Static control protection is essential for your automotive parts because static electricity can severely damage sensitive electronic components like ECUs, circuit boards, and battery management systems. You'll find that uncontrolled static discharge poses risks during manufacturing and assembly, potentially causing both immediate and latent damage that affects critical safety systems like airbags and ABS brakes. Modern vehicles rely heavily on electronics that must meet strict standards, including protection against discharges up to 8kV. With automotive manufacturers facing billions in static-related losses annually, proper static control isn't just about protection—it's about ensuring your vehicle's reliability and safety. There's much more to discover about keeping your car's crucial systems protected.
Understanding Static Electricity in Manufacturing
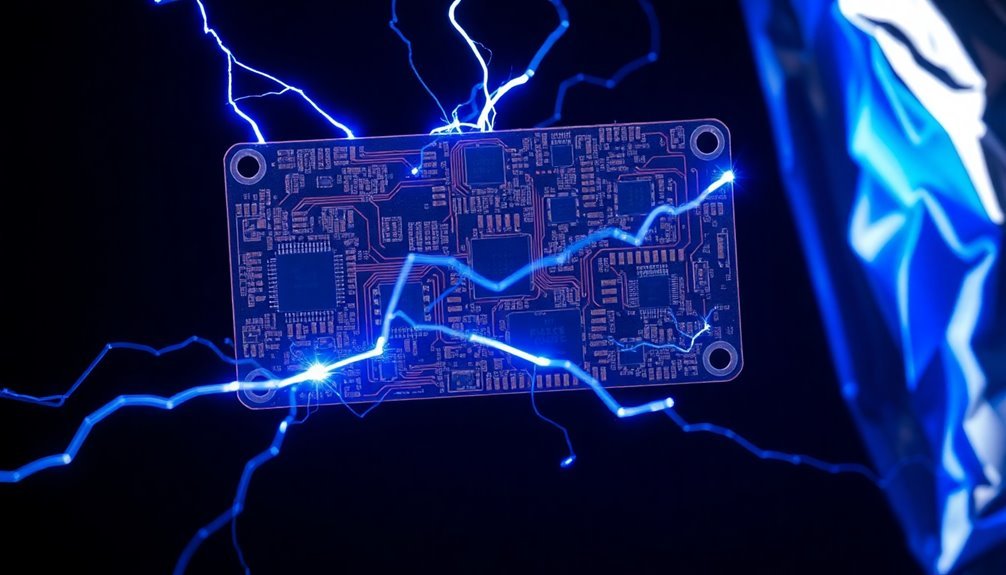
Static electricity lurks as an invisible threat in manufacturing environments, particularly where automotive parts are produced. When you're working with automotive components, static charges can build up through various manufacturing processes that involve contact and separation between materials, especially during operations that use rollers or require frequent material handling.
You'll find that static electricity doesn't just come from one source. It develops when materials undergo rapid temperature changes, such as passing through heating ovens, and during cutting operations like slitting and trimming. Clean production areas are critical since static charges can attract dust and contaminate surfaces.
Even your workers can generate static charges simply by standing in a static field and touching grounded equipment. The consequences can be severe – from equipment malfunctions and damaged electronics to quality control issues caused by dust attraction. This is especially critical in plastic component manufacturing where static buildup occurs naturally during cooling processes.
What makes static control particularly vital in automotive manufacturing is its potential to cause multiple problems simultaneously. You're not just dealing with the risk of electrostatic discharge damaging sensitive electronic components; you're also facing potential fire hazards when static sparks occur near flammable materials.
Understanding these basics helps you recognize why implementing proper static control measures isn't optional – it's essential for maintaining both quality and safety standards.
Critical Automotive Components at Risk
Critical automotive components, such as electronic control units and circuit board assemblies, need robust static protection to prevent costly failures and safety risks.
You'll find these sensitive components throughout modern vehicles, from engine management systems to advanced driver assistance features, making proper ESD safeguards essential at every stage of manufacturing.
Battery management systems require particular attention since static discharge can compromise their performance and potentially create hazardous conditions in electric and hybrid vehicles.
Using permanent static control additives like inherently dissipative polymers ensures long-lasting protection against static buildup in automotive parts.
Production facilities must implement comprehensive static systems including anti-static floors and specialized clothing to ensure component integrity during assembly.
