humidity management system stands as a critical foundation for maintaining ideal conditions. You'll need to maintain relative humidity levels between 30-40% to prevent both moisture-related issues and static electricity problems.
Regular hygrometer testing and calibration helps ensure accurate measurements of cleanroom conditions. Install hygrometers at strategic locations to continuously track these levels and respond quickly to any deviations.
Your monitoring strategy should include regular checks of both humidification and dehumidification equipment. Pay special attention to your industrial steam humidifiers and desiccant dehumidifiers, guaranteeing they're working in harmony to maintain consistent conditions.
Here are the key areas you'll need to monitor:
- Airlock zones where humidity fluctuations commonly occur due to personnel entry
- HVAC ducting points where steam injection takes place
- Areas near moisture-sensitive equipment or processes
- Locations where static electricity could impact production
- Critical process zones requiring precise humidity control
When you detect variations, take immediate corrective action using your humidity control systems. Use distilled or filtered water in your humidifiers to prevent scale buildup, and guarantee your dehumidification systems are operating at peak efficiency.
Remember that poor humidity control can lead to product contamination, equipment failure, and compromised quality control.
Streamline Maintenance Procedures
Maintaining an effective humidity control system requires streamlined procedures that focus on four key areas: regular inspection, calibration, preventive maintenance, and system upgrades.
You'll need to conduct frequent inspections of your humidity control equipment and test humidity levels to verify they stay within the 40-60% RH range.
It's crucial to implement a monitoring system that tracks both humidity and temperature, allowing you to take immediate corrective action when levels deviate from specifications.
Your calibration procedures should include regular sensor checks and system validation to maintain accuracy and regulatory compliance. Make sure you're using properly calibrated instruments and maintaining detailed records of all validation activities.
To prevent system failures, you'll want to schedule routine maintenance tasks, including filter changes and equipment cleaning. Use distilled water in your humidifiers to prevent mineral buildup, and verify proper airflow throughout your clean room.
Don't forget to assess your system's performance regularly and plan for necessary upgrades. You should update control software when needed and train your staff thoroughly on system operation.
Keep spare parts readily available and consider implementing redundant systems for critical applications.
Set Automated Alert Systems
Automated alert systems serve as your clean room's first line of defense against environmental fluctuations. By implementing wireless sensors and centralized monitoring, you'll receive instant notifications when humidity levels deviate from ideal ranges.
These systems continuously track critical parameters and trigger immediate responses through email, SMS, or mobile app alerts.
You'll need to integrate your alert system with your humidity control equipment, including humidifiers and dehumidification modules. Smart systems like ES100 and TS100 can automatically adjust to maintain precise moisture levels, helping you prevent static electricity issues and comply with CGMP standards.
Key components you should include in your automated alert system:
- Wireless sensors strategically placed throughout the clean room
- Real-time monitoring software with centralized data analysis
- Automated control algorithms for humidity adjustment
- Multiple notification channels (email, SMS, mobile apps)
- Integration with HVAC and humidification systems
Your alert system's effectiveness depends on proper programming and regular calibration. Set thresholds that align with your specific clean room requirements, and guarantee your system responds promptly to external climate changes.
This proactive approach helps maintain consistent humidity levels while preventing contamination risks.
