Laboratory testing of ESD safe packaging matters because it's your primary defense against costly electronic failures and compliance issues. You'll need proper validation to guarantee your packaging meets essential ANSI/ESD S541 and IEC standards, as approximately 30% of electronic failures stem from ESD events. Testing under controlled conditions (12%±3% RH, 73°F±5°F) verifies that your materials provide genuine protection against static discharge and moisture damage. Through extensive evaluations, you can identify potential failures before they impact your hardware investments. Exploring the testing protocols can help you safeguard your sensitive electronic components and maintain regulatory compliance.
Standards and Compliance Requirements
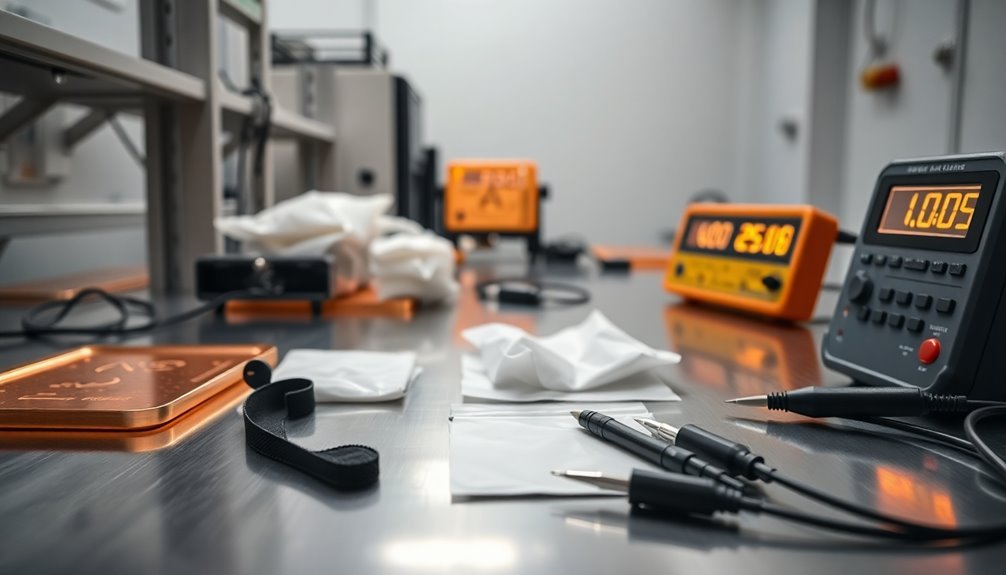
Numerous standards govern ESD safe packaging, with ANSI/ESD S541 serving as the primary framework for packaging materials.
Counterfeit packaging concerns have made laboratory testing increasingly critical for validating authentic ESD materials.
You'll need to guarantee your packaging meets specific requirements outlined in ANSI/ESD S11.4 for static control bags, including vital marking requirements for traceability. The multi-industry standard ANSI/ESD S20.20 provides thorough guidelines for ESD Control Programs that you must follow.
When testing your packaging materials, you'll need to maintain strict environmental conditions of 12%±3% relative humidity and 73°F±5°F for a minimum of 48 hours. Static charge retention increases significantly when humidity levels drop below specification.
Your materials must meet resistance limits according to ANSI/ESD STM11.11 and ANSI/ESD STM11.12, while static shielding bags should demonstrate discharge protection below 20 nJ per ANSI/ESD STM11.31.
You can't overlook traceability requirements – all bags must display manufacturer information and lot codes.
You'll also need to take into account international standards like IEC 61340-5-1 if you're operating globally.
Regular verification of incoming materials is vital to prevent substitution or quality degradation.
Remember that your industry might've additional specific requirements, and your contracts may stipulate extra ESD packaging criteria.
ESD Testing Methods
You'll need to understand two critical aspects when testing ESD safe packaging: simulation testing protocols and compliance testing standards.
Standard simulation protocols require you to perform both contact and air discharge tests using calibrated ESD simulators that meet IEC 61000-4-2 requirements. Monitoring equipment allows for precise measurement of device performance during testing.
Your testing must follow strict compliance standards, including proper documentation of test conditions, voltage levels, and discharge repetitions to guarantee your packaging meets industry-specific ESD protection requirements. Testing should include static decay measurements to evaluate how quickly your packaging material can dissipate electrical charges when grounded.