Sensitive Electronic Control Units
Anyone who works with automotive electronics knows that Electronic Control Units (ECUs) represent some of the most ESD-sensitive components in modern vehicles. These critical units contain vulnerable microcontrollers and integrated circuits that can suffer immediate or latent damage from static discharge. Meeting IEC 61000-4-2 standards requires ECUs to withstand at least 8kV contact discharge.
You'll find ECUs controlling everything from your vehicle's airbags to its braking systems, making their protection essential for both performance and safety. Dashboard warning lamps may activate due to circuit damage, impacting driver confidence in vehicle quality.
When you're handling ECUs, you need to implement thorough static control measures to prevent costly failures and warranty claims. This includes using anti-static materials, maintaining proper grounding systems, and ensuring physical isolation of sensitive components.
You'll want to incorporate protection devices like TVS diodes and polymer-based solutions into your manufacturing and handling processes.
To maintain compliance with ISO 10605 standards, you must regularly test and audit your ESD protection systems. Don't forget to train your personnel on proper handling procedures and best practices.
Installing static monitoring systems will help you detect potential issues before they cause damage. Remember that ESD-related failures in ECUs aren't always immediate – they can develop over time, leading to unexpected malfunctions that could compromise vehicle safety and reliability.
Circuit Board Assembly Protection
During assembly, circuit boards in automotive applications face constant ESD threats that can compromise their functionality and reliability.
Static electricity poses severe risks in electronic manufacturing, with latent damage potential often going undetected until component failure occurs.
You'll find that surface mount technology (SMT) production lines are particularly vulnerable to static electricity, with risks present throughout the manufacturing process from component handling to final assembly.
To protect these sensitive components, you'll need thorough static control measures. These include anti-static floors, specialized clothing, and ionization devices strategically placed throughout your production area.
You must guarantee that your assembly stations are equipped with static discharge units and that your employees use proper anti-static gear when handling electronic components.
Your circuit board protection strategy should incorporate automotive-specific ESD protection devices, such as TVS diodes and discrete components that meet IEC 61000-4-2 standards.
You'll need to integrate these protective elements directly into your circuit board designs while ensuring compliance with ISO 10605 requirements for automotive ESD immunity testing.
Regular monitoring and testing of your static control systems isn't optional – it's essential for maintaining the integrity of your automotive electronic components.
Battery Management System Safety
Battery management system safety stands at the forefront of automotive electronics protection, where static discharge events can severely impact vital monitoring and control functions.
You'll find that BMSs rely heavily on sensitive electronic components to monitor battery parameters like voltage, current, and temperature in real-time, making them particularly vulnerable to static damage.
Your BMS's protection mechanisms, including overcurrent prevention and voltage regulation circuits, can fail if static discharge compromises their integrity.
When these safety features are compromised, you're risking thermal runaway conditions, improper cell balancing, and potential battery failures.
The system's thermistors and sensors, which are essential for maintaining safe operating temperatures, can also be rendered inaccurate or non-functional by static events.
To maintain compliance with automotive safety standards like ISO 26262 and ASIL C, you'll need robust static protection measures throughout your BMS design.
Modern simulation tools help validate static protection designs before implementation, significantly reducing development costs and potential failures.
This includes protecting the monitoring circuits, communication interfaces, and control systems that manage your battery's state of charge and health.
Remember that your BMS's ability to prevent hazardous conditions depends entirely on the proper functioning of these electronic components, making static control a vital aspect of automotive safety.
The continuous self-correction features of modern BMS help maintain prediction accuracy for battery performance even when facing potential static-related disruptions.