Clean Room Environmental Requirements
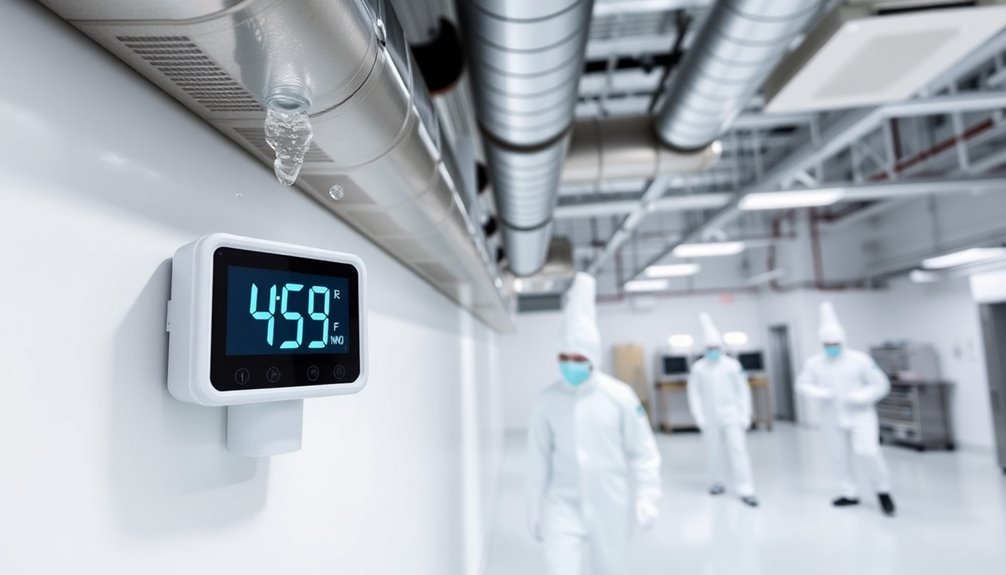
Clean room environmental requirements consistently demand precise control of both temperature and humidity levels to maintain ideal operating conditions. You'll need to maintain a temperature of 21°C with a variance of no more than 2°C to guarantee optimal performance and worker comfort. This precise temperature control prevents particle generation from staff shivering or sweating.
For humidity control, you should aim for 30-40% relative humidity (RH) in standard clean rooms, though aerospace facilities can operate effectively between 40-60% RH.
You'll find that maintaining these levels is vital, as low humidity leads to static buildup and electrostatic discharge, while high humidity causes condensation and bacterial growth.
To achieve these requirements, you'll need robust HVAC systems with humidity control features. You can utilize desiccant solutions or thermo-electric dehumidifiers when moisture levels rise too high, and evaporative humidifiers when additional moisture is needed.
It's imperative to monitor these conditions continuously using hygrometers and implement regular testing protocols. Your system's performance may fluctuate due to external environmental changes, so you'll need to maintain proper enclosure integrity and adjust set point controls accordingly.
Static Prevention Solutions
Static electricity poses a significant risk in clean rooms, making thorough prevention measures necessary for maintaining product quality and safety. To control static effectively, you'll need to maintain humidity levels above 55% RH, as this allows moisture in the air to naturally conduct and earth static charges.
Between 45-55% RH, you'll still experience static build-up, though at reduced levels.
You can implement various solutions to combat static electricity in your clean room:
- Install anti-static flooring systems (dissipative or conductive) to ground charges
- Use industrial steam humidifiers with your HVAC system
- Deploy ionization technology to neutralize static charges
- Implement proper grounding throughout the facility
- Require anti-static garments and proper gowning procedures
Your static prevention strategy should include multiple approaches. Start by installing anti-static flooring and wall panels to create a foundation for static control.
Add humidity control systems to maintain ideal moisture levels, and supplement with ionization technology where needed.
Don't forget to enforce strict clothing policies, prohibiting static-prone materials like fleece and requiring appropriate anti-static garments.
For areas around heat-generating equipment, you can add localized spray systems to maintain adequate humidity levels.
