To protect your electronics with ionization, you'll need systems that generate balanced positive and negative ions to neutralize static charges. Verify that your ionizers maintain balance voltages below 5 volts and keep charged insulators at proper distances (within 1 inch for charges up to 125V, 12 inches for charges over 2000V). You'll want regular maintenance of emitter points and automated monitoring systems to verify performance. Choose between alpha, corona, or soft X-ray ionization based on your environment and specific needs. Understanding these core requirements will help you build a thorough ESD protection strategy that safeguards your valuable electronic components.
Ionization Basics in ESD Control
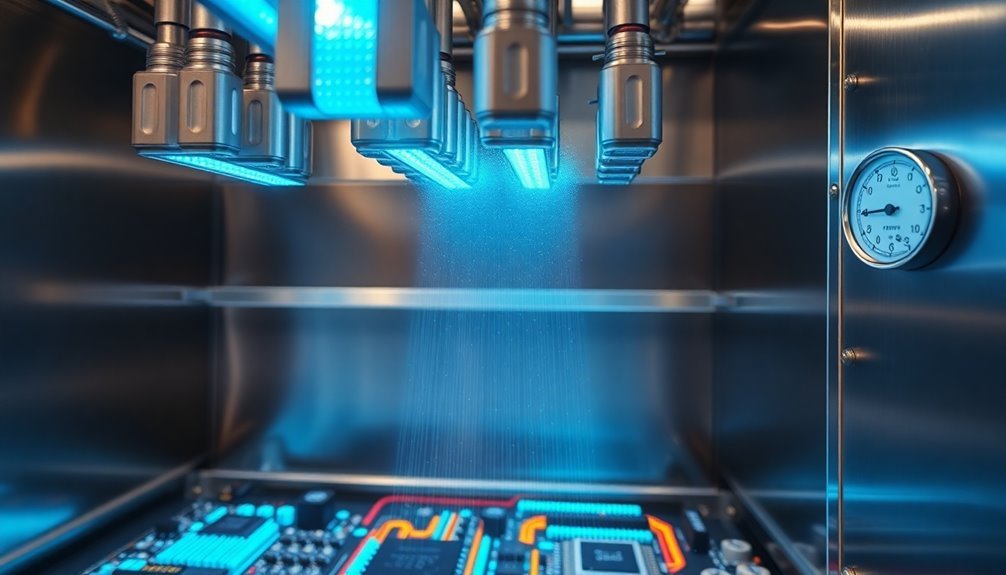
Effectively controlling electrostatic discharge requires a thorough understanding of ionization principles. You'll find that ionization works by generating both positive and negative ions to neutralize static charges that build up on insulating materials.
This process involves atoms either losing or gaining electrons, requiring energy input for electron removal while releasing energy when electrons are added. Electromagnetic radiation interactions can trigger the ionization process.
When you're working with electronics manufacturing, you'll need to pay special attention to ionization's role in ESD control. It's particularly essential when you're handling insulators that can't be grounded through conventional methods.
You'll discover that different types of ionizers, including bench top, overhead, and point-of-use models, are designed to address specific application needs in your manufacturing environment.
To protect your sensitive electronic components, you'll need to guarantee your ionization system is properly balanced, producing equal amounts of positive and negative ions. The effectiveness of ionization can substantially reduce failure rates in your manufacturing process, especially compared to relying solely on relative humidity control.
With proper implementation, you can achieve neutralization of static charges within seconds, maintaining safe voltage levels throughout your facility.
Understanding Static Charge Risks
You'll need to identify key charge buildup zones in your facility where static risks are highest, including areas with synthetic materials and high-friction processes.
Your voltage monitoring should focus on establishing safe thresholds that protect your most sensitive components, as even low-level discharges can damage modern electronics.
When evaluating insulator risks in your workspace, you should regularly test non-conductive materials and surfaces using a static field meter to measure potential charge accumulation points.
Maintaining appropriate humidity control systems in your facility helps reduce static electricity buildup and protects sensitive equipment from damage.
Charge Buildup Impact Zones
Within the domain of electronics protection, understanding charge buildup impact zones is essential for preventing potential damage and safety hazards. These zones primarily affect three critical areas: personnel safety, equipment integrity, and production processes.