Simulation Testing Protocols
Effective ESD testing protocols rely on carefully controlled simulations that replicate real-world electrostatic discharge events. You'll need specialized ESD simulators, proper discharge networks, and consistent environmental controls to guarantee reliable results.
Testing should follow IEC 61000-4-2 standards for comprehensive evaluation of packaging materials.
When testing packaging materials, both contact and air discharge methods provide valuable insights into how your products will perform under various electrostatic conditions. Simulations help identify potential failure locations before investing in costly hardware prototypes.
Your simulation setup must include these essential components for accurate testing:
- Ground planes and coupling planes for consistent test environments
- Temperature and humidity controls to maintain testing reliability
- Discharge networks that generate proper ESD pulse characteristics
- Verified ESD simulators with annual calibration checks
- Current waveform monitoring equipment for precise measurements
You'll want to focus on both Human Body Model (HBM) and Charged Device Model (CDM) testing, as they represent the most common real-world scenarios. The HBM simulates human contact discharge, while CDM replicates device-to-device interactions.
Compliance Testing Standards
Through rigorous international standards, ESD compliance testing guarantees packaging materials meet strict electrostatic protection requirements. You'll find that IEC 61000-4-2 serves as the primary standard, establishing fundamental test methods and specifications for ESD protection. When you're developing ESD-safe packaging, you'll need to ascertain compliance with both general and industry-specific standards. Documentation is essential since approximately 30% of electronic failures result from ESD events. Successful testing requires accredited labs to provide comprehensive evaluations alongside other compliance certifications.
Standard | Application | Test Level | Key Requirement |
---|---|---|---|
IEC 61000-4-2 | General Electronics | ±8kV contact | Discharge Network Verification |
ANSI/ESD S20.20 | Manufacturing | ±200V to ±2kV | Control Program Implementation |
IEC 60601-1-2 | Medical Devices | ±8kV air | Enhanced Protection Levels |
ISO 10605 | Automotive | ±25kV max | Extended Voltage Range |
To achieve compliance, you'll need to use specialized ESD testing equipment, including ESD generators and discharge networks. Your testing process should incorporate both pre-compliance assessments and final verification testing. It is vital to maintain detailed test reports documenting your results, as these serve as significant evidence for regulatory compliance and quality assurance purposes. When you work with an accredited testing laboratory, they'll help guarantee your packaging meets all relevant standards.
Material Selection Criteria
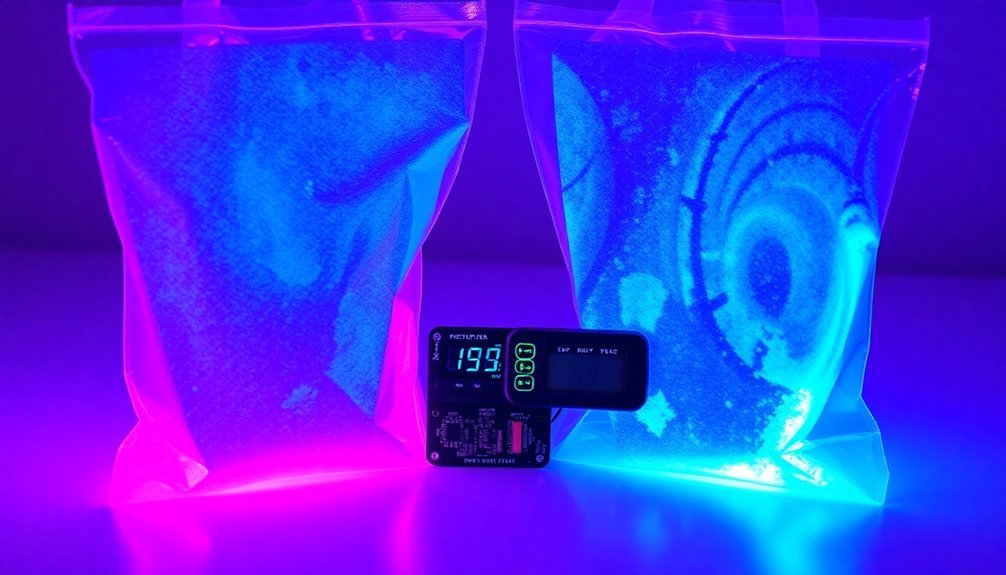
Selecting the right materials for ESD safe packaging requires a systematic evaluation of multiple critical factors. You'll need to understand your device's sensitivity levels through testing and manufacturer data before making any material choices.