Humidity Monitoring Systems
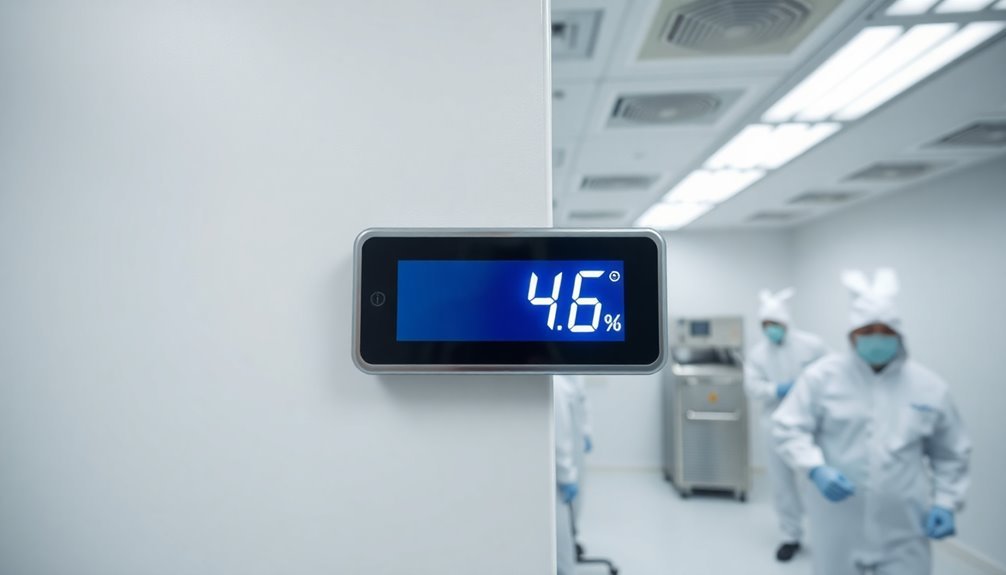
High-precision humidity monitoring systems form the backbone of any effective clean room operation. You'll need continuous, real-time monitoring to maintain the ideal 50% relative humidity level that prevents static electricity buildup. Modern systems offer remote access capabilities, allowing you to track conditions from anywhere through web-based platforms.
Monitoring Feature | Key Benefit |
---|---|
Remote Access | Track conditions from any location |
Advanced Alarms | Instant alerts for out-of-range levels |
24/7 Monitoring | Continuous data collection and control |
Data Logging | Historical tracking for compliance |
Today's humidity monitoring equipment includes various options to suit your specific needs. You can choose from capacitive sensing technology for high accuracy or wireless connectivity for seamless data transmission. Systems like the SRH series offer both analog and digital outputs, supporting BACnet and Modbus protocols for integration with your existing infrastructure.
Seasonal Humidity Management Strategies
Most clean room facilities require distinct humidity management approaches for summer and winter conditions. During summer months, you'll need to focus on dehumidification using air conditioning or desiccant systems to maintain levels below 70% relative humidity. Standard refrigeration equipment can achieve dew points of +40°F, effectively removing excess moisture from the incoming air.
Winter strategies shift toward humidification, as you'll need to add moisture to maintain minimum humidity levels of 40%. Industrial steam humidifiers and atomizing nozzles provide cost-effective solutions, but remember to use distilled or filtered water to prevent scale buildup on heating coils.
For ideal static prevention across industries, you'll want to maintain these key elements:
- Keep relative humidity above 55% to eliminate static electricity
- Integrate air conditioning with desiccant systems for thorough control
- Monitor and adjust for external weather conditions continuously
- Use localized humidification systems in static-sensitive areas
- Maintain precise temperature control to regulate humidity effectively
This balanced approach is particularly essential for pharmaceutical, electronics, and automotive manufacturing, where static electricity can compromise product quality and safety. Remember to take into account your specific industry requirements when implementing seasonal humidity management strategies.