Personnel Safety Zones
In personnel safety zones, you need to watch for areas where electric shocks can occur, particularly in dry environments where charge buildup is more likely. These risks increase with faster material separation and larger contact surfaces between dissimilar materials. The human body can accumulate voltages exceeding 10,000 V in low-humidity conditions.
Equipment Impact Zones
Equipment impact zones focus on electronic components and mechanical systems. Your sensitive devices are particularly vulnerable when they're interconnected through cables, and the risk increases with modern miniaturization. You'll need to pay special attention to areas containing bearings and other mechanical components that can suffer from static damage.
Production Impact Zones
Production impact zones involve areas where you're processing materials like paper, plastics, or powders. Static buildup can severely disrupt these processes, especially when impurities and contaminants are present. To protect these zones, you'll want to implement proper bonding and grounding systems, use static-resistant designs, and maintain appropriate humidity levels.
Voltage Thresholds Matter Most
Understanding voltage thresholds forms the cornerstone of static charge risk management in electronics protection. You'll need to pay close attention to two critical models: the Human Body Model (HBM) at 1,000 volts and the Charged Device Model (CDM) at 250 volts.
These thresholds aren't arbitrary – they're based on extensive research and industry standards like ANSI/ESD S20.20 and IEC 61340-5-1. Effective implementation requires equipotential bonding techniques to minimize charge generation between surfaces.
You're facing significant risks when these thresholds are exceeded:
- Immediate component damage that can result in costly repairs and replacements
- Latent defects that may surface weeks or months after the initial discharge
- Data corruption that can compromise your electronic systems' integrity
You'll notice that as electronics technology advances, these threshold levels tend to decrease, making proper ESD protection even more critical. When you're working with devices that have lower ESD target levels, you'll need to implement additional protective measures beyond basic controls.
The economic impact of static discharge damage isn't trivial – it's estimated to cost billions annually across industries. That's why you can't afford to ignore these threshold requirements in your electronics protection strategy.
Insulator Risk Assessment Methods
Proper insulator risk assessment starts with recognizing how static charges accumulate in your electronic environment. You'll need to identify potential sources of static electricity, including human movement, synthetic materials, and varying environmental conditions that can trigger electrostatic discharge (ESD) events.
Risk Factor | Assessment Method |
---|---|
Material Properties | Test surface resistivity and charging potential of insulators |
Environmental Conditions | Monitor humidity levels and air ionization effectiveness |
Contact/Separation Events | Evaluate material interactions and movement patterns |
Charge Generation Sources | Map locations of high-risk activities and materials |
Your assessment should focus on understanding how different materials interact within your workspace. Pay special attention to high-charging insulators like plastics and synthetic materials, as they pose the greatest ESD risk. You'll want to examine surface properties, including texture and cleanliness, since they substantially impact static generation.
To effectively mitigate risks, you must implement controls based on your findings. This includes selecting appropriate materials, installing proper grounding systems, and using ESD-protective equipment. Regular monitoring and updating of these controls guarantees your protection measures remain effective against static-related threats to your electronic components. A thorough understanding of ionic contamination and its potential to create leakage currents, especially in humid conditions, is crucial for comprehensive risk assessment.
Types of Ionization Systems
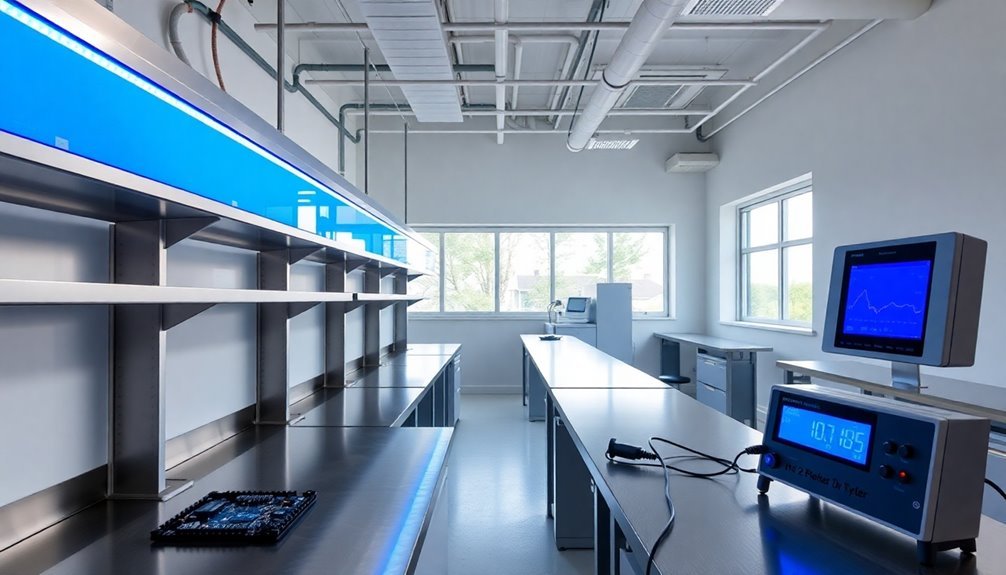
When protecting your electronic components, you'll need to evaluate two primary ionization approaches: alpha ionization systems, which operate without power and excel in extreme environments, and corona discharge systems that use voltage to generate ions.