Impact on Vehicle Safety Systems
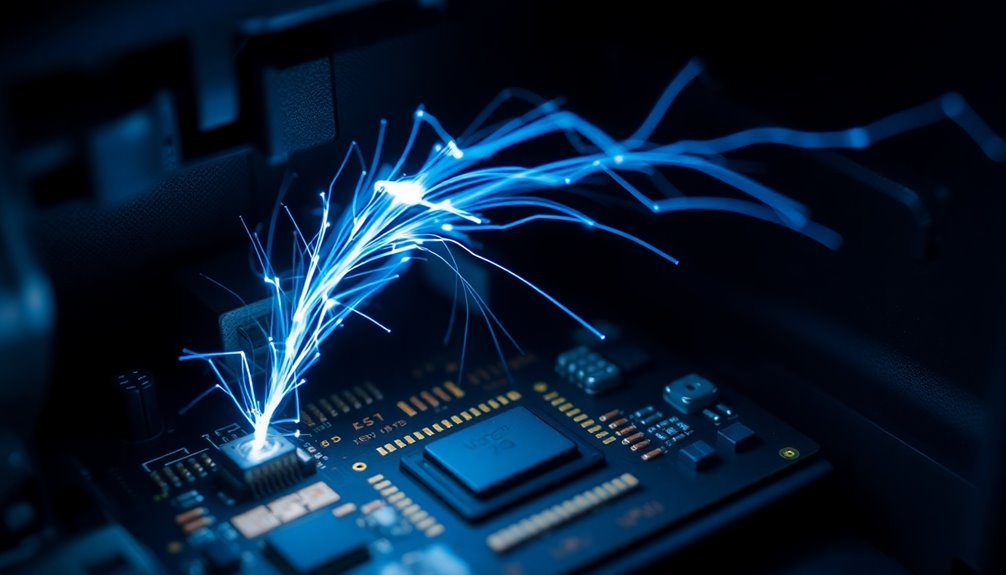
Your vehicle's safety systems need robust static control measures to prevent component failures that could compromise critical functions like ABS and airbag deployment.
You'll find that proper ESD protection involves multiple layers of defense, including TVS diodes and specialized silicon devices that shield sensitive electronics from dangerous discharge events.
When you're maintaining your vehicle's safety systems, it's crucial to verify all ESD protection devices are functioning correctly to maintain system reliability and prevent potentially dangerous malfunctions during operation.
High-speed assembly of automotive components requires careful static management to prevent process errors that could affect safety system integrity.
Component Failure Prevention Strategies
Within automotive manufacturing, protecting sensitive electronic components from static discharge requires extensive prevention strategies, especially for safety-critical systems.
You'll need to implement multiple layers of protection to safeguard these essential components from ESD damage that could compromise vehicle safety.
To prevent component failures, you must install ionization equipment like fans and ion bars throughout your manufacturing facility.
You'll also need to make certain your workers wear ESD-safe clothing and PPE to prevent static buildup during assembly.
It's imperative to implement anti-static flooring and maintain thorough static monitoring systems to track potential risks.
For enhanced protection, you should incorporate TVS diodes and specialized silicon and polymer devices that meet IEC 61000-4-2 and ISO 10605 standards.
You'll want to use static control additives in plastic components, choosing between permanent or temporary solutions based on your specific needs.
Don't forget to use inert gases in sensitive manufacturing processes to prevent static-induced sparks.
Regular testing of components for ESD immunity verifies your prevention strategies are working effectively and maintaining the reliability of safety-critical systems like airbags, ABS, and electronic stability control.
System Reliability Under Discharge
Understanding system reliability under static discharge conditions is essential when evaluating vehicle safety systems.
You'll find that uncontrolled static discharge can severely compromise critical safety components, including airbags and anti-lock braking systems. When ESD damages sensitive electronic components, it often creates latent failures that won't show up immediately but can lead to dangerous system malfunctions over time.
Your vehicle's electronic components are particularly vulnerable due to their miniaturized nature, and they must meet strict IEC 61000-4-2 immunity requirements.
These components need robust ESD protection devices to maintain system integrity and prevent electrical overvoltage damage that could affect your safety.
Here's what you need to know about system reliability risks:
- Static discharge can cause immediate or delayed damage to safety-critical systems
- Modern semiconductor components are increasingly susceptible to ESD damage
- Vehicle safety systems require continuous, reliable operation to protect occupants
- Latent failures from ESD may not be immediately detectable during testing
- Protection devices must meet international safety standards for automotive use
You'll want to guarantee your vehicle's electronic systems have proper ESD protection to maintain long-term reliability and safety performance.
Static Control Solutions for Automotive
Static control solutions play an important role in modern automotive manufacturing, protecting both product quality and worker safety. You'll find various specialized equipment designed to address static-related challenges throughout the production process, from injection molding to final assembly.
To combat contamination issues, you can implement air knives and blow-off systems that effectively clean and dry both flat and contoured surfaces. For painting and coating operations, you'll need ionizing guns to guarantee surfaces remain clean and static-free.
Bar ionizers and nozzle ionizers provide versatile solutions across different manufacturing stages, while anti-static fittings and vacuum pads help you safely handle sensitive components.
When you're dealing with small to medium-sized parts, ion boxes offer a dual benefit by combining static neutralization with dust removal. These solutions are particularly vital in plastic extrusion and molding processes, where static charges can greatly impact product quality.