Your packaging must effectively protect against both ESD damage and physical harm while considering the specific distribution environment it'll encounter. Cushioned bags with bubble layers provide essential impact protection for delicate components.
Major industries like automotive and defense rely heavily on proper ESD packaging solutions for sensitive equipment.
When choosing materials, consider these essential criteria:
- Device sensitivity level and required protection class
- Environmental conditions during storage and transport
- Physical protection requirements and durability needs
- Cost-effectiveness and reusability options
- Compliance with industry standards and testing protocols
You'll want to match your material selection to the intended use, whether it's for inside or outside an EPA (ESD Protected Area). For intimate contact packaging, opt for low charge generation materials with dissipative or conductive properties.
If you're packaging for transport outside an EPA, you'll need additional electrostatic discharge shielding. Don't forget to factor in moisture protection requirements – you might need specialized barrier materials or desiccants for moisture-sensitive items.
Remember that all material choices must be validated through proper testing to guarantee they meet your ESD protection needs.
Environmental Testing Parameters
After identifying suitable materials, proper environmental testing guarantees your ESD packaging will perform reliably in real-world conditions.
You'll need to maintain strict environmental parameters of 12%±3% relative humidity and 73±5°F for a minimum of 48 hours during testing to confirm accurate results.
Your testing protocols must follow specific standards, including ANSI/ESD STM11.11-2015 for surface resistance and ANSI/ESD STM11.12-2015 for volume resistance tests.
You'll need to use calibrated equipment and verify measurements against reference values of 1.0 x 10^12 Ω. Don't skip the preconditioning phase, as some materials require oven conditioning at 160°F for 14 days before standard testing.
Low humidity testing is essential because materials that pass at higher RH levels might fail when conditions are drier.
You must keep your samples in the test chamber throughout the entire testing period to maintain integrity.
Remember that temperature and humidity greatly impact ESD events – lower values of either typically increase the likelihood of discharge.
If you're using air discharge methods to simulate real-world conditions, you'll need to pay extra attention to environmental controls, as these tests are particularly sensitive to atmospheric variations.
Quality Control Measures
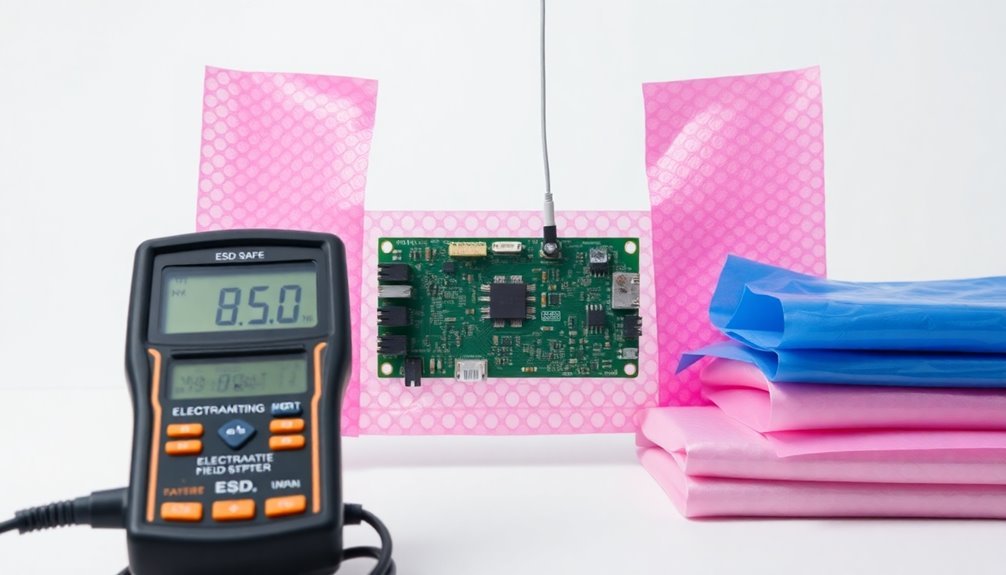
Reliable quality control for ESD safe packaging requires five essential measures: laboratory accreditation, standardized testing procedures, material verification, supply chain monitoring, and thorough documentation.
You'll need to work with accredited laboratories that follow established standards like ANSI/ESD S541 and IEC 61000-4-2 to guarantee your packaging meets industry requirements.