Light-based ionization methods like soft X-ray systems provide another effective option for static elimination.
You'll find corona discharge systems available in AC, steady DC, and pulsed DC variants, each offering distinct advantages for specific applications.
To select the right ionization method, you must assess your specific needs, including installation space, object movement speed, and environmental conditions that could affect system performance.
Alpha Ionization Advantages
Alpha ionization systems stand out as powerhouses in static elimination, offering unique advantages over traditional ionization methods. You'll appreciate their maintenance-free operation and exceptional reliability in sensitive environments where electrical power sources aren't feasible. Alpha ionization generates ions through alpha particle collisions with air molecules.
These systems provide consistent, balanced ion production without requiring the regular adjustments often needed with corona-based alternatives.
- No external power requirements, making them ideal for explosive environments and areas where electrical connections pose risks
- Operational effectiveness across extreme temperatures (-40°C to 180°C), perfect for demanding manufacturing conditions
- Superior performance in confined spaces, especially when working with Class 0 static-sensitive components
When you're dealing with highly sensitive electronic components or operating in tight spaces, alpha ionization delivers precise static control within a 1-3 inch range. You'll find these systems particularly valuable in applications requiring predictable, reliable ionization without electrical interference.
While the effective range is limited, adding airflow can extend their reach for broader coverage. The cost efficiency comes from their consistent performance and minimal maintenance requirements, though you'll need to plan for periodic replacements due to the natural decay of Polonium-210.
Corona Discharge Systems
Corona discharge systems represent a versatile approach to ionization that you'll commonly find in electronics manufacturing and processing environments. These systems operate by creating an intense electric field that breaks down air molecules into ions, which occurs within a small plasma zone just 50-100 µm from the emitter point.
You'll encounter three main types of corona discharge ionizers in electronics protection: AC, DC steady-state, and pulsed DC. AC systems generate both positive and negative ions from a single emitter but face ion recombination challenges. The ionization process begins when an ultraviolet photon strike initiates the electron avalanche effect.
DC steady-state systems use separate emitters for each polarity, reducing recombination issues. Pulsed DC offers an ideal balance by alternating between polarities at lower frequencies than AC.
To maintain effective corona discharge performance, you'll need to evaluate the critical field strength of 30 kV/cm at sea level. You can prevent unwanted discharge and power loss by implementing corona rings and avoiding sharp edges on electrodes.
For electronics protection, you'll find these systems particularly effective at static elimination, though they also serve additional purposes like air filtration and cooling in electronic devices.
Selecting Right Ionization Method
Selecting the right ionization method for electronics protection depends on a wide range of operational factors. While corona discharge is common, you'll find several other effective ionization systems like soft X-ray, UV, and radiation types. Each system serves specific applications, and you'll need to match the method to your unique requirements.
Clean rooms and laminar flow hoods work best with ceiling or bar-type ionizers.
Assembly areas without airflow benefit from fan-powered blowers or compressed gas.
PCB manufacturing requires specialized point-of-use ionizers for targeted protection.
When choosing an ionization system, you'll need to evaluate the installation space, movement speed of your materials, and the amount of static electricity you're dealing with. For instance, if you're working in a mini-environment or with conveyor systems, you'll require specific ionizer designs that fit these spaces.
Don't forget to assess the ion balance needed for effective static elimination and whether compressed air is available or suitable for your application.
Insulator Charge Distance Requirements
Within the domain of electronics protection, understanding insulator charge distance requirements is essential for preventing ESD damage. You'll need to maintain specific distance thresholds when working with charged insulators near ESD-sensitive items.