Performance Impact of Humidity Control
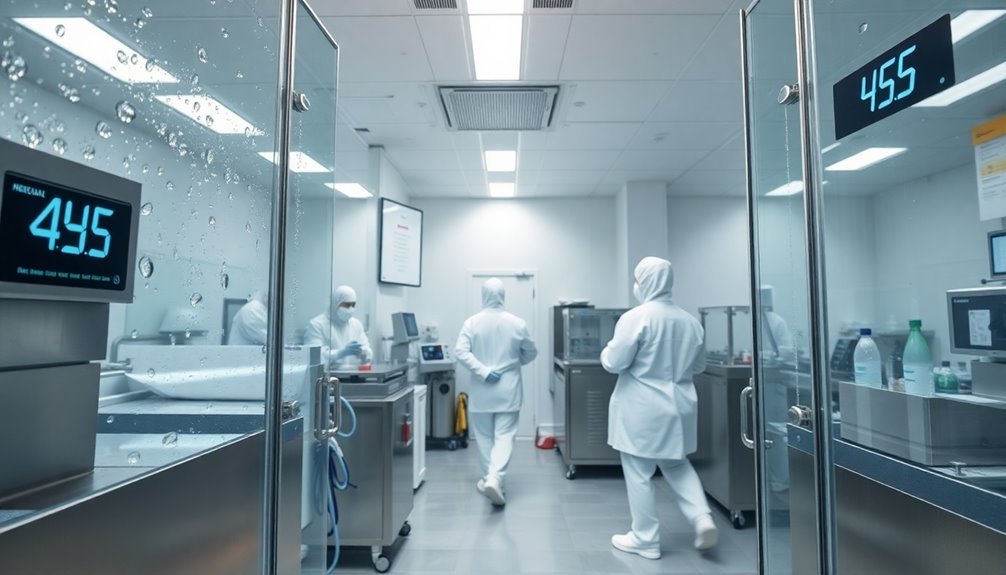
In maintaining cleanroom operations, proper humidity control directly impacts both equipment performance and process reliability. You'll find that maintaining humidity levels between 30% and 60% RH is vital for optimal performance, with levels above 50% providing the best static charge dissipation.
When humidity drops too low, you'll face increased risks of static electricity buildup, which can damage sensitive electronic components and attract contaminating particles through electrostatic attraction. Your lab technicians can inadvertently contribute to this problem by generating static charges through their insulating footwear.
However, you'll need to be careful not to let humidity levels exceed 60% RH. High humidity creates its own set of challenges, including condensation that can lead to equipment damage, bacterial growth, and corrosion of metal surfaces.
In pharmaceutical applications, you'll notice that excessive humidity can cause powder handling issues and clog tablet dies.
To maintain optimal performance, you should implement proper humidity control methods. Using humidifiers, dehumidifiers, or desiccant solutions while monitoring levels with hygrometers will help you maintain the sweet spot between 40% and 60% RH, where you'll achieve both static control and human comfort.
Frequently Asked Questions
How Long Does It Take to Stabilize Humidity After a Door Opening?
You'll see initial humidity stabilization within minutes, but complete stabilization can take several hours. It depends on your room's size, HVAC system efficiency, and how often you're opening the door.
Can Emergency Sprinkler Systems Affect Cleanroom Humidity Control Settings?
Yes, your cleanroom's humidity control can be disrupted when sprinklers activate. They'll introduce moisture that affects relative humidity levels, and you'll need your HVAC system to readjust to maintain proper environmental conditions.
What Backup Systems Are Recommended for Humidity Control During Power Outages?
You'll need UPS battery backup systems, resistive steam humidifiers, and automatic environmental controls. Install redundant systems and ultrasonic humidifiers as backup options to maintain ideal humidity levels during power disruptions.
How Often Should Humidity Sensors Be Calibrated for Optimal Performance?
You should calibrate your humidity sensors every 6-12 months, following manufacturer recommendations. If you're operating in harsh environments or notice drift issues, you'll need more frequent calibrations to maintain accuracy.
Do Different Cleanroom Classifications Require Different Humidity Control Response Times?
Yes, you'll need faster response times as cleanroom classifications become more stringent. ISO 5 and higher require immediate responses, while ISO 7 needs rapid adjustments, and ISO 8 can tolerate longer response times.
In Summary
You'll want to maintain relative humidity between 35-45% in your clean room to effectively prevent static electricity buildup. By keeping your humidity controls within this range, you're protecting sensitive equipment and maintaining product quality. Remember that you'll need to adjust your humidity management strategy seasonally and invest in reliable monitoring systems to guarantee consistent static prevention throughout your facility's operations.
Leave a Reply