You'll need to implement these controls throughout your production line to prevent machine jams, part sticking, and product defects. By incorporating thorough static control measures, you're not only improving product quality but also creating a safer working environment for your operators.
Supply Chain Static Protection Measures
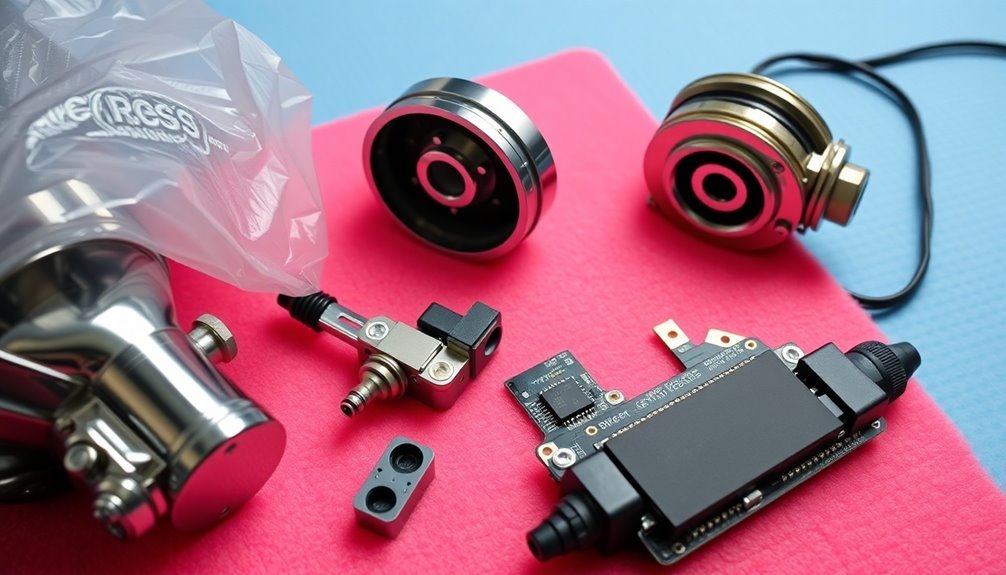
Building on effective factory-floor static control, extensive protection measures must extend throughout the automotive supply chain. You'll find thorough static protection systems implemented across multiple manufacturing stages, from electronic components to plastic parts production. These measures guarantee your automotive parts maintain their quality and functionality throughout the entire production process.
In electronics manufacturing, you'll see anti-static floors, specialized clothing, and ion bars working together to prevent static buildup. For plastic components, static neutralization systems help prevent contamination during extrusion and molding processes. You'll also find ESD protection devices safeguarding sensitive automotive electronics, particularly in CAN lines and high-speed assembly operations.
- Install ionizing fans before SMT machine entry points to eliminate static charges
- Use anti-static materials in packaging and conveyor systems
- Implement static monitoring systems throughout production lines
- Apply ESD protection devices that comply with ISO 10605 standards
- Maintain static control in cleanroom environments for quality assurance
Through these supply chain protection measures, you're guaranteeing that static doesn't compromise your automotive parts' integrity from manufacturing through final assembly and packaging.
These controls work together to prevent contamination, reduce rejection rates, and maintain product quality standards.
Cost Implications of Static Damage
The financial toll of static damage adds up to a staggering $5 billion annually across American industries, with automotive manufacturers bearing a significant portion of these losses. When you're dealing with static electricity damage, you'll face both immediate and long-term costs that can severely impact your bottom line.
You'll find that catastrophic failures, while expensive, aren't your biggest concern. It's the latent damage that poses the greatest financial threat, as these hidden defects often surface after your products have reached customers.
You're not just looking at component replacement costs; you're also facing expenses for labor, shipping, customer service, and potential warranty claims.
In today's automotive industry, where vehicles contain increasingly sensitive electronic components, you can't afford to overlook static protection. A single damaged circuit board can cost thousands to replace, and that's before you factor in operational downtime and lost productivity.
What's more, your reputation's at stake – repeated failures due to static damage can erode customer trust and lead to lost business. By implementing proper static control measures, you'll protect both your assets and your company's standing in the market.