For insulators charged to more than 125 volts, keep them within 1 inch of the sensitive item for effective ionization. If the charge exceeds 2000 volts, maintain a 12-inch distance.
You must remember that electric field strength decreases with the square of the distance. When measuring insulators, your field meter readings are only valid at 1 inch away. If you measure 2500 volts/in, you'll need to keep the insulator at least 12 inches from ESD-sensitive devices. For measurements of 1000 volts/in, maintain a minimum 1-inch distance.
At your workstation, you'll need to use ionization or other charge-mitigating techniques to neutralize electrostatic fields on process-essential insulators. Ionizers create both positive and negative ions to neutralize static charges within seconds. They're particularly important for controlling charges on non-removable insulators and isolated conductors, helping minimize triboelectric charging and reducing ElectroStatic Attraction.
Alpha Versus Corona Ionization
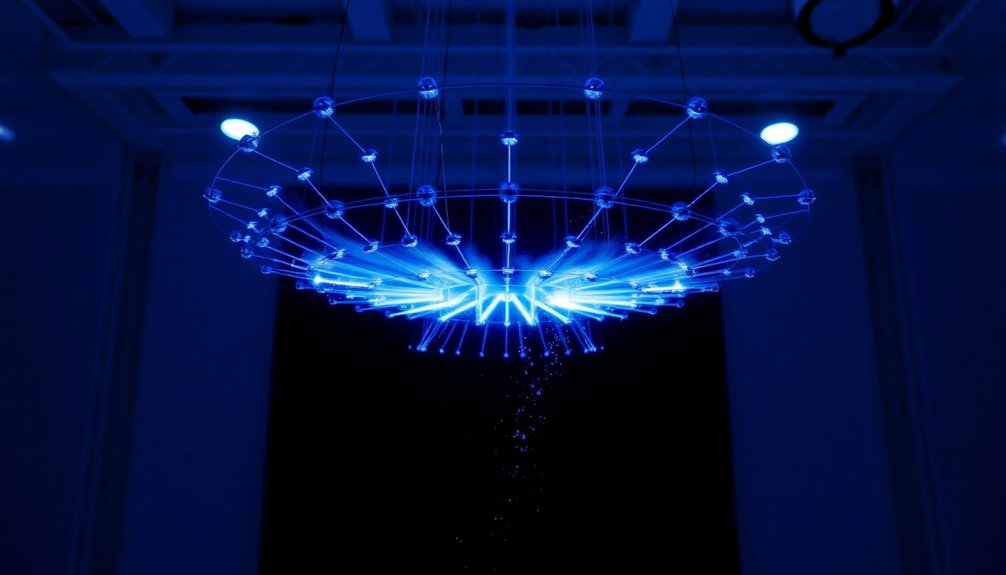
When choosing between ionization methods for your ESD protection system, you'll need to understand the key differences between alpha and corona ionization technologies.
Alpha ionization uses Polonium-210 to create balanced positive and negative ions without requiring an external power source. Corona ionization, on the other hand, relies on an electric field powered by an external source to strip electrons from air molecules.
- Alpha ionization works best in explosive, harsh, or confined environments where power sources aren't practical.
- Corona ionization offers a more cost-effective solution for less sensitive areas but requires regular maintenance.
Both methods effectively neutralize static charges, but their applications differ based on environmental conditions.
You'll want to select alpha ionization when working with extremely sensitive components or in hazardous environments where external power isn't desired. The encapsulated radioactive material poses no safety risks under normal conditions, and it consistently produces balanced ions.
If you're operating in a standard environment with available power sources, corona ionization might be your more economical choice. Consider your specific needs regarding maintenance capabilities, environmental conditions, and component sensitivity when making your final decision.
Core Benefits of Ionization
You'll find that ionization systems effectively neutralize static charges through a balanced release of positive and negative ions, protecting your sensitive electronic components during manufacturing.
Your ESD control program becomes more robust when you implement ionization, as it actively manages charges that can't be controlled through standard grounding methods.
The safe handling of electronic components is enhanced because ionizers continuously work to neutralize potentially damaging charges on both conductors and insulators in your workspace.
Static Charge Neutralization Process
Static charge neutralization through ionization delivers three essential benefits that make it indispensable for electronics protection. When you're working with sensitive electronic components, you'll need to implement effective ionization methods to prevent ESD damage and maintain ideal manufacturing conditions.