To maintain quality control throughout your supply chain, you should implement these critical checkpoints:
- Regular inspection of ESD bags for physical damage or wear
- Verification of proper environmental conditions during testing (12%±3% RH, 73±5°F)
- Confirmation of authentic packaging through traceability markers
- Validation of test equipment calibration and certification
- Documentation of all test results and material specifications
Your quality control process must include periodic verification of incoming materials to prevent counterfeit products from entering your supply chain.
Don't forget to check the credentials of potential ESD test labs before issuing purchase orders.
By maintaining strict quality control measures, you're protecting sensitive electronic components and guaranteeing compliance with industry standards.
Remember that proper documentation and labeling are essential for traceability throughout the manufacturing process.
Risk Assessment Protocols
You'll need to establish a systematic approach to failure mode analysis by evaluating ESD packaging under extreme environmental conditions and identifying potential weak points in the material composition.
When setting up your testing environment, you must maintain strict control over humidity levels (12%±3%RH) and temperature while utilizing calibrated ESD generators and current probes to ascertain accurate results.
Your compliance validation process should include regular verification of manufacturer certifications, lot code traceability, and performance testing against ANSI/ESD S541 and IEC 61000-4-2 standards to ensure reliable ESD protection.
Failure Mode Analysis Steps
The systematic process of Failure Mode Analysis requires a structured approach to identify and assess potential risks in ESD-safe packaging.
You'll need to follow specific steps to guarantee your packaging meets required safety standards and effectively protects sensitive electronic components from ESD damage.
When conducting your failure mode analysis, you'll work through a thorough evaluation process that combines both quantitative and qualitative assessments.
You're looking for potential failure points that could compromise your packaging's ESD protection capabilities, from material degradation to design flaws.
Here are the essential steps you'll need to follow in your analysis:
- Define your scope clearly, determining whether you're examining component-level or system-level packaging elements
- Identify all possible failure modes that could affect your packaging's ESD protection performance
- Analyze the effects of each potential failure on your packaging's protective function
- Assess risks using severity ratings, occurrence probability, and detectability metrics
- Develop specific mitigation strategies to address identified risks and improve package reliability
This structured approach guarantees you'll catch potential issues before they become actual problems, saving time and resources while maintaining product integrity.
Testing Environment Setup Guidelines
Setting up a proper testing environment for ESD-safe packaging demands strict adherence to temperature and humidity controls while following established risk assessment protocols.
You'll need to maintain temperatures at 730±50°F (230°C±30°C) and relative humidity at 12%±3% to guarantee reliable test results.
Your testing must comply with ANSI/ESD S541 and ANSI/ESD S20.20 standards, and you should only work with accredited ESD laboratories that use calibrated, lab-grade equipment.
Don't overlook the importance of environmental conditioning, as testing at ambient conditions won't provide accurate results.
You'll need to account for material variability and device sensitivity in your risk assessment.
Be vigilant about counterfeit materials by thoroughly vetting your supply chain and test labs.
When conducting tests, you must use advanced ESD instrumentation and simulators in controlled environments to evaluate product resistance accurately.
Remember that proper testing environments help you avoid liability issues while guaranteeing compliance with safety regulations.
Compliance Validation Methods
Validating ESD packaging compliance requires thorough risk assessment protocols aligned with ANSI/ESD S541 and IEC 61340-5-1 standards.
You'll need to verify that your packaging materials undergo extensive testing at accredited laboratories under strictly controlled environmental conditions (12%±3%RH, 73°F±5°F) for a minimum of 48 hours.
When validating compliance, you must verify that your packaging materials meet these critical requirements:
- Surface resistance testing according to ANSI/ESD STM11.11
- Volume resistance verification using ANSI/ESD STM11.12
- Electrostatic decay performance per Mil-STD-3010C
- Proper marking and traceability information
- Documentation of test results from qualified laboratories
Don't rely solely on Technical Data Sheets for compliance verification.
You'll need traceable in-house or third-party test data that demonstrates adherence to the required standards.
Each package must include markings that trace back to the manufacturer and specific production lot codes.
Remember that testing at ambient conditions won't meet compliance requirements – you must conduct all validation procedures under the specified environmental parameters to verify reliable results and maintain the integrity of your ESD-sensitive devices within the EPA.