Meeting Automotive Industry Static Standards
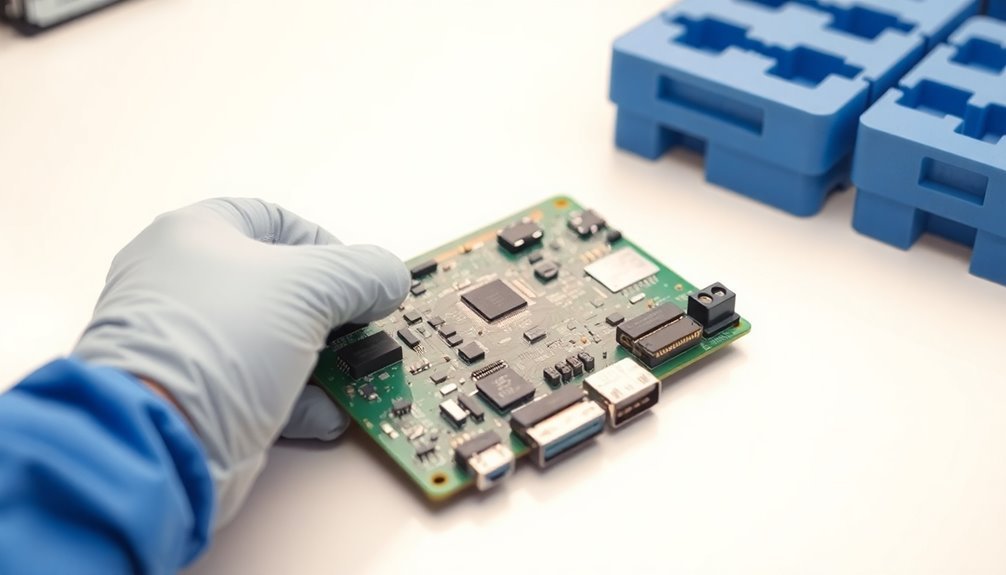
With financial losses mounting from static damage, understanding and meeting industry standards becomes your first line of defense.
You'll need to comply with key standards like IEC 61000-4-2, which requires ±8kV contact discharge protection, and ISO 10605, which tests for discharges up to 25kV in automotive environments. Your components must withstand these rigorous requirements to guarantee safety and reliability.
To meet these standards, you'll need to implement thorough static control measures across your manufacturing processes. This includes using TVS diodes for circuit protection, installing ionizing fans on SMT lines, and guaranteeing proper anti-static flooring and clothing for your workers.
Key standards you must meet:
- Level 4 ESD immunity compliance for all automotive electronic components
- Implementation of ESD-safe workstations with proper grounding
- Regular testing and monitoring of static control equipment
- Use of certified anti-static materials in component packaging
- Documentation of ESD control programs and test results
Your compliance strategy should focus on both prevention and protection, integrating physical safeguards with proper testing protocols.
Remember that component miniaturization makes proper ESD protection even more critical for modern automotive electronics.
Frequently Asked Questions
How Long Do Anti-Static Treatments Typically Last on Automotive Components?
You'll find permanent anti-static treatments like Ionphase IDPs last indefinitely, while short-term solutions like Atmer additives provide protection for up to 12 months, depending on your specific automotive component requirements.
Can Extreme Weather Conditions Affect Static Control Measures in Vehicles?
Yes, extreme weather greatly affects your vehicle's static control. You'll notice reduced effectiveness in very dry conditions, while high humidity can alter conductivity. Temperature extremes can also compromise protective measures and materials.
What Percentage of Automotive Recalls Are Related to Static Electricity Damage?
You won't find an exact percentage of static-related automotive recalls in current data. While static damage contributes to recalls, manufacturers don't typically isolate this as a specific cause in their reporting.
Do Hybrid and Electric Vehicles Require Different Static Protection Than Conventional Cars?
Yes, you'll need enhanced static protection for hybrid and electric vehicles due to their higher voltage systems, increased electronic components, and greater use of static-sensitive parts compared to conventional combustion engine cars.
How Often Should Static Control Equipment Be Calibrated in Manufacturing Facilities?
You'll need to calibrate static control equipment daily for basic checks, monthly for high-risk areas, and annually for thorough audits. Don't forget to perform additional calibrations after major process changes or equipment modifications.
In Summary
You'll need to prioritize static control protection throughout your automotive parts manufacturing and handling processes. If you don't implement proper safeguards, you're risking damage to sensitive electronic components that could lead to costly recalls and safety issues. By following industry standards and maintaining static protection across your supply chain, you're ensuring vehicle reliability while protecting your bottom line and brand reputation.
Leave a Reply