The process relies on balanced ionization systems that generate both positive and negative ions to neutralize unwanted charges on surfaces and materials.
- You'll protect sensitive components from ESD damage while reducing particle adhesion on critical surfaces
- You can maintain extremely clean conditions essential for medical and aerospace applications
- You'll achieve precise control over manufacturing processes, improving product quality
To implement effective static charge neutralization, you'll need to choose between several proven methods. Bipolar ionization uses both positive and negative ions, while photoionization employs light to generate ions without airflow.
AC ionizers alternate high voltage to create balanced ion production, and DC ionizers use separate power supplies for ion generation. Modern systems incorporate real-time monitoring and IoT capabilities for proactive control.
You'll also need to guarantee proper isolation from ground and maintain balanced ion production to protect against both CDM and CBE ESD damage effectively.
Safe Handling During Manufacturing
Safety in electronics manufacturing hinges on properly implemented ionization systems that protect sensitive components during handling and assembly. You'll need to position your ionizers strategically, maintaining at least 20cm distance between emitter points and products while guaranteeing thorough coverage of your work areas.
For the best protection of your sensitive electronics, you'll want to implement both ceiling-mounted and localized ionization solutions. Ceiling units provide broad coverage, while workstation-specific ionizers deliver faster neutralization where you need it most.
Protection Aspect | Requirement | Benefit |
---|---|---|
Emitter Placement | 20cm minimum distance | Prevents charging damage |
Coverage Type | Ceiling & local units | Thorough protection |
Maintenance | Regular tip cleaning | Consistent performance |
Balance Control | <5V offset voltage | Reliable neutralization |
Monitoring | Automated systems | Continuous protection |
Your ionization system must comply with ANSI/ESD S20.20 standards and maintain balance voltages below 5 volts. You'll need to incorporate regular maintenance schedules, including emitter cleaning and performance monitoring, to guarantee your system continues providing reliable static protection. Remember, proper ionization is essential where you can't eliminate insulators from your manufacturing process.
Protecting Sensitive Electronic Components
Modern electronics demand robust protection against invisible threats, with ionization serving as a vital defense mechanism for sensitive components. When you're handling sensitive electronic components, proper ionization systems help neutralize static charges that could otherwise damage or destroy your valuable devices.
By implementing balanced ion output technology, you'll effectively eliminate both positive and negative static charges while preventing new charge generation.
- Neutralizes harmful static charges on insulators and isolated conductors, protecting your components from ESD damage
- Reduces triboelectric charging during manufacturing processes, maintaining the integrity of sensitive electronics
- Eliminates ElectroStatic Attraction (ESA) to prevent contamination from charged particles
You'll find ionization particularly essential in semiconductor manufacturing, where even minimal static discharge can compromise entire batches of components.
To maximize protection, guarantee your ionization system maintains electronic isolation and receives regular maintenance. Modern ionizers offer advanced features like auto-cleaning and monitoring capabilities, helping you maintain consistent performance.
When selecting an ionization system, focus on long-term reliability and compliance with ANSI/ESD S20.20 standards. Don't forget to verify that your chosen system includes thorough monitoring and alarm features to alert you of any performance issues.
Selecting the Right Ionizer
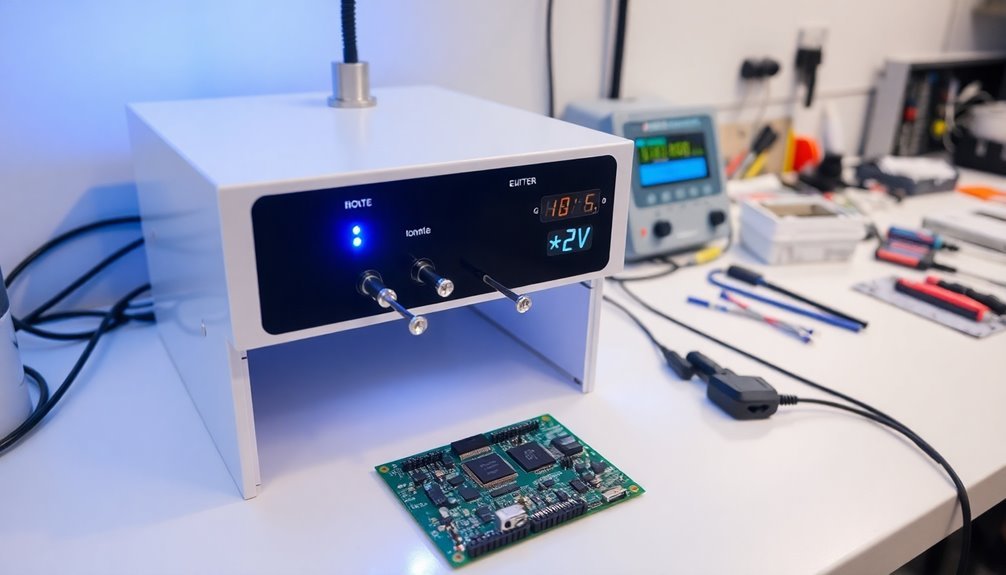
Selecting an appropriate ionizer requires careful evaluation of three critical factors: the ionization method, performance requirements, and environmental conditions.