Packaging Performance Verification
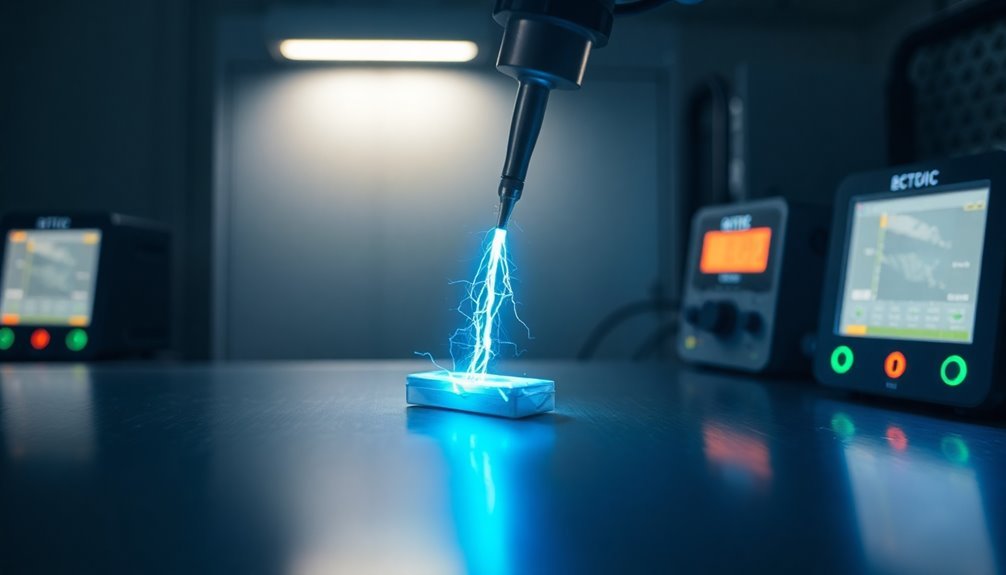
Maintaining quality control through performance verification stands out as a critical process in ESD-safe packaging manufacturing. You'll need to guarantee your packaging materials meet specific performance criteria through rigorous testing under controlled environmental conditions of 12%±3%RH and 73±50F.
To verify your packaging's performance effectively, you must test surface resistance against relative humidity changes and measure ESD withstand voltage. You'll want to use calibrated, lab-grade equipment and follow standardized simulation methods, including human body model and machine model electrostatic discharges. Remember that testing should run for a minimum of 48 hours to guarantee reliable results.
You can't overlook the importance of periodic verification of incoming materials to prevent counterfeit products or material substitution. Make sure you're working with accredited ESD laboratories that can provide thorough documentation of test results.
You'll need to maintain traceability through proper marking and lot code information. By integrating these verification processes into your product lifecycle management, you'll guarantee continuous protection and compliance with industry standards like ANSI/ESD S541 and IEC 61340-5-1.
This systematic approach helps prevent costly recalls and repairs while maintaining your packaging's protective integrity.
Industry Certification Process
Successfully maneuvering the ESD certification process requires working closely with accredited testing laboratories and standards organizations like ANSI and ESDA.
You'll need to guarantee your packaging materials meet specific standards, including ANSI/ESD S541 and ANSI/ESD S11.4 for static control bags. Testing must occur under controlled conditions of 12%±3% relative humidity and 73°F±5°F for at least 48 hours.
When selecting a testing laboratory, you'll want to verify its legitimacy and accreditation. Use Google Earth to confirm the facility's location and ascertain they're using properly calibrated, lab-grade equipment.
The lab will conduct human body model electrostatic discharge simulations to assess your packaging's performance.
Key requirements for successful certification include:
- Maintaining consistent environmental conditions throughout testing
- Using calibrated testing equipment that meets IEC 61000-4-2 standards
- Following proper documentation procedures for all test results
- Conducting regular verification and periodic testing
- Working with vetted ESD test labs for credibility
Remember that certification isn't a one-time event – you'll need to maintain compliance through regular testing and verification.
This ongoing process helps guarantee your packaging continues to meet industry standards and protects sensitive components effectively.