You'll need to examine your specific application to determine whether voltage-based, self-discharge, or light-based ionization methods best suit your needs. Corona discharge types, including AC, DC, and pulsed DC, offer different advantages depending on your setup.
If you're working with particularly sensitive electronics, you might want to evaluate soft X-ray or UV systems.
When evaluating performance requirements, focus on the ion balance needed for your application and whether you'll need compressed air integration. You must also account for maintenance demands, including regular cleaning of emitter points and filter replacements.
Don't forget to verify compatibility with nearby electronic equipment.
Your environmental conditions will substantially impact your choice. Evaluate the installation space, object movement speed, and the amount of static electricity you're dealing with.
You'll need to follow ANSI/ESD S20.20-2014 guidelines, ensuring proper ionization when insulators could be charged to more than 125 volts within 1 inch or 2000 volts within 12 inches of ESD sensitive items.
Ionization in Manufacturing Environments
Once you've selected the appropriate ionizer for your needs, implementing it effectively in manufacturing environments presents its own set of challenges. You'll need to focus on proper placement, maintenance, and air distribution to guarantee the best performance. Corona ionization, the most common method, requires careful attention to emitter placement and grounding considerations.
When implementing ionization in your manufacturing setup, you must maintain distances between 4,000V to 20,000V emitter points and grounded surfaces to maximize ion generation. You'll find that air movement is vital – whether through fans or compressed gas – to properly distribute ions to your target areas.
Regular cleaning of emitter tips is essential to maintain consistent performance and prevent decreased effectiveness.
Proper placement of unshielded emitter points away from grounded surfaces helps maximize useful ionization.
Short distances between ionizers and products are critical, especially in confined spaces like mini-environments.
Your ionization strategy should account for specific manufacturing requirements, whether you're working with PCB assembly, flat panel displays, or semiconductor manufacturing.
Localized ionizers typically offer more flexibility and effectiveness than ceiling-mounted systems, particularly in cleanroom environments where contamination control is paramount.
ESD Program Integration Strategies
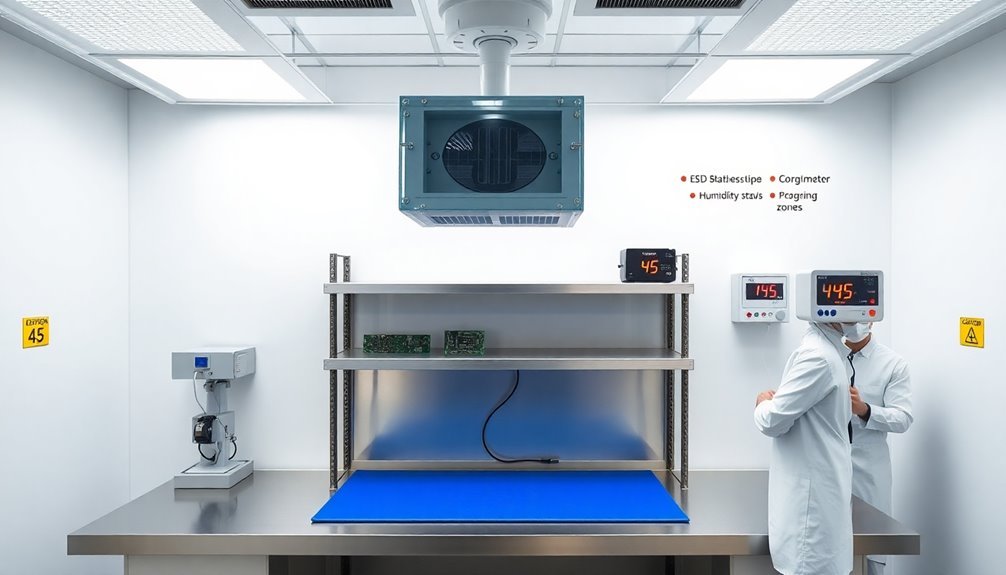
Integrating an effective ESD program requires a systematic approach that aligns with ANSI/ESD S20.20-2016 standards. You'll need to start by appointing an ESD Control Program Manager who'll oversee the entire implementation process and verify ongoing compliance with established guidelines.
Your first step should be conducting a thorough risk assessment across all operational areas that handle ESD-sensitive components. Use the Reliability Analysis Center V-ZAP data book to determine component susceptibility levels and identify potential vulnerabilities in your manufacturing and handling processes.
You'll want to develop detailed local ESD control plans for each workstation, ensuring they're tailored to specific job functions and requirements.
It's essential to implement a thorough training program for all employees who handle sensitive electronics, and you should establish regular audit schedules to monitor compliance.
Remember to maintain detailed records of your configuration control procedures, training sessions, and audit results. You'll need this documentation to demonstrate program adherence and for potential certification through ISO 9000 registrars.
Keep your program dynamic by continuously updating it based on audit findings and evolving industry standards.
Workstation Ionization Standards
Proper ionization standards set the foundation for effective ESD control at electronics workstations. You'll need to implement specific ionization methods, including bar ionizers, blowers, and compressed-gas blow-off devices, while guaranteeing they're mounted within a 1-meter distance from ESD-sensitive products.
When selecting ionizers, consider steady-state DC, AC, or alpha ionizers based on your application requirements, maintaining offset voltages of ±50 V for products sensitive to 100-V human body model ESD.
Key attention points for your workstation standards:
- Maintain compliance with S20.20 and ESD STM3.1-2000 test methods to guarantee your ionization systems meet industry requirements.
- Position ionizers strategically above or directly on worksurfaces to effectively neutralize static charges on process-essential insulators.
- Implement regular maintenance schedules and performance monitoring to verify continuous functionality.
To meet these standards, you'll need to customize your ionization solutions for each workstation while documenting system performance and maintenance activities. Don't forget to integrate proper grounding requirements and guarantee your workstations are situated within Electrostatic Protected Areas (EPAs).
Regular inspections and personnel training will help maintain the effectiveness of your ionization systems.
Frequently Asked Questions
How Often Should Ionizers Be Calibrated and Maintained for Optimal Performance?
You should calibrate ionizers every 6 months minimum, but adjust frequency based on your environment. Clean emitter points regularly, check balance monthly, and maintain more frequently if used in critical cleanroom applications.
What Are the Safety Precautions When Handling Alpha Ionizers Containing Radioactive Materials?
You should never tamper with sealed alpha ionizers, maintain regular safety checks, and follow proper disposal guidelines. Since they're encapsulated, they're safe when handled properly, but always observe radiation safety protocols.
Can Ionizers Interfere With Sensitive Electronic Test Equipment During Measurements?
Yes, your ionizers can interfere with sensitive test equipment. You'll need to position them carefully away from measurement devices and consider using ultra-low EMI models to minimize electromagnetic field disruptions during testing.
What Is the Typical Lifespan of Different Types of Ionizer Emitter Points?
You'll get 1-2 years from titanium points, 6-12 months from tungsten, and 2-3 years from silicon emitters. Your maintenance practices and environmental conditions will greatly impact these lifespans.
How Do Temperature and Humidity Affect Ionizer Performance and Effectiveness?
You'll find that temperature has minimal impact on ionizer performance, but humidity matters more. Lower humidity reduces your ionizer's effectiveness, so you should maintain levels above 30% for the best static control.
In Summary
You'll need to carefully integrate ionization systems into your overall ESD control program while following proper distance, maintenance, and testing requirements. Don't overlook regular monitoring of your ionizers' performance and decay times. By selecting the right type of ionizer for your specific application and maintaining strict workstation standards, you'll effectively protect sensitive electronics from damaging static charges throughout your manufacturing process.
Leave a Reply