Testing Documentation Requirements
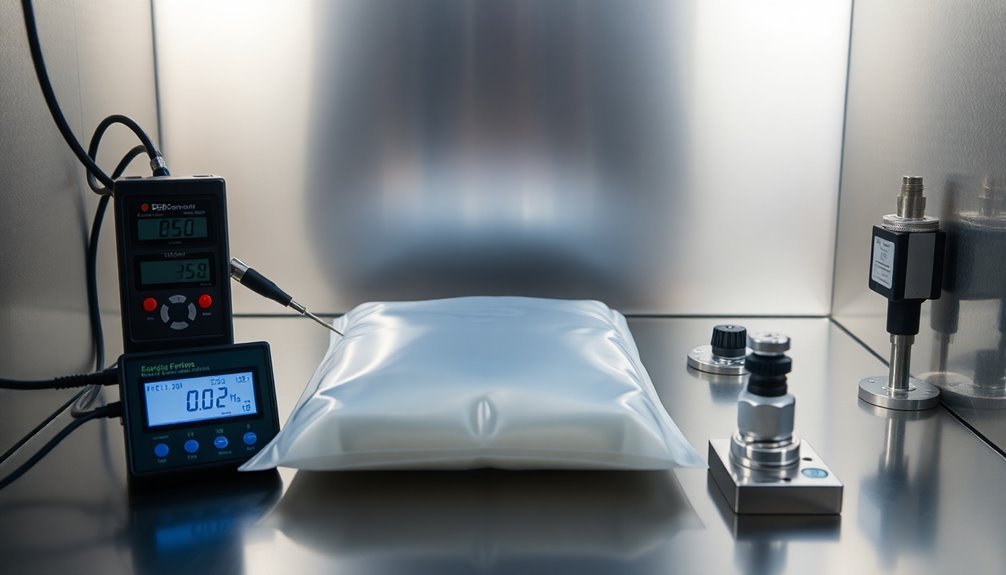
Documentation requirements for ESD safe packaging must follow strict protocols and industry standards to guarantee compliance and traceability. You'll need to maintain detailed test reports that include waveform analysis and test point mapping while ensuring all packages contain proper identification markers, lot codes, and handling instructions.
Documentation Type | Required Elements |
---|---|
Test Reports | Waveform data, environmental conditions, test points |
Traceability Info | Manufacturer details, date codes, lot numbers |
Inspection Records | Regular checks, replacement schedules, findings |
Compliance Certs | Standard conformity, testing facility details |
Audit Records | Testing history, inspection logs, replacements |
You must conduct testing under specific environmental conditions (12%±3%RH and 23°C±3°C) for at least 48 hours, using specialized ESD simulators and current probes. Your documentation should include performance evaluations after discharge events and detailed material selection criteria. Don't forget to maintain thorough records of storage conditions and handling procedures. Remember that proper documentation isn't just about meeting regulations – it's essential for product safety and quality control throughout the entire lifecycle of ESD packaging materials.
Frequently Asked Questions
How Long Does a Typical ESD Bag Retain Its Protective Properties?
You can expect your ESD bags to maintain protective properties for up to 5 years when stored properly. However, you'll need to store them away from heat, moisture, and sunlight, while following FIFO inventory practices.
Can ESD Bags Be Reused Safely After Initial Component Removal?
You can safely reuse ESD bags if they're undamaged and pass integrity checks. Make sure to inspect for tears, punctures, or weak spots before reusing. Don't reuse bags with visible damage or excessive wrinkles.
What Causes Pink-Poly ESD Bags to Change Color Over Time?
Your pink-poly ESD bags change color due to exposure to UV light, temperature variations, humidity, and chemical interactions. These factors break down the antistatic coating and pigments in the bag's material over time.
Do Generic ESD Bags Provide the Same Protection as Branded Ones?
No, you can't rely on generic ESD bags for equal protection. They often lack proper testing, use inferior materials, and don't maintain consistent performance. You'll get better, more reliable protection from branded ESD bags.
How Do Temperature Extremes During Shipping Affect ESD Bag Performance?
You'll find that extreme temperatures can degrade your ESD bag's protective properties, causing material deterioration and affecting static dissipation. Hot and cold conditions also impact moisture levels, potentially compromising your device's safety during shipping.
In Summary
You'll find laboratory testing essential for ensuring your ESD safe packaging meets all required standards and performs reliably. Through rigorous testing protocols, material verification, and quality control measures, you're protecting sensitive electronics from costly damage. Don't skip these critical evaluations – they're your safeguard against ESD-related failures and help maintain your compliance with industry regulations while providing documented proof of your packaging's effectiveness.
Leave a